効果的な調達システムの組織化とサプライヤーとの生産的な作業。
「要求される品質の範囲内で最低価格のサプライヤーの選択をやめる前提条件は、忠誠心と信頼に基づいて、単一の材料について単一のサプライヤーと長期的なパートナーシップを形成するというコミットメントでなければなりません。」
記事への自由なアクセスは、記事に含まれる資料の価値を決して減じるものではありません。
ポイント4。 E. デミング博士の管理のための 14 のポイント プログラム 読みます:
「最安値で購入する習慣をやめましょう。
購入する製品の品質を示す指標がなければ、価格は意味がありません。 1 。適切な品質基準がなければ、注文は最低価格を提供するサプライヤーに送られることになり、必然的に品質が低くなり、総コスト(消費と使用の総コスト - S. グリゴリエフのメモ)が高くなります。米国の産業界と米国政府、さらには文民機関や軍事機関も、最も低価格のサプライヤーを選択することを義務付ける規則に惑わされている。
工具や機器を購入する際の目標は、耐用年数全体にわたって、時間 (または年) あたりの作業コストの合計を最小限に抑えることです。しかし、これには、現在の最安値で購入する方が簡単な場合、長期的な思考が必要になります。すべての重要な機器の初期コスト、運用コスト、耐用年数に関する必要なデータはすでに存在しており、さまざまな情報源から分散していますが、収集することができます。現在使用するためのそのようなデータの自動収集は、今日の重要なプロジェクトの 1 つです。
これまで、サプライヤーの任務は、より低い価格を提示する売り手を見逃さないように警戒することでした。そして、同じ素材の他の販売者も値下げを余儀なくされています。
サプライヤーに責任はありません。これは過去 20 年間の彼の仕事です。彼が仕事をしたことを責められますか? 時代遅れの調達ルールを維持している責任は経営陣にあります。
材料の品質やサービスのレベルに関係なく、すべての購入価格を継続的に引き下げることを目的とした政策は、成功した販売者やサービス会社の破産につながる可能性があります。
最低価格のサプライヤーを選択する方針を持つ人は騙されて当然です。」
次に、エドワーズ・デミングが挙げた例を紹介します。これと同様の例は、ロシアの産業やサービス部門にも十分にあります。
「ある小さな靴メーカーは、レンタル料が非常に高価なミシンをスムーズに稼働させるのに苦労していました。オペレーターはマシンのスレッドをやり直すために多くの時間を無駄にしており、これは大きな無駄でした。
重要な点は、すべての機械とすべてのオペレーターにとって問題が共通であるということでした。検査の結果、問題の原因は、工房のオーナーが節約の誘惑に負けて購入した低品質の糸であることが判明しました。機器のダウンタイムによる損失は、使用できなくなったスレッドの購入による仮想損失を数百倍も上回りました。スレッドの投入価格が高価な罠であることが判明しました。
これは、品質や性能を考えずに低価格に誘惑されて、どのようにぼったくりをするかの一例です。
より高品質のスレッドにより問題は解決しました。
この変更を実行できるのは経営陣だけです。オペレーターは、たとえ問題が何であるかを理解したとしても、仕事を辞めてより良い糸を購入することはできませんでした。それらはシステム内で動作します。スレッドもその一部でした。
これらの単純かつ日常的だが効果的な研究が行われる前は、所有者はすべての問題はオペレータの経験不足と不注意に起因すると信じていました。」
以下はロシアの実践例です。
「2015年を振り返ると、総局の仕事の結果は良好だったと言えます。商品、資材、サービスの調達コストの削減は、7,000万ルーブルの計画に対して、1億6,700万ルーブルに達しました。」と局長は述べています。イゾラ工場での購買と物流の管理。
イゾラ工場とOMZグループの企業シュコダJS(チェコ共和国)との共同作業により、ChTPZが製造する六角形(シームレス - セルゲイ・P・グリゴリエフ注)ボロンパイプの独占供給から逃れ、使用することが可能になりました。コズロドゥイ原子力発電所(ブルガリア)の機器製造用の溶接六角パイプにより、大きな経済効果を達成することができました。」
購入コストを削減するという目標値は、どのような生産物にとっても危険な数値目標であり、原子力発電所の機器メーカーにとってはなおさらです。
また、シームレスパイプを溶接パイプに交換することが有能な技術専門家によって合意された場合、交換の効果は数年間の運用結果によってのみ判断できます。しかし、その時はすでに手遅れかもしれません。
仕様は供給される材料のすべての要件を考慮しているわけではなく、サプライヤーによる継続的な改善を必要としません。
「技術仕様を遵守するだけでは十分ではありません。
唯一のサプライヤーに突然一時的な問題が発生したり、永久に廃業したりした場合に備えて、2 番目のサプライヤーを追加するのは高価なポリシーです。
買い手との短期的な関係にしか依存できないサプライヤーは、どのようにして生産プロセスを革新し、コストを削減できるでしょうか?
クライアントとサプライヤーの両方がシステムの最適化に最善を尽くしている限り、単一のサプライヤーと長期的な関係を築くのは賢明な決定です。
購買部門のマネージャーは、この技術革新 (単一の運送業者) により、サービスの低下や無責任のリスクを伴いながら、安い輸送手段を常に探し続けるという重荷が肩から降ろされたと語った。彼女は空いた時間を有効に活用しました。
サプライヤーには、価格ではなく、合理的な基準を満たす能力に基づいて、同社の唯一のサプライヤーになるために競争する機会が与えられなければなりません。
単一ベンダーのバッチ間の変動は、通常、機器の調整が必要になるほど大きくなります。 2 つのサプライヤーのバッチ間の変動により、さらに多くの問題が発生することが予想されるのは当然です。
リーダーたちに理解してもらいたいことを一言でまとめると、これは「すべては変動性を減らすことだ」ということになるでしょう。」
単一の配送拠点を持つ単一のサプライヤーに移行することのメリットは非常に大きく、ここではその一部を紹介します。
- 文書のフローと承認、登録、購入と決済の実行にかかる時間が短縮されます。
- 調達、物流、倉庫保管、生産に関わる人々の作業を簡素化し、同時にそのような作業の品質を向上させる。
- 納品不足、低品質の教材の納品、遅延、採点ミスのリスクを軽減します。
「突然 1 つのサプライヤーに切り替えることはお勧めできません。それはかなり危険なステップです。ゆっくりしてください。強い関係を築かなければなりません。
消費者は原材料よりも重要です。通常、新しい顧客を見つけるよりも、原材料のサプライヤーを変更する方がはるかに簡単です。そして、あなたの顧客ではない、あなたの製品をまだ試したことのない人は、あなたの製品の追加ユーザーとなる可能性があるため、あなたにとってさらに重要です。
値札は読みやすいですが、品質を理解するには教育が必要です。購買部門は、購入する材料の最低価格の追求から、最低の総コストの達成に焦点を移す必要があります。
つまり、購買マネージャーという職業には特別な教育が必要であるということです。」
ただし、サプライヤーの代表者の保証だけに頼らないでください。
「会議室での約束には気をつけてください。」
サプライヤーの能力の単純な宣言に依存するのではなく、お客様に供給される製品および関連サービスの品質の統計的証拠 (プロセスの統計的に管理された状態と、いくつかの合理的な基準や仕様を満たす能力の実証) を要求します。統計データがない場合は、簡単な統計手法を使用して収集と分析を開始します。サプライヤーとパートナーシップを確立することで、サプライヤーのサプライヤーとのサプライ チェーン管理を組織化することができます。
サプライヤーとこのような取り組みを開始するための最良のインセンティブは、次のようなものを使用することです。 ソフトウェア これは、サプライヤー側の製品の品質の統計的確認を実証することができ、消費者は、受け取ったバッチからの少量のサンプルに基づいてサプライヤーの声明を確認または反論することができます。このようなやり取りは空虚な保証ではなくデータに基づいており、サプライヤーのプロセスについて取得した知識を、その製品の品質、ひいては自社製品の品質の向上に使用できるようになります。
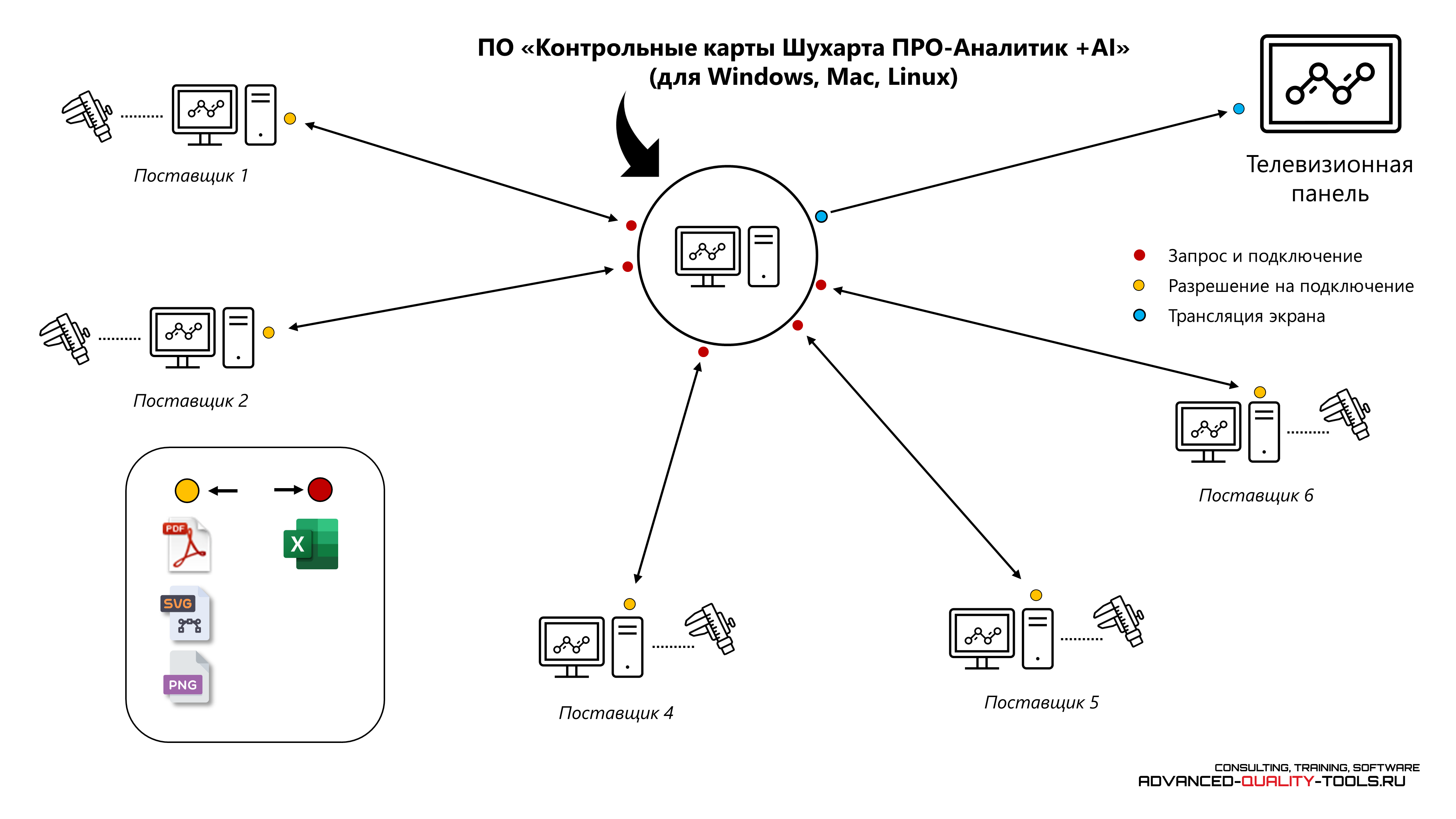
米。供給された材料とコンポーネントの統計的品質管理のためのデータ交換の組織化の概略図。
さらに、供給された原材料と供給品の品質管理のこの方法により、購入した材料の品質とサプライヤーの品質の状況について、実際に得られるものよりも優れたアイデアが得られます。 選択受入検査テーブル 品質またはその他の受入管理措置。
エドワーズ・デミングは、クライアントの一人の優れたパフォーマンスについて次のように述べています。
「私のクライアントの 1 つの購買部門は、3 年間で次のような成功を収めました。
- 現在、20 の部品のうち 1 部品のみが 2 つ以上のサプライヤーを持っています。 (20 分の 1 は、おそらく削減不可能な最小値に近いです。)
- 1年前、その割合は16人に1人だった。
- 2年前 - 12人に1人。
- 3年前 - 2つのうちの1つ。」
自分でやるのか、それとも買うのか?
サプライヤーが上記の基準を満たしている場合、そのサプライヤーはパートナーとなり、特別なリスクを負うことなく、供給された材料のシェアを増やすことができます。この場合、検討中のシステムの境界が拡大しているため、両社の経営陣はより広範な新しいシステムの最適化を開始する必要があります。
「日本の自動車メーカーは、必要なプレス加工の(金額ベースで)70~80%を製造会社から契約に基づいて購入し、残りの20~30%を自社で製造している。米国では、すべてがまったく逆のことが起こります。
日本の自動車メーカーは、製品を自社で生産するよりもアウトソーシングすることで、購買部門が品質、納期規律、在庫、相対コストを管理しやすくなると考えているようです。」
結論
追加できるサプライヤーを選択するための基準をいくつか用意しました。
- サプライヤーと協力すると、売上高が増加し、会社の在庫を減らすことができます。たとえば、配送ロットを最小限に抑えながら、配送頻度を増やします。
- サプライヤーと企業の企業情報システム間での文書 (申請書、納品書、運送状など) の相互電子交換を組織する機能。
- サプライヤー側と企業側の新材料の開発とテストには、当事者の代表者が共同で参加することが規定されています。
- 会社が必要とする追加のサプライヤー サービスの利用可能性。
- 1 つのサプライヤー – 1 つの出荷地点 – 1 つの運送会社 (最適なターゲットとして)。
- 新しいサプライヤーには、企業の生産プロセス全体、組み立て、輸送、消費者でのテストを経る必要がある少量の試用バッチが提供されます。推定値の統計的有意性 (客観性) を得るには、少なくとも 7 回のそのような配信から情報を収集する必要があります。
- 現在のサプライヤーからの材料使用の全コストに関するデータの収集と分析を開始します (輸送および保管中の損失、供給品のグレードミスによる損失、材料の加工コスト、顧客に納入される製品の材料使用による損失など)。
- 資材の出荷ごとに、サプライヤーに重要な品質指標の管理図を提供するよう依頼してください。担当者にそのような知識がない場合は、従業員をサプライヤーに派遣し、従業員を訓練してください。これにより、選択可能な全か無かの入力検査計画を実装して、施設内の平均総検査コストと欠陥入力による損失を最小限に抑えることができます。
- 前の段落を考慮して、受け入れサンプリングの実行にスプレッドシートを使用することは避けてください (変換の障害の 1 つ)。
- 会社が必要とするサービスや資材を提供する能力、会社や他の顧客の既存の需要を満たすサプライヤーの能力と能力。
- 企業のニーズに対する柔軟性、企業のニーズへの理解と対応力。
- サプライヤーの信頼性と以前の仕事の経験。
- 資金の借り手としてのサプライヤーの評判 (主に銀行間)。 [3]
- このサプライヤーとそのサプライヤーとの関係。彼らは幸せですか、それとも意見の相違の兆候はありますか? [3]
- 特定のサプライヤーが顧客として貴社を重視する重要性。あなたの会社は彼のビジネスのほんの一部ではないでしょうか? [3]
- 適切なアフターサービスの提供と品質。
- サプライヤーが研究開発のために割り当てた資金の額。
- 開発成功の経験。 (ゼネラルモーターズのノーバート・ケラー氏の提案。)
- 材料の価格を長期間、たとえば最長 1 年間固定します。
-
サプライヤーは継続的な改善に対する責任を負います。 14 の管理ポイント、特にポイント 5 におけるサプライヤー管理者の関与の証拠を要求します。障害や病気の克服とともに、すべてのプロセスを改善します。