オール・オア・ナッシング計画は、ランダムな品質受入検査にテーブルを使用することに反対している。エドワーズ・デミング
「受け入れサンプリング検査テーブルの使用は、入荷する材料の検査にかかる平均総コストと、欠陥のある材料が生産に入る可能性を最小限に抑えるためには適用できません。」
引用資料の出典: [2] - W. Edwards Deming, “Out of the Crisis” (「Out of the Crisis」、W. Edwards Deming - M.: Alpina Publisher、2017。科学編集者 Y. Rubanik、Y. Adler) 、V. シュパー)。出版社から本を購入できます アルピナ出版社 。
この記事は、AQT センターの科学ディレクターによって作成されました。 セルゲイ・P・グリゴリエフ
記事への自由なアクセスは、記事に含まれる資料の価値を決して減じるものではありません。
序文
入荷した荷物に含まれる欠陥品の一部またはすべてを拒否する必要がありますか?それとも、検査を回避してすべてのバッチをそのまま生産に送り込むべきでしょうか?経済的に健全な解決策は、エドワーズ・デミングが提案した、入荷する原材料、材料、およびコンポーネントの「オール・オア・ナッシング」管理計画を使用することです。
いずれの場合も、当社が製造した要件を満たさない製品が当社の購入者に届くことはありません。
全か無かの入力制御ルールは、企業の生産単位あたりの平均総コストを最小限に抑えるために使用されます。 「オール・オア・ナッシング」ルールは、不良品の拒否を伴う原材料の入荷バッチの 100% 管理、または入荷管理なしでそのようなバッチを生産に投入し、その後に部品の交換と再加工を行うかどうかを決定するためのルールです。制御が入らないこのようなパスの結果として形成される欠陥製品の割合。
サンプリング管理のために原材料、材料、部品の受入検査を実行する場合は、次のことを知っておくとよいでしょう。
「入荷する材料の品質に対する統計的管理の程度が高い場合、サンプルの管理では、検査されたロットの残りの部分についての洞察が得られません。これは、この場合、サンプル間の相関関係の証拠が欠如しているためです。」
たとえば、ランダムな合格品質管理の表を使用したサンプリング管理では、管理されたバッチ内の欠陥製品の数を把握できないというエドワーズ・デミングの声明は実際に裏付けられています。 赤いビーズを使って実験する ここで、赤と白のビーズの混合物からのランダムな機械的サンプルは、毎回、制御された混合物中の実際の赤ビーズの割合とは異なる、より高いまたはより低い赤いビーズの割合の値を与えます。実験では、同じサイズのサンプルの赤いビーズの数の対照 np チャートを使用しました。
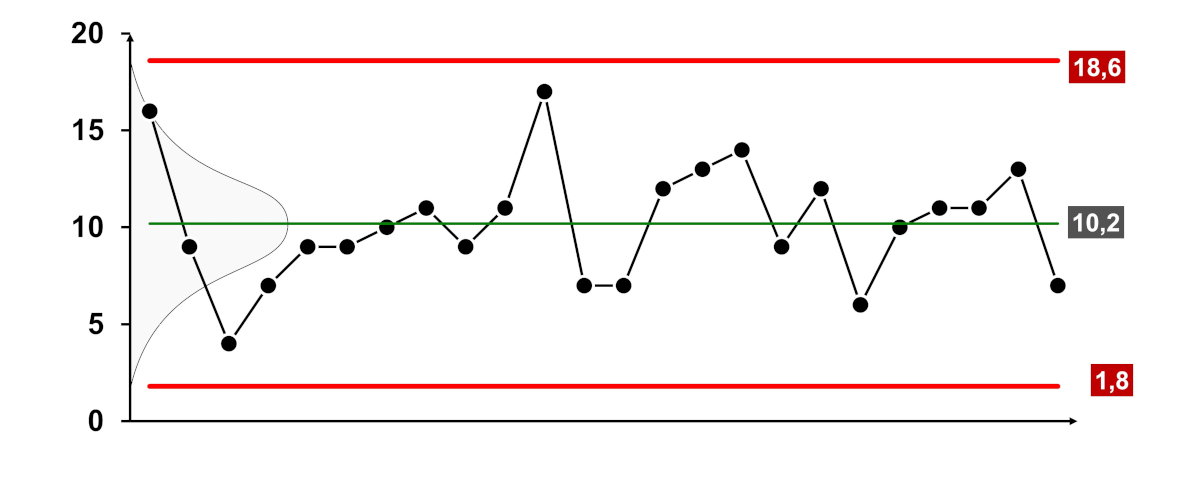
米。 1983 年にエドワーズ デミングが実施した赤いビーズ実験の対照 np チャート。
「総平均コストを最小限に抑えるためのルールは、条件によっては非常に簡単であることがわかります。
指定:
p は、入荷する部品バッチ内の欠陥製品の平均割合です。
k 1 - 一部の部品の受入検査にかかる費用。
k 2 - 生産に入った 1 つの欠陥部品により故障したユニットの分解、修理、再組み立て、再テストにかかるコスト。
条件1:
最悪の入荷ロットは、平均不良率 (p) が (k 未満) になります。 1 /k 2 )。
p<k 1 /k 2
この場合: 入力制御はありません。コンポーネントのテスト時点での検査に全面的に依存する必要があります。
説明、セルゲイ・P・グリゴリエフ:
条件 1 の式の導出、入荷したバッチから欠陥部品を含むすべてのユニットを修正するための総コスト (N×p×k) 2 ) は、入荷する部品 (N×k) をすべて 100% 検査するコストよりも低くなります。 1 )。
(N) - 入荷する部品のバッチのサイズ (個数)、不良品の割合 (p):
N×p×k 2 <N×k 1
式を次のように簡略化します。
p×k 2 <k 1
それから:
p<k 1 /k 2
条件2:
最良の入荷バッチには、不良品の割合 (p) が次の値より大きくなります。 (k 1 /k 2 )。
p>k 1 /k 2
この場合: 100% 入力制御。また、完成品の検査時点での管理も行います。
説明、セルゲイ・P・グリゴリエフ:
条件 2 の式の導出。入荷したバッチから欠陥部品を含むすべてのユニットを修正するための総コスト (N×p×k) 2 ) は、入荷する部品をすべて 100% 検査するコスト (N×k) よりも高くなります。 1 )。
(N) - 入荷する部品のバッチのサイズ (個数)、不良品の割合 (p):
N×p×k 2 >N×k 1
式を次のように簡略化します。
p×k 2 >k 1
それから:
p>k 1 /k 2
(k 1 /k 2 ) - 平衡品質、または平衡点。
(k 2 ) は常に大きくなります (k 1 );
したがって、比率(k 1 /k 2 ) は 0 と 1 の間になります。
条件 1 ルールを適用する必要がある状況で条件 2 ルールを適用すると、合計コストは最大になります。その逆もまた真です。」
例(セルゲイ・P・グリゴリエフ)
与えられる:
p (入荷する部品バッチ内の不良品の平均割合) = 0.05;
k 1 (1 つの部品の受入検査費用) = 100.00 ₽;
k 2 (生産に入った 1 つの欠陥部品により故障したユニットの分解、修理、再組み立て、および再テストのコスト) = 1,000.00 ₽;
投入ロット = 1,000.00 個
条件 1: p<k 1 /k 2 - 入場規制はありません。
条件 2: p>k 1 /k 2 - 100% 受信制御。
計算
p = 0.05
k 1 /k 2 = 100.00 ₽ / 1,000.00 ₽ = 0.10
0.05 < 0.10
p<k 1 /k 2 - 条件 1 - 入力制御なしに対応します。
解決
「制御なし」プランを選択します。
解決策の確認
入口で 100% 制御する場合のコストは次のとおりです。
1,000個×100.00₽=100,000.00₽
不良品を渡す場合のコストは次のとおりです。
1,000個×0.05×1000.00 RUR=50,000.00 RUR
したがって、欠陥部品を生産に投入する場合、この場合、生産に入った 1 つの欠陥部品により故障したユニットのその後の分解、修理、再組み立ておよびテストを行うと、コストは実際に 100% 受入検査₽よりも 50,000.00 安くなります。
「したがって、統計的管理の状態には明らかな利点があります。入ってくるバッチ フローが条件 1 または条件 2 を満たしているか、あるいは混沌に近い状態にあるかを知るには、できればサプライヤーの敷地内で、進行中の小規模サンプル試験 (いずれの場合も) に基づいて作成されたチャートを使用して、統計的管理と平均不良率を追跡するだけで済みます。」
実際に観察されたその他の条件 (エドワーズ・デミング)
統計的な制御可能性から中程度の偏差を持つ分布の中間位置。
ここでは、入荷ロットにおける不良品の割合の分布について 2 種類の中間状況を分析します。おそらく、独自の管理図、サプライヤーの管理図、または共同で管理する管理図を使用すると、分布のごく一部だけが均衡点の右側に位置することが予測できます。この場合、「ノーコントロール」ルールを採用できます。このルールにより、均衡点の右側にある分布の部分が小さい場合に限り、平均総コストの最小値に近づくことができます。
逆の状況: 入荷するバッチ内の不良品の割合の分布のごく一部だけが平衡点の左側にあります。これを知っていれば、受信バッチを 100% 制御するというルールを安全に受け入れることができます。
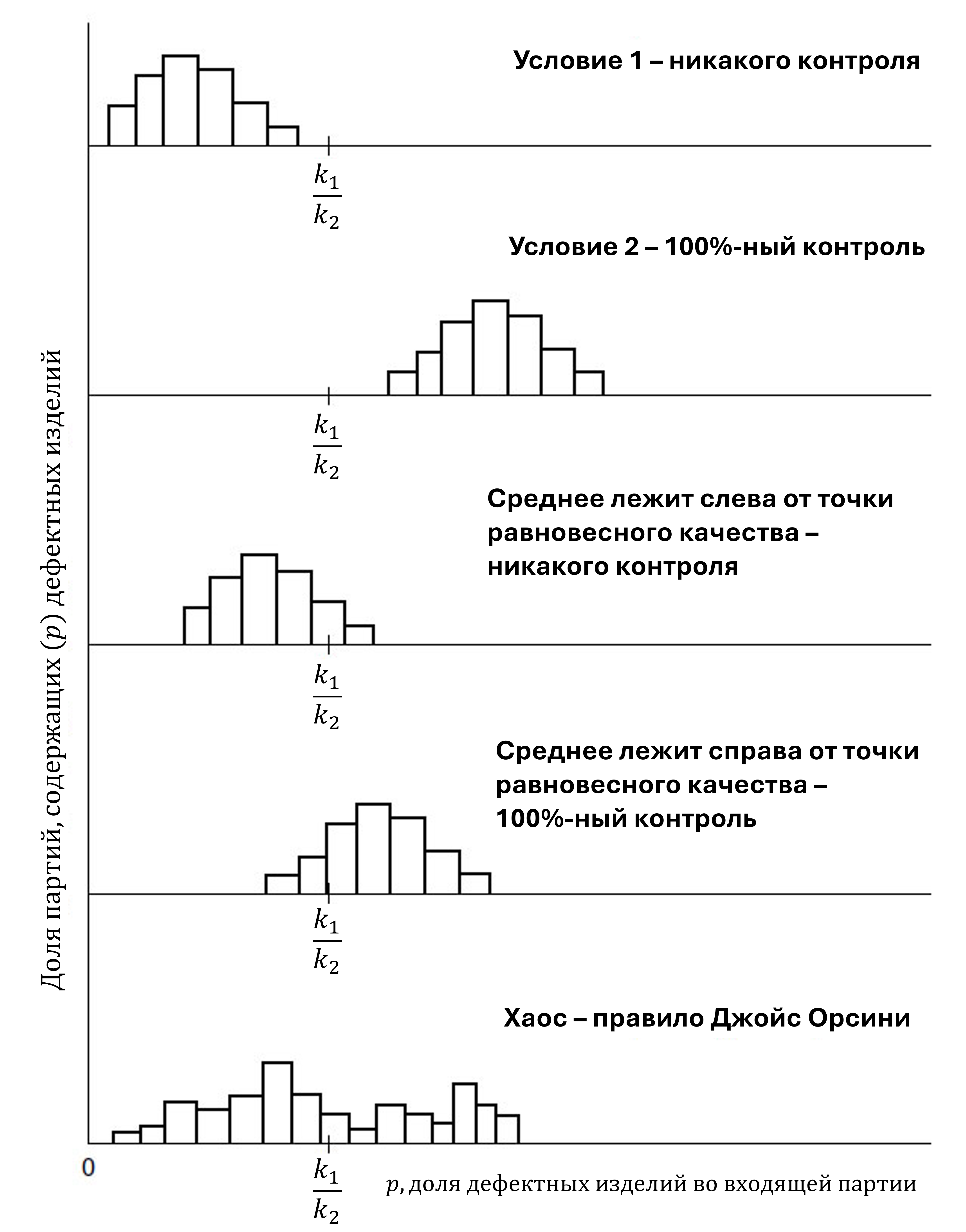
米。 1. 入荷した製品をバッチで受け取るときに考えられる状況。
点 B は、p = k となる平衡品質の点です。
1
/k
2
。 ソース:
[2]
エドワーズ・デミング、危機からの脱却
入荷バッチにおける不良品の割合の傾向
不良品の割合が増加する傾向が生じたとします。現在、私たちは条件 1 にあり、制御することはできませんが、(p) は時間に依存して増加しており、おそらく一定の割合で、おそらくは不規則に増加しています。 2 日以内に、私たちは条件 2 ゾーンに入るでしょう。私たちは警告を受けています。サプライヤーの管理図または当社の管理図があれば、傾向が明らかになります。この問題は簡単に解決できます。
異なるサプライヤー間の切り替えによって引き起こされる問題
システムの入力における材料ソースの変更により、常に問題が発生します。 2 つの情報源を考慮することに限定してみましょう。両方のソースが適切または適度に統計的に管理されており、相互に分離できる場合、原則として、各ソースは、そのソースの平均が平衡点の左側にあるか右側にあるかに応じて、条件 1 または条件 2 を満たします。このアイデアは言葉で言うと単純ですが、工場によっては実装が難しい場合があります。
2 つの供給源からの材料が一定の割合で均一に混合され、両方の供給源が十分な統計的制御を示す場合、混合されたバッチは二項混合物とみなすことができ、その最小平均制御コストは全かなしを使用して達成できます。ルール。
2 つの供給源からの材料は、生産にさらなる問題をもたらします。 2 つの供給源からの材料が均一に混合されることは、製造管理者にとって最悪のシナリオです。
最初のステップは、サプライヤーの数を 1 つに減らすことです。品質にばらつきのある製品が単一の供給元から供給されている場合、サプライヤーとその顧客は条件 1 を満たし、最終的に欠陥ゼロを達成することを目指して協力して製品を改善する必要があります。
混沌の状態
分布の位置が平衡点にわずかに近づいたり遠ざかったりする状況で何をすべきかを決定するのは比較的簡単です。
平衡点付近では、100% 制御できているか、まったく制御できていないかはあまり重要ではありません。できるだけ早く情報を収集するには、100% コントロールを選択します。入荷する材料の品質が主に平衡点の右または左にあるとは断言できず、逆に、平衡品質点を通過して大きく変動する場合、私たちは混乱状態にあります。
1. この容認できない状況は、変動性が高く、品質が予測できない材料が単一の供給源から供給される場合に発生する可能性があります。
2. 平衡品質点付近でのこのような変動は、品質が大きく異なる 2 つ以上の供給源から材料を入手することに起因する可能性があります。この場合、あるソースから別のソースへの切り替えは、考え抜かれたシーケンスなしに制御不能に実行されます。できるだけ早くこの状態から抜け出し、条件 1 に移行する必要があります。しかし、バッチは引き続き到着するため、それらを処理する必要があります。彼らにどう対処すべきでしょうか?
各バッチに不良品の割合を示すラベルが付いていれば、問題はありません。各バッチを均衡点の右または左に配置し、バッチごとにオール・オア・ナッシング・ルールを適用することで、最小の平均総コストを達成します。
しかし、バッチにはマークが付けられていません。ただし、混乱状態では、サンプル内の製品の品質と残りのバッチの製品の品質の間にはある程度の相関関係があります。したがって、混乱した状態でサンプルをテストし、何らかのルールに基づいて、残りの部分を完全に本番環境に送るか拒否するかを決定できます。
サンプリングがどれほどうまく使用されたとしても、一部のロットは平衡点の間違った側に到達し、その結果、誤って識別されたロットの総コストが最大化されます。
混沌とした状態では、人は 100% コントロールしようとする傾向があるかもしれません。この決定にはある程度の意味があります。
情報なしで放置されることはありません
進入禁止の規則は、暗闇の中でヘッドライトを消して運転することを意味するものではありません。情報を取得し、実際の納品とサプライヤーの出荷伝票、サプライヤーのテストの検査、および付属の管理図とを比較するために、すべての入荷資材をレビューする必要があります (場合によっては一部のロットをスキップすることもあります)。サプライヤーが 2 社ある場合は、それぞれの記録を別々に保管してください。
次のアドバイスは、長期的な関係に基づいて製品ごとに 1 つのサプライヤーを訪問し、彼らと協力して入荷品質を向上させることです。
破壊試験
前述の理論は、プロトタイプの非破壊テストに基づいています。一部のテストは破壊的です。彼らは管理されたサンプルを破壊します。例としては、電球の寿命、立方フィートのガスの燃焼によって生成される熱カロリー、ヒューズの動作時間、または布地のウール含有量のテストなどがあります。バッチ全体を拒否しても、本番環境に転送するものは何もないため、意味がありません。
明らかに、破壊試験の場合、唯一の解決策は、部品を即座に正確に製造するために、部品の製造において統計的制御の状態を達成することです。このソリューションは、破壊テストと非破壊テストの両方に最適です。
多くの部品の組み立てに欠陥がある可能性
前のセクションでは、1 つの部品で構成される単純な製品について説明しました。全体のコストを最小限に抑えるために、一部の部品では全数検査が必要になる場合があります。一度テストすると、アセンブリ (アセンブリ) が失敗することはありません。残りの部品はテストされず、欠陥部品が生産に入ると故障の原因となります。未テストのパーツが 2 つあるとします。
未テストの部品2つに不良品が混入している 1 そして、p 1 。この場合、アセンブリが失敗する確率は次のようになります。
広報 (断ります) = 1 – パー (拒否しません) = 1 – (1 – p 1 )(1 – p 2 ) = p 1 +p 2 -p 1 p 2
両方の p 値が 1 そして、p 2 -small の場合、この確率は次の値に近くなります。
広報 (断ります) = p 1 +p 2
任意の数の部品の故障確率を記述する簡単な方法は、ベン図を使用することです (確率論に関するどの本でも説明されています)。
すべてのpが 私 小さい。 m 部分に一般化すると、次のようになります。
広報 (断ります) = p 1 +p 2 + … + p メートル
したがって、部品の数が増えると、故障の可能性が高くなります。ラジオには 300 個の部品がある場合がありますが、この数は数え方によって異なります。数え方によっては、車には 10,000 個の部品が使用されることもあります。車に搭載されているラジオは 1 つの部品ですか、それとも 300 の部品ですか?燃料ポンプは1パーツですか7パーツですか?どう考えても、1 つのアセンブリに含まれる部品の数は膨大になる可能性があります。
` しかし、別の問題があります: k 2 部品点数が増えると、(組み立て不良を修正するコストも)増加します。組み立てが失敗した場合、どの部品に問題があるのでしょうか?誤診は非常に簡単です。また、2 つの部品のうち、両方が不良である可能性もあります。
多くの部品で構成される製品の場合:
1. 条件 2 (100% 制御) を満たすのは少数の部品だけです。そうしないと、制御コストが過大になります。
2. その他の部品については、欠陥がゼロに近い品質のみが許容されます。
複雑なコンポーネントからのアセンブリ
補助サブシステムを作成する際の可能な節約。以前の理論では、コストk 2 通常、プロセスの各ステップで増加し(おそらく 10 倍)、最終組み立て中に非常に高い値に達する可能性があります。組み立てられた最終製品を形成するフローに沿って移動するサブシステムを作成することで、不必要に高いコストを回避できる場合があります。一部のサブシステムは制御を通過し、軽微な交換や調整が必要となり、新たな出発点を形成します。コストk 2 サブシステムの監視と調整のコストになります。理論と有用な経験の記録を組み合わせると、一部のサブシステムはまったくテストする必要がない一方、他のサブシステムはプロセスの進行に伴うコストの増加を避けるために 100% 制御する必要があることがわかります。この章で説明する理論により、正しい決定を下すことができます。
前のセクションの目的は、正しい理論に従えばコストを最小限に抑え、利益を最大化する方法があることを示すことです。
同時に、工程内での不良品の徹底的な排除にも努めます。当社では、自社のテスト結果とサプライヤーのテスト結果を比較し、X チャートや R チャート (シューハート管理図) などの適切な統計手法を適用することで、これを体系的に行っています。
部品、特に重要な部品のサプライヤーとの協力が実り、サブシステムのテストと調整が成功することで、システムの最終検査中のすべての重大な問題がまれな事象に抑えられます。
入荷した材料はサプライヤーにとって副産物です
サプライヤーにとって顧客にとって重要な材料が、そのビジネスの 1% 未満に相当する副産物である可能性がある場合。サプライヤーは、製品を改善するために機器を設置するコストとリスクを負担することは期待できません。
考えられる推奨事項は、この材料を鉄鉱石または変動性が高く精製されていないその他の投入物と考えることです。独自の材料洗浄システムをインストールするか、サードパーティ会社のサービスを利用します。この計画は場合によっては有効です。
稀な欠陥の検出の難しさ
まれな欠陥は検出が困難です。不良品の割合が減少するにつれて、その数がどの程度小さいかを判断することがますます困難になります。検査を使用してすべての欠陥を検出することは、特にまれな場合には不可能であり、これは目視検査と自動検査の両方に当てはまります。 10,000 個の製品に 1 個の欠陥しかないと主張するメーカーを、5,000 個の製品に 1 個の欠陥があると主張するメーカーを信頼する理由はありません。どちらの場合も、この割合を推定するのは困難です。
したがって、(p) が 1/5000 に等しく、プロセスが統計的に管理された状態にある場合、16 個の欠陥部品を見つけるために 80,000 個の部品を検査する必要があります。
セルゲイ・P・グリゴリエフ:
5000×16=80000
これらのデータは、標準誤差 σ = √16 = 4 で、製造プロセスの平均不良率の推定値 p = 1/5000 を示します。多くの監視が困難であるにもかかわらず、この不良率の推定値は不正確です。 8万部品。 80,000 個の部品を生産する間、プロセスは安定したままでしたか?という疑問が生じます。そうでない場合、16 番の不良品にはどのような意味があるのでしょうか。難しい質問。
セルゲイ・P・グリゴリエフ:
この場合、サプライヤーのプロセスが統計的に制御された状態にある場合、上限 (VKG) の値を持つサイズ 80,000 部品のサブグループの形でバッチの平均値 c = 16 個の欠陥を中心に動作すると想定されます。 、UCL) および下位 (NKG、LCL) 管理限界 C-管理図: UCL、LCL = c ±3σ または UCL、LCL = c ±3√c。これにより、平均 (c=16) 付近の値の広がりが生じます。 ±12以内。
計算式は、GOST R ISO 7870-1-2011 (ISO 7870-1:2007)、GOST R ISO 7870-2-2015 (ISO 7870-2:2013) - 統計的手法に記載されています。シューハート管理図 [十一] 。
(σ) を計算するために、デミングは 80,000 個の部品に相当する一定の定義領域あたりの欠陥数の C 管理図を使用します。
なぜ 16 なのか?平均値 (16) により、C 管理図の (σ) 値を簡単に計算でき、管理下限と上限が得られます。
したがって、サプライヤーがそのような欠陥率 (1/5000) を主張するには、その生産プロセスの安定性を理解する必要があり、それはシューハート管理図を使用してのみ確認できます。管理図は、たとえば、最小 8 ポイント。各ポイントは 80,000 個の部品のバッチあたりの欠陥数であり、4 ~ 28 個の欠陥が分布している可能性のある整数値です。 経験則 平均すると、80,000 個の部品のバッチあたり 16 個の欠陥。
5000 個の部品の定数定義領域で欠陥の平均値 c = 1 を使用してこれらの単純な数学的操作を実行することがなぜ不可能だったのでしょうか?はい、平均値 c=1 を下回る管理図上の欠陥数の整数 (ゼロを除く) からはポイントを取得できないためです。数学的には、計算で小数、たとえば = 0.3 を取得するのは簡単ですが、実際の条件でテストされたバッチ (サブグループ) 内の欠陥数 0.3 を取得できる可能性をどのように想像しますか?
数百万個の部品に故障がひとつもなかったり、その数が非常に少なかったり、100億個の部品が欠落している例もあります。不良品の割合が非常に小さい場合、完成品を管理していないと必要な情報を得ることができません。このような極端な要求で何が起こっているかを知る唯一の方法は、プロセス中の部品の実際の測定値を含む管理図を使用することです。 4 項目を 1 日 25 回連続して実行するなど、100 回の観測では、サブグループ平均と範囲の X グラフと R グラフのサンプル ポイントが 25 個得られます。シューハート管理図は、プロセスが変更なく進行しているのか、それともどこかで障害が発生し、原因が判明するまで多数の製品の生産を停止する必要があるのかを示します。理由が判明したら、一定期間製品セット全体を拒否するか、一部の製品をスキップするかを決定できます。平均サブグループと範囲サブグループの XbarR 管理図の機能がますます向上していることが、ますます明らかになってきています。
セルゲイ・P・グリゴリエフ: 記事中のドナルド・ウィーラー 代替データ (カウント) の管理図、P チャート、NP チャート、C チャート、U チャート、または個別の値の 1 つの XmR チャート? エドワーズ・デミング氏のこの推奨を補強するものです。
「測定結果が得られる場合、離散的な数量 (カウント) を使用することが意味を成すことはほとんどないため、属性の使用は通常、「失敗」を数えられる状況に限定されます。しかし、「失敗」を定義することは、通常、非常に困難を伴います。 「失敗」の定義が難しいことが主な問題です 操作上の定義 」。
予約の利用
複雑な機器を設計する場合、2 つ以上の部品を並列に配置して、そのうちの 1 つが故障しても、もう 1 つが自動的にその機能を引き継ぐことが可能かつ合理的な場合があります。 2 つの平行な部品、それぞれの平均欠陥率 p 私 、平均不良率が p に等しいものと同等です。 私 ²。たとえば、p の場合、 私 =1/1000、すると p 私 ²=1/1000000。
もちろん、重量とサイズの制限により、冗長性の使用が妨げられる場合があります。
他にも懸念事項があります。必要なときにバックアップ部分が機能するかどうかです。おそらく最良の解決策は、単一部品の高い信頼性です。
結論
製造工程において、材料や製造上の欠陥は容認されません。上で概説した理論は、製造のどの段階でも材料の欠陥を許容しないことがいかに重要であるかを教えてくれます。 1 つの操作の結果が次の操作の入力材料となります。欠陥のある材料は、一度製造されると、運が良ければその後のテストで欠陥が発見されるまで欠陥のままですが、修正と交換の費用は決して安くありません。
統計的に制御可能な状態には、明らかな利点があります。入ってくるバッチ フローが条件 1 または条件 2 を満たしているか、あるいは混沌に近い状態にあるかを知るには、できればサプライヤーと協力してサプライヤーの管轄内で、小さなサンプルの継続的なテストから構築されたシューハート管理図を使用して、統計的管理と不良品の平均割合を監視するだけで済みます (いずれの場合も)。
例外
多くの入力資料は、上で概説した理論に従っていません。たとえば、エアホースで撹拌した後のメタノールのタンク。タンクのほぼどの部分から採取したメタノール サンプルも、ほぼ同じになります。ただし、化学会社はさまざまなレベルでメタノールをサンプリングします。おそらく、より近い例は、ジンまたはウィスキーのショットを試飲することです。私たちは、ボトルの上部、中央、または底のどこから部分を採取するかは問題ではないことに同意します。
説明 Sergey P. Grigoryev: 上の段落は、サンプル管理の結果がバッチ全体に帰属する可能性がある例外的なケースについて言及しています。
高炉の加熱は問題を引き起こしますが、これもこの章の理論が適用されない例です。加熱が均一ではありません。一部の企業は、瓶詰めごとに少量のサンプルを採取します。これらのサンプルを分析すると、最初のキャストから最後のキャストまでの品質の変化を示すプロセス チャートのデータが得られ、改善の手がかりが得られます。
Sergey P. Grigoryev による説明: 上の段落では、定義上、プロセスがプロセスのさまざまな段階で異種混合であり、各段階から 1 つのサンプルを取得する可能性がある例外的なケースについて説明しています。このような場合、異なるバッチ (鋳物) 間の変動を分析するには、個々の値の制御 XmR マップを使用する必要があります。
オープンソース ソリューションを参照してください。 ランダム受け入れ品質管理にテーブルを使用する場合の問題点 。