実験、ビッグデータ、それともシューハート管理図?
Donald Wheeler による記事: 「プロセス改善へのさまざまなアプローチ。あなたのアプローチは望みどおりの結果をもたらしますか?」
ドナルド J. ウィーラー: 「プロセス改善へのさまざまなアプローチ。あなたのアプローチは必要なことを実現していますか?」
翻訳: AQT センター科学ディレクター
セルゲイ・P・グリゴリエフ
。
記事への自由なアクセスは、記事に含まれる資料の価値を決して減じるものではありません。
現在、プロセスを改善するためのさまざまなアプローチが提案されています。効果的なアプローチを選択するには、各アプローチがどのように機能するかを評価することが重要です。ここでは、生産上の問題と、さまざまな改善アプローチがこの問題をどのように解決するかを見ていきます。
生産上の問題
以下の説明では、原因の意味の変化が製品特性の意味の変化をもたらす場合、因果関係が存在します。ここで、原因結果を、原因がその自然な値の範囲内で変化したときに製品の流れに生じる変動として定義します。原因が限定的で変更できない場合、製品の価値の流れに変化は生じなくなります。
製造された製品の特定の特性は、数百とは言わないまでも、数十の因果関係の結果です。これらの原因は 2 つのグループに分類できます。1 つは名前を挙げることができるほどよくわかっている原因、もう 1 つは私たちの知らないうちに作用し、したがって未知のままである原因です。生産を開始する前は、これらすべての原因の結果が不明である可能性があり、その結果、図 1 のような状況が得られます。
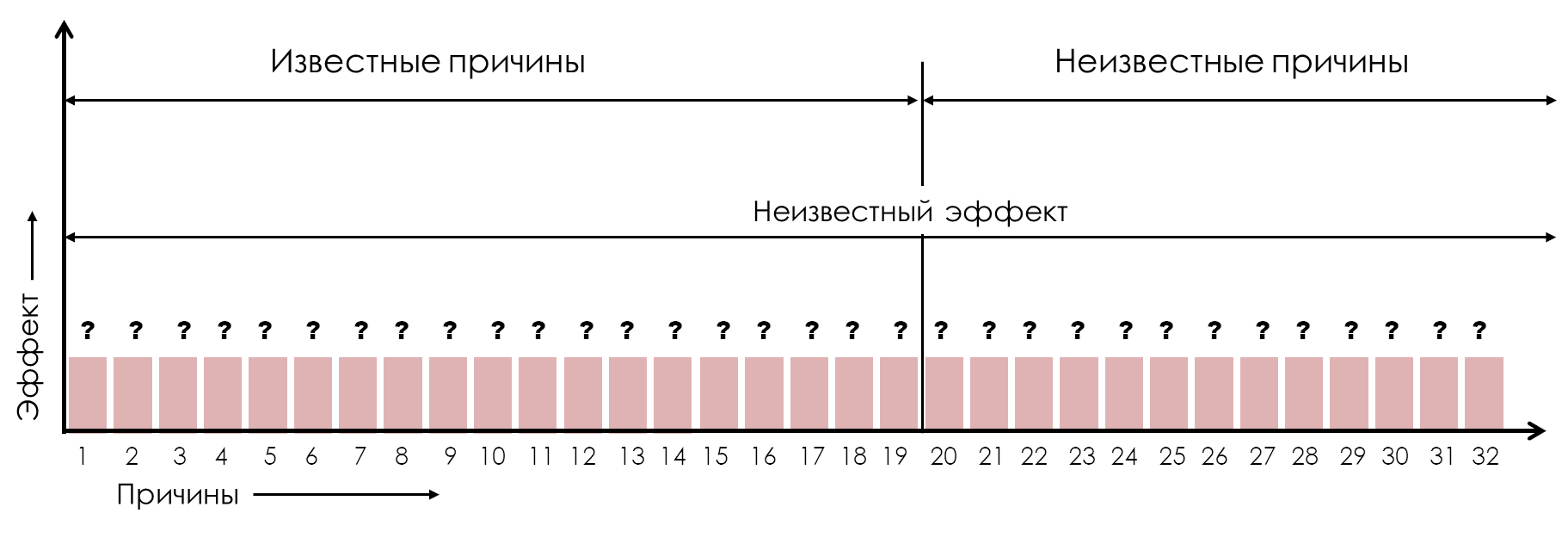
図 1: 因果関係の 2 つのカテゴリ
通常、R&D では、既知の原因のサブセットを調査して、その結果を判断します。調査される理由は、製品の特性に顕著な影響を与えると考えられるものです。これらの効果が判明したら、この調査された原因のセットは、図 2 に示すように、パレート図 (グループ I、II) に整理できます。
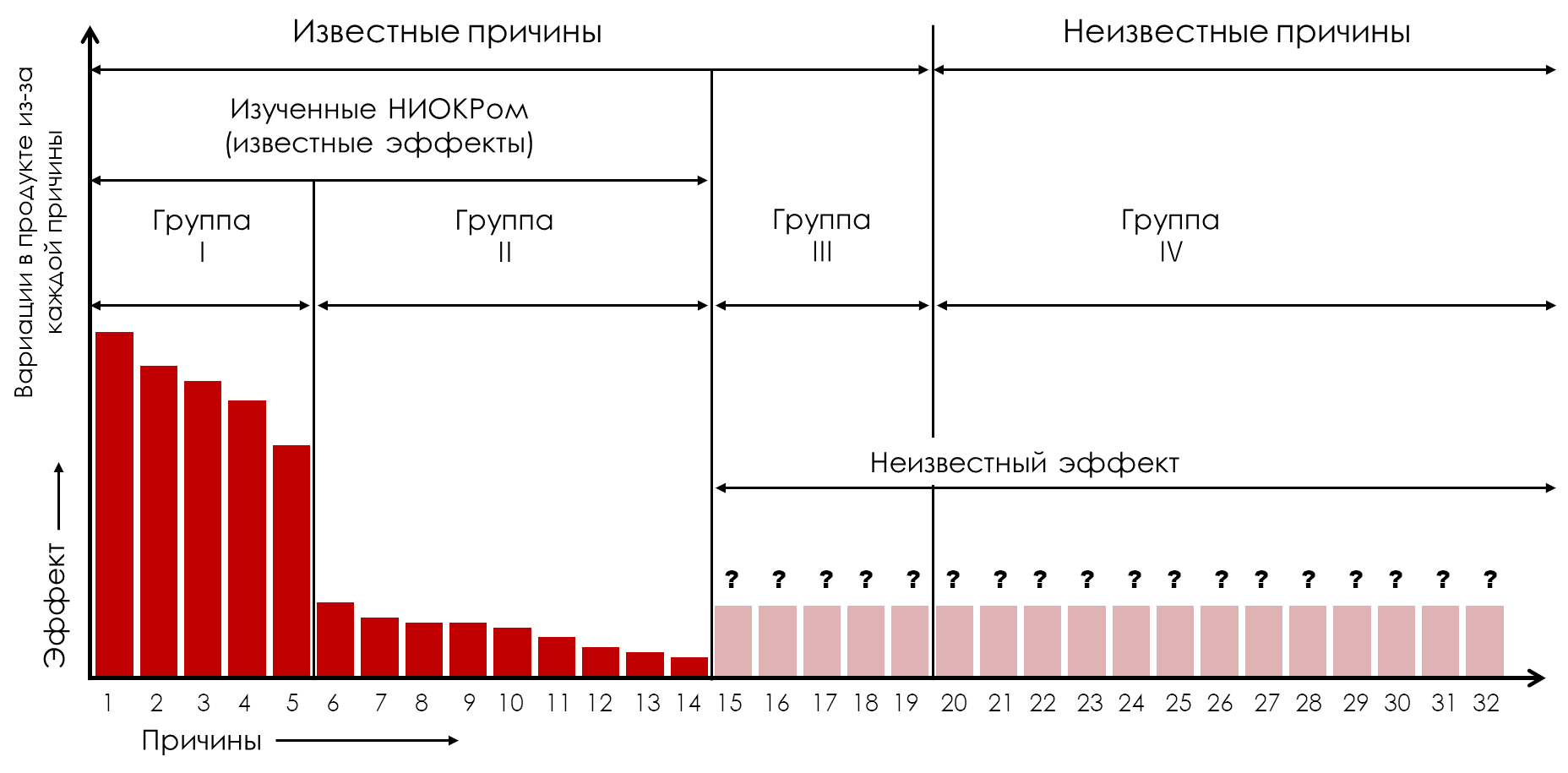
図 2: 研究された原因に対する既知の影響のパレート図 (グループ I、II)
1 番目から 5 番目までの理由を、第 1 グループの理由とします (図 2、グループ I)。これらの原因は支配的な影響を及ぼし、生産中に制御したい原因となります。これら 5 つの原因を一定に保つことで、製品の流れからその影響を効果的に排除します。同時に、これら 5 つの原因のそれぞれに対して選択された固定値が集合的にプロセスの平均値を決定します。
6 から 14 までの理由は、2 番目のグループの理由です (図 2、グループ II)。これらの原因による影響は非常に小さいため、本番環境では制御しようとしません。 (これらは通常、制御のコストが制御の利益を上回る理由です。)
研究開発で調査された 14 の原因のうち、これらの原因を制御する試みが行われなかった場合、グループ 1 の 5 つの原因の影響が製品フローの変動の 85 パーセントを占め、グループ 2 の残りの 9 つの原因が製品フローの変動の 15 パーセントに寄与することになります。バリエーション。したがって、原因の最初のグループを制御することにより、調査された原因によって引き起こされる製品フローの変動の 85 パーセントが排除されます。
3 番目のグループ (図 2、グループ III) の原因は、研究開発によって研究されていない既知の原因です。通常、これらの原因は、その影響が最小限であると考えられているため、研究する価値がありません。ただし、図 2 に示すように、これらの原因は実際には未知の結果をもたらします。
便宜上、私たちの知らないうちにプロセスに影響を与える未知の因果関係の全体を、4 番目のグループ (グループ IV) の原因として示します。
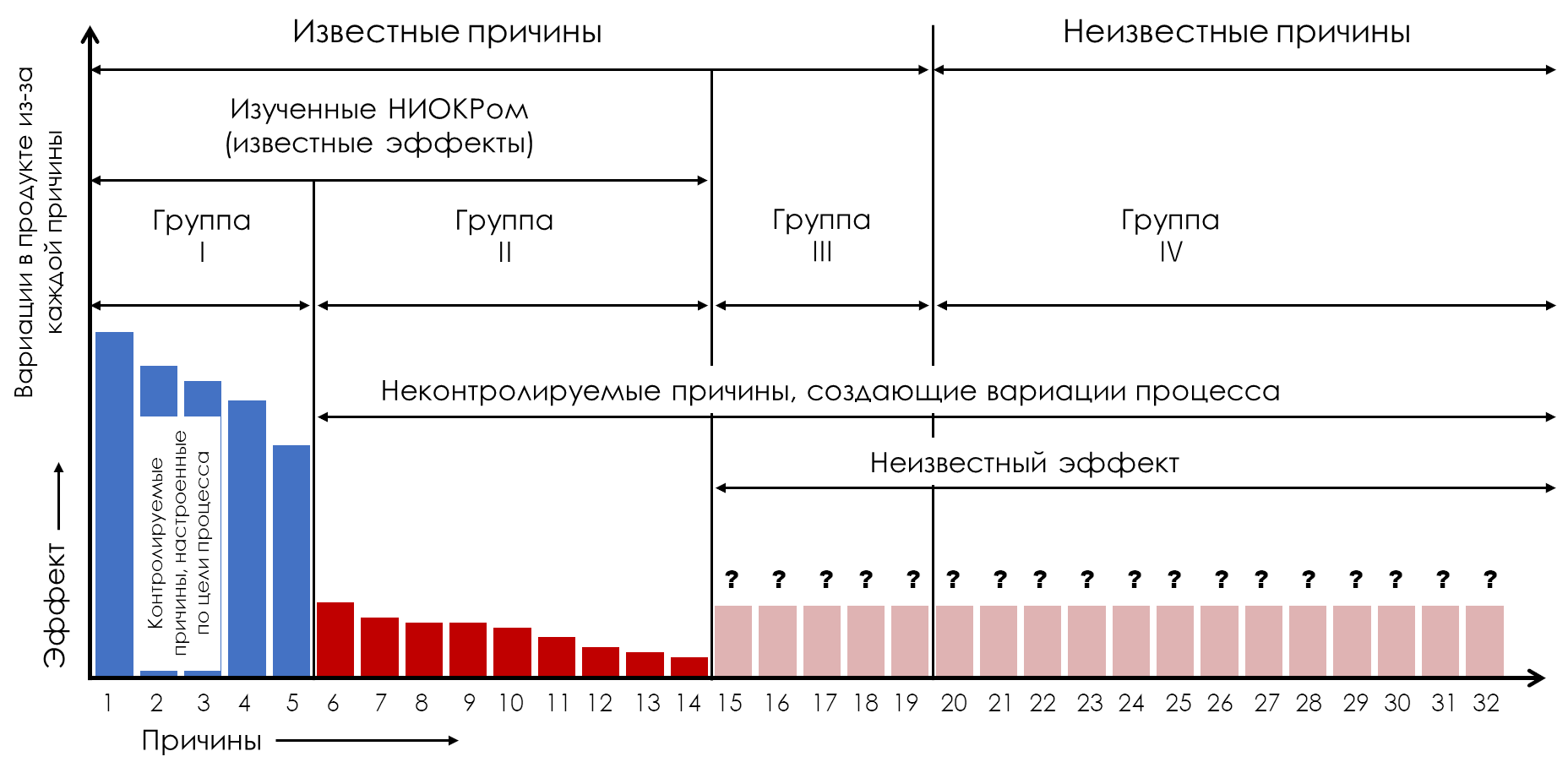
図 3: プロセスの変動は、あらゆる制御不能な原因によって発生します。
残念ながら、生産される製品の流れの変動は、2 番目のグループ (グループ II) の原因に限定されません。 3 番目のグループ (グループ III) と 4 番目のグループ (グループ IV) の原因も、この変動に寄与しています。これら 3 つのグループ (グループ II、III、IV) の原因は異なるため、それぞれが製品特性の変動に寄与し、これらすべての変動源が合計して製品の流れの変動となります。生産時に観察される変動が、通常、研究開発で予測される変動を超えるのはこのためです。
最後に、グループ III および IV の原因によるすべての未知の影響が重要ではないという保証はありません。さらに、これらの効果は時間の経過とともに変化する可能性があります。これらの変化は、磨耗、人員の変更、作業方法の開発、材料供給の変更などによって発生する可能性があります。このような変化が発生すると、プロセスの改善がさらに困難になる可能性があります。
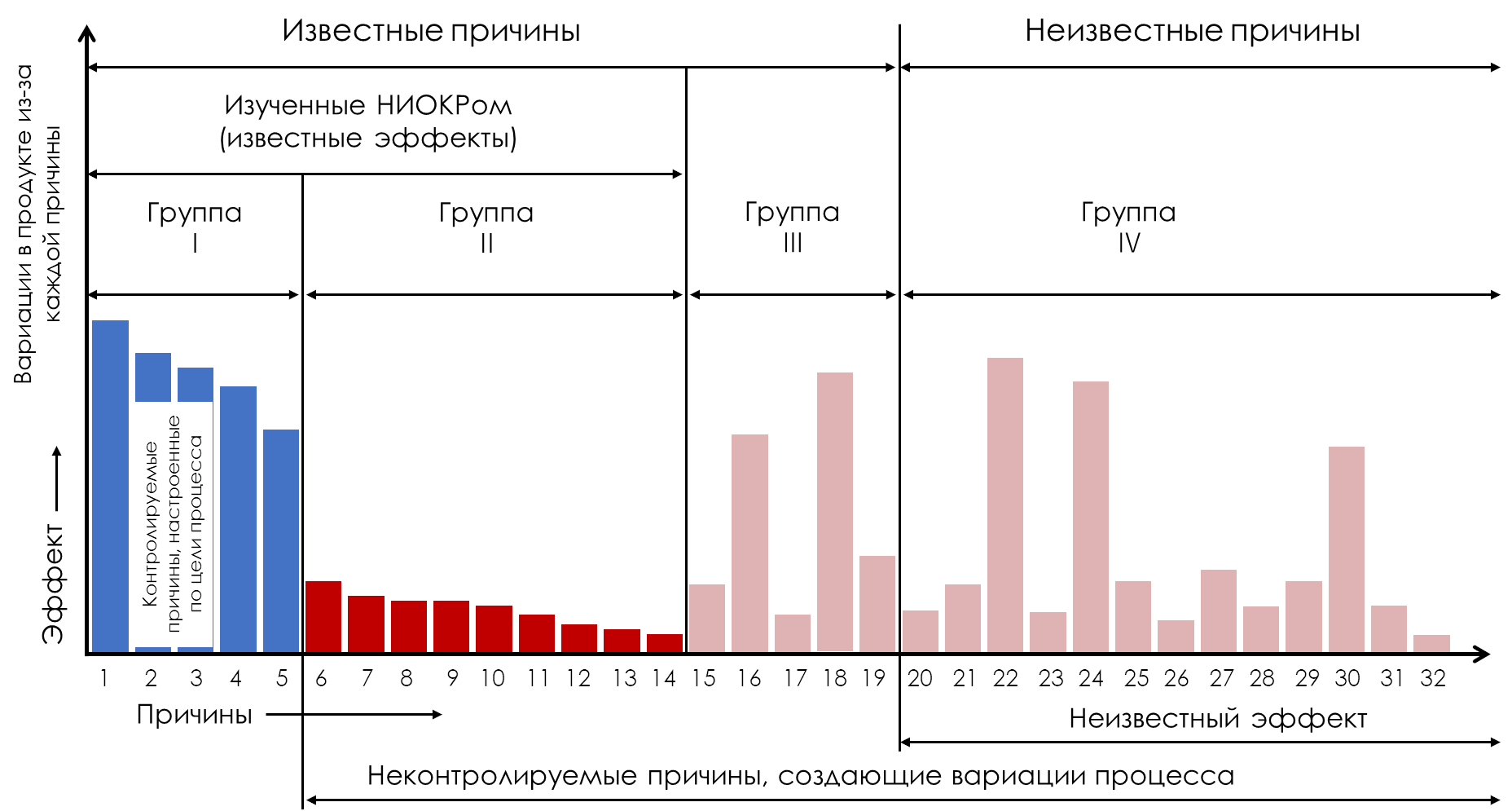
図 4: 制御できない原因によっては、支配的な影響が及ぶ可能性があります。
したがって、図 3 と図 4 は、さまざまな改善アプローチを評価するためのフレームワークを提供します。これらは、私たちが知っていることと知らないことを特徴づけるため、特定のアプローチがプロセス改善問題の各要素にどのように関連しているかを確認できます。
図 3 から、プロセスを目標 (公称) に合わせて調整する際の問題は、最初のグループ (グループ I) の原因のレベルの選択に関連していることがわかります。製品の流れの変動を減らすという問題は、他の 3 つのグループ (グループ II、III、IV) の原因と関連しています。
では、どうすればプロセスのばらつきを減らすことができるのでしょうか?基本的に、ばらつきを減らす唯一の方法は、その原因をある固定レベルに保ちながら、製品の流れから影響を除去することです。言い換えれば、原因を第 2、第 3、または第 4 グループ (グループ II、III、IV) から最初のグループ (グループ I) に移動することによって変動を排除します。
ただし、原因を最初のグループ (グループ I) に移すことで費用対効果が高くなるには、利益が費用を上回る必要があります。これは、原因を制御しようとすることが経済的に実現可能になる前に、その原因が支配的な影響を及ぼさなければならないことを意味します。
したがって、プロセスの変動性を低減するタスクは、2 番目、3 番目、または 4 番目のグループ (グループ II、III、IV) で主な影響を持つ原因を見つけて、これらの原因を最初のグループ (グループ I) に移すことです。
実験的アプローチ
プロセスを改善するためのいくつかのアプローチは、一連の実験に依存しています。実験により、個々の原因を研究し、特定の製品特性に対する影響を定量化することができます。これらの実験的アプローチは、単純な単一原因実験から計画された複数原因実験まであらゆるものをカバーします。複雑さに関係なく、実験研究では常にプロセス入力の操作が必要です。これにより、実験的アプローチは、第 1、第 2、または第 3 グループ (グループ I、II、III) からの既知の原因を研究することに限定されます。
最初のグループ (グループ I) の理由を調査したら、最適化の調査を行います。ここでは、研究対象の製品特性をプロセス目標(公称)に一致させるための最適な値につながる、最初のグループの理由の値の組み合わせを見つけるように努めます。
グループ 2 または 3 (グループ II、III) の原因を使用して実験研究が使用される場合、目標は、支配的な影響を与える可能性のある原因を特定することです。そのような原因が特定されると、それらの原因を最初のグループに移動して、製品フローからその変動を削除できます。もちろん、グループ 2 (グループ II) の原因を使った実験では、研究開発が当初小さな効果しか発見しなかった場合に、大きな効果を探すことになります。そして、グループ 3 (グループ III) の原因を調査する実験では、大きな影響が存在すると考えられていなかった場所で大きな影響を探すことになります。しかし、時間の経過とともに、磨耗やその他のエントロピーの影響により、以前はほとんど影響がなかった原因が、大きな影響を与える原因になる可能性があります。
このため、2 番目と 3 番目のグループ (グループ II、III) の原因を使った実験が役立つ場合があります。図 4 では、理由 16 と 18 (グループ III) が支配的な影響を持っていることが判明したため、グループ 3 からグループ 1 に移動されました (図 5)。これにより、このプロセスの平均生産コストと使用コスト (ACP&U) が図 4 の 75% に削減されました。
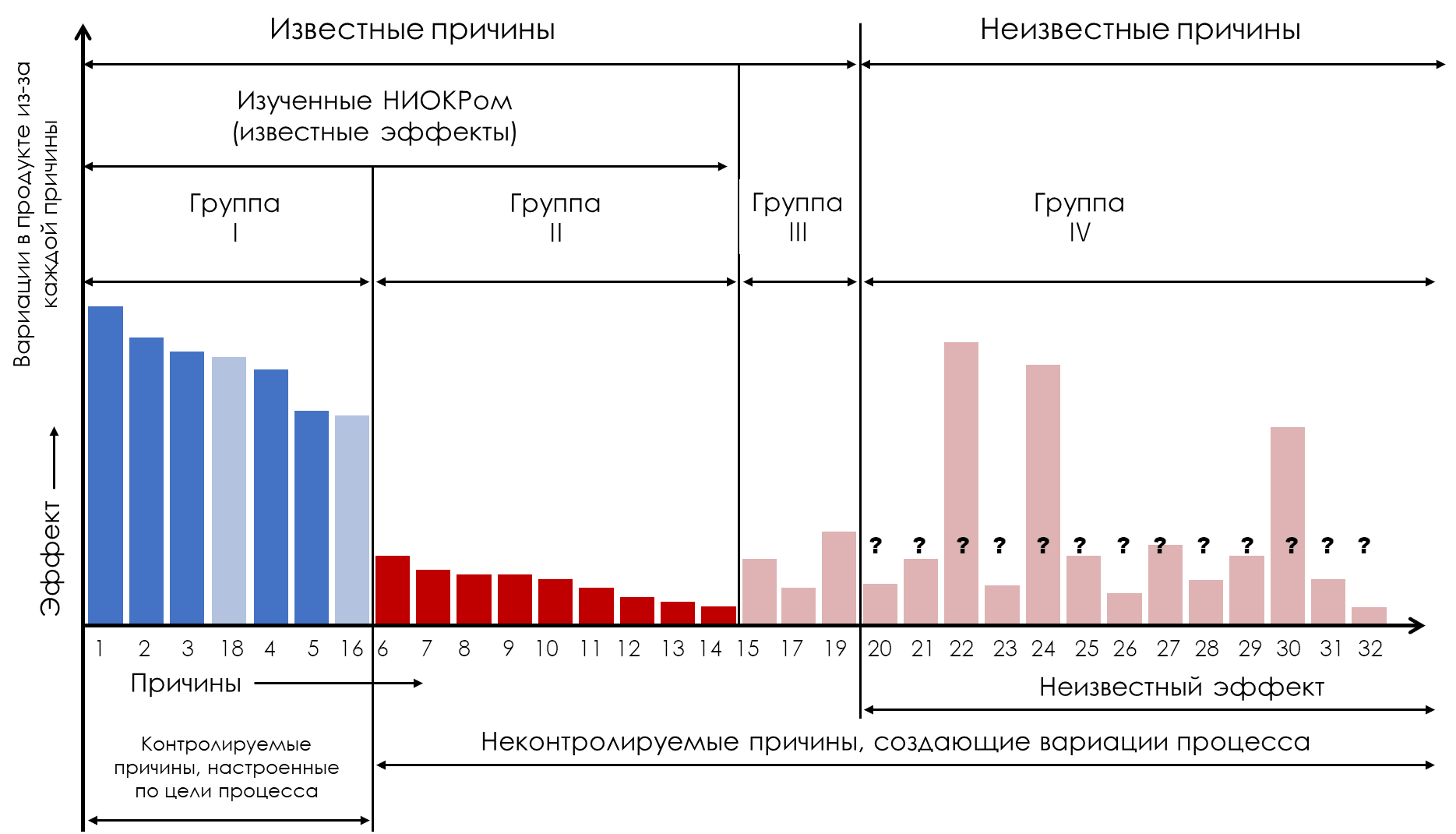
図 5: どのような実験結果が得られるか
しかし、4 番目のグループ (グループ IV) の原因はどうなるのでしょうか?実験で未知の原因を調べることはできませんが、これは、実験結果が第 4 グループの未知の原因の影響を受けないことを意味するものではありません。 4 番目のグループの主要な原因が実験中に変化すると、分析が台無しになり、実験が台無しになる可能性があります。 (ほとんどの統計学者は、研究の外部からの無関係な変数が実験に干渉したときに何が起こったのかについて話してくれるでしょう。)
したがって、実験研究はプロセス設計に不可欠であり、さまざまなプロセス入力の影響を分析できるようになりますが、プロセス改善タスクでは一定の制限に直面します。実験によって特定の質問に対する具体的な答えを得ることができますが、どのような質問をすればよいかわからない場合、その有用性は限られています。
観察的アプローチ
実験的研究は常に、調査対象の原因を特定することから始まります。観察的アプローチでは、このことは行いません。むしろ、既存のデータを使用してプロセスに関する洞察を得ようとします。既存のデータは通常、グループ 1 (グループ I) の原因が一定である間に取得されるため、観察的アプローチでは制御できない原因に重点が置かれる傾向があります。
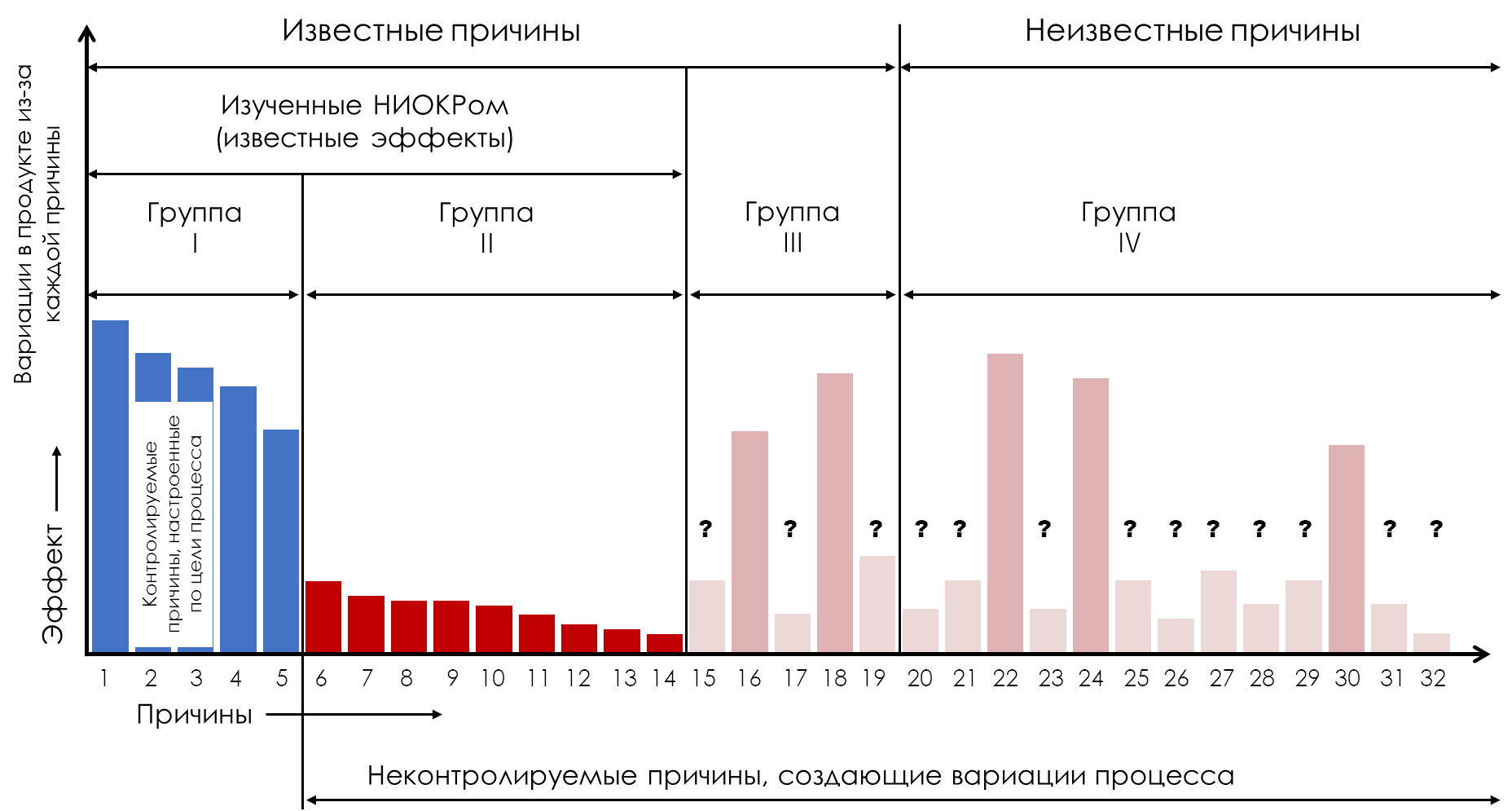
図 6: 知っておくべきこと
観察アプローチの背後にある考え方は、図 6 のすべての影響の大きさを実際に知る必要はないということです。むしろ、どの制御不能な原因が支配的な影響を持っているかを知る必要があるだけです (ここでは原因 16、18、22、 24、30)。どの原因が製品の流れを変えるほど大きな影響を及ぼしているかがわかれば、どの原因を最初のグループ (グループ I) に移動する必要があるかがわかります。そして、私たちはその結果の大きさを実際に定量化することなく、これらの原因について決定を下すことができます。以下では、主に 2 つのタイプの観察研究の特徴について説明します。
データ追跡へのアプローチ
今日のコンピューティング能力のおかげで、既存のデータを分析するための独創的な新しいアプローチが普及しつつあります。これらのアプローチは以前はデータ追跡と呼ばれていましたが、現在ではビッグデータ、人工知能、または機械学習のアプローチとして知られています。名前に関係なく、これらのアプローチは利用可能なすべてのデータをデータベースに収集し、いくつかの数学的手法を使用してデータ内のパターン、グループ化、または関係を見つけます。これは有望に聞こえますが、使用する変数の数に関係なく、これらのアプローチの主な問題は、データが常に不完全なコンテキストを持つことです。
コンテキストは分析にとって非常に重要であるため、コンテキストはデータ分析の最初の公理です。つまり、コンテキストの外にあるデータは意味を持ちません。ただし、データ追跡アプローチでは完全なコンテキストが得られることはありません。データベースにどれだけ多くの変数を含めても、4 番目のグループ (グループ IV) の変数を含めることはできません。未知の因果関係は決して測定されないため、データベースに含めることはできません。 (それらの影響を測定するのに十分な知識があれば、それらは未知の原因ではなく既知の原因となるでしょう。) したがって、データ追跡アプローチは既知の原因と製品の特性の間の関係を発見するのに役立ちますが、未知の理由を特定することはできません。
すべてのデータ追跡手法の背後にある暗黙の前提は、データの背後に均一な条件がある、つまりデータベースに含まれていない変数は研究対象の結果に実質的な影響を及ぼさないということです。しかし、この基本的な仮定を効果的にテストする方法はありません。未知の原因がプロセスを支配すると、データ追跡方法で検出されたパターンが完全に歪曲される可能性があります。したがって、これらのアプローチは既知の変数間のパターンを見つけようとしますが、4 番目のグループ (グループ IV) の変数によって損なわれる可能性があります。
プロセス動作チェックリスト
プロセス動作管理図 (シューハート管理図) は、プロセスを改善するための観察的アプローチであることが証明されています。彼らは与えます 運用上の定義 あらゆるプロセスを最大限に活用する方法。現在の製品性能記録 (管理図上の点) は、プロセスの実際の性能を反映しています。管理図の限界は、プロセスの可能性、つまり最小限の変動で意図したとおりに動作するときにプロセスが達成できる能力を定義します。プロセスのパフォーマンスをプロセスの潜在能力にマッピングすることにより、プロセス動作管理図を使用して、プロセスが潜在能力を最大限に発揮して稼働する状態にどの程度近づいているかを評価できます。また、プロセスに変化がいつ発生したかを判断することもできます。そして、これらの変化は、4 番目のグループ (グループ IV) からの支配的な影響を伴う未知の原因を特定する鍵となります。
シューハートの管理図がどのように機能するかを理解していない批評家の中には、シューハートの管理図は「時代遅れ」であると主張する人もいます。しかし数学に関しては、年齢によってテクニックの価値が下がったり、その適用可能性が変わったりすることはありません。ピタゴラスの定理は少なくとも 2500 年前のものです。 Walter Shewhart は 90 年以上前にプロセス動作管理図を作成しました。管理図の背後にある概念は 2,200 年前のものです。システムに影響を与える原因を発見するには、システムが変化するポイントに注目しなければならないことを私たちに教えてくれたのはアリストテレスでした。そしてこれは本質的に、プロセス動作管理図によって実現できることです。
プロセス動作管理図を使用して、プロセスが変化するポイントを特定することにより、4 つのグループ (グループ I、II、III、IV) のいずれかに由来する支配的な影響を伴う原因を検出できます。
プロセスが動作の変化を示すのを待つことで、プロセスが影響の大きさに応じて原因に優先順位を付けることもできます。このようにして、重要でない影響を与える多くの原因を研究するのに時間と労力を無駄にすることなく、主要な影響を与える原因を発見します。
シューハートとアリストテレスのアプローチによってのみ、支配的な影響を持つ 4 番目のグループ (グループ IV) から未知の原因を発見することができます。プロセス動作管理図は、プロセス動作管理図によって検出される信号を生成する支配的な影響を伴う既知の原因と未知の原因の両方を特定できますが、4 番目のグループ (グループ IV) の原因について学習できることが、管理図を使用する主な利点です。 。これにより、製造現場では実際に起こっているものの、研究開発 (R&D) プログラムでは決して研究されないような間違い、悪い慣行、愚かなことについて学ぶことができます。これにより、何か問題が発生したときにリアルタイムで検出し、タイムリーに修正できるようになります。したがって、プロセス動作管理図は他のアプローチよりも一般的で信頼性が高くなります。
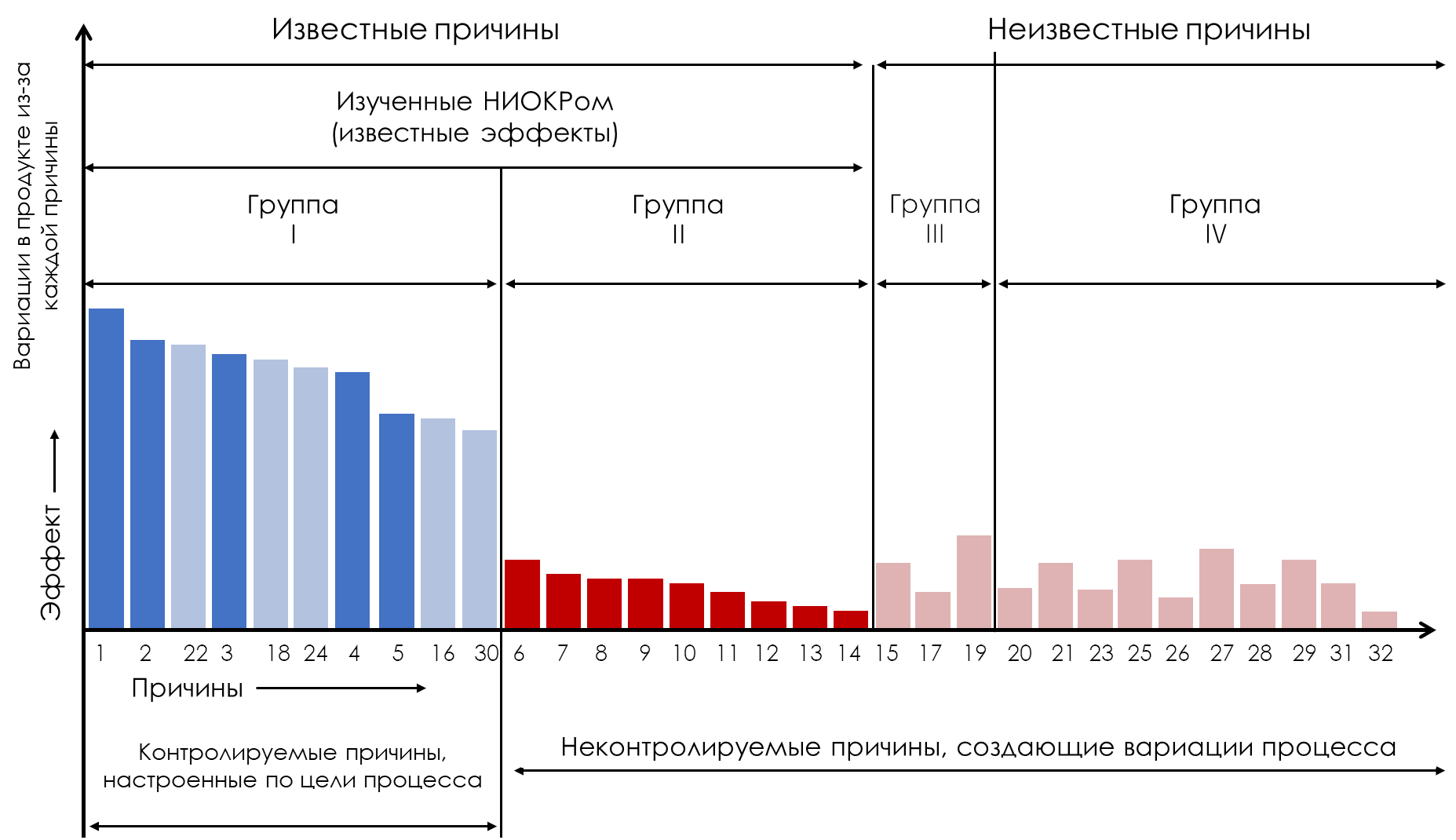
図 7. プロセス動作管理図で実現できること
図 7 に示すプロセスの場合、生産および使用の平均コスト (ACP&U) は、図 4 に示すプロセスの生産および使用の平均コストのわずか 25 パーセントになります。品質と生産性は 4 倍向上します。理由の移動: 22、18、24、16、および 30 を最初のグループに追加します。
説明内のこの段落の説明を参照してください タグチ品質損失関数 。
まとめ
プロセス改善への実験的アプローチでは、既知の因果関係のみを研究できます。このような検討はプロセスチューニングには必要ですが、プロセス改善手法としては限界があります。最初と 2 番目のグループ (グループ I、II) の原因研究は以前の研究を再現し、3 番目のグループ (グループ III) の原因研究は以前の研究で見逃したナゲットを見つけることを目的とします。したがって、2 番目と 3 番目のグループ (グループ II、III) の原因の実験的研究では、これらの原因のほとんどがまだ無視できるほどの影響を及ぼしていることを本質的に確認するには、時間、費用、および労力が必要になります。さらに、実験では第 4 グループ (グループ IV) の原因を研究することはできず、支配的な効果を持つ第 4 グループの原因によって実験結果が損なわれる可能性があります。
プロセス改善のためにデータを追跡するアプローチには、データをモデル化し、2 番目と 3 番目のグループ (グループ II、III) の原因を使用して関係を発見しようとするビッグ データ、人工知能、機械学習技術が含まれます。残念なことに、これらのアプローチは、その複雑さと高度さにも関わらず、支配的な影響を伴う原因の 4 番目のグループ (グループ IV) によって損なわれる可能性があります。
プロセス動作管理チャートだけが、既知の原因と未知の原因の両方によって引き起こされる障害を明示的に検索します。プロセスが変化するポイントを研究するアリストテレスのアプローチにより、実験研究の範囲を超え、データ追跡方法では検出できないものを発見することができます。さらに、プロセス挙動管理図のアプローチでは、些細な効果の定量化に時間と労力を無駄にすることがありません。プロセス動作管理図を使用すると、支配的な影響を伴う原因に常に焦点を当てることで、変動を最小限に抑え、正確に目標どおりにプロセスを予測どおりに実行する方法を学ぶことができます。
したがって、研究者や開発者が見逃していた何かを発見できると確信している場合は、プロセス改善のための実験的なアプローチをとってください。
または、アリストテレスとは異なり、プロセスが時間の経過とともに変化しないと確信している場合は、データ追跡アプローチのいずれかを使用してプロセスを改善します。これらのテクニックの複雑さと洗練さには誰もが無関心ではありません。ただし、結果は砂上の楼閣のように信頼できる可能性があることに注意してください。
プロセスを改善したいだけなら、プロセス動作チェックリストを使用して、プロセスを最大限に活用する方法を学習してください。これほど少ない労力でこれほど多くの成果が得られるものはありません。