シンプルなグラフィカル手法を使用した測定プロセス (EMP) の評価
出典: [34] Donald J. Wheeler、記事:「A Better Way to Do R&R Studies. The Evaluating the Measurement Process Approach..」 / Donald Wheeler、記事:「A Better Way to Do R&R Studies. Evaluating the Measurement Process Approach..」 。」 Donald Wheeler 博士のご厚意により記事を提供していただきました。翻訳とコメント: Sergey P. Grigoryev
あなたはできる ダウンロード この記事のデータ。
記事への自由なアクセスは、記事に含まれる資料の価値を決して減じるものではありません。
当社のソフトウェアを使用すると、次のことを行うことができます 測定プロセスの評価 (測定プロセスの評価、EMP)。これは、測定オペレーターから上級管理者まで、結果を見せることを決めたすべての人にとって明らかです。
この記事では、より少ない労力でデータから測定システムのゲージ再現性と再現性 (ゲージ R&R) について詳しく知る方法を説明します。測定プロセス (EMP) の評価アプローチでは、一連の計算に迷うのではなく、情報のグラフィック表現の力を利用して、データの興味深い側面を明らかにします。
EMP (測定プロセスの評価) 調査
EMP 研究の背後にある考え方はシンプルかつ奥深いものです。私の友人で同僚の故リチャード・ライデイ氏は、「測定はプロセスであり、合理的なサブグループの助けがあれば、どんなプロセスでも研究できる」と述べています。 EMP スタディは、R&R キャリブレーションスタディとほぼ同じように始まりますが、可能なすべての推定値を計算する代わりに、サブグループ平均と範囲の XbarR 管理図にデータをすぐに配置して、データ内で何が起こっているかを発見します。
ソフトウェアの合理的なデータ グループ化機能の説明を参照してください。
- シューハート管理図 プロアナリスト+AI
サブグループ平均と範囲の XbarR 管理図を実験データとともに使用すると、その管理図で通常行うこととはまったく異なることを行うことになります。 XbarR サブグループ平均および範囲グラフが連続プロセス進行データとともに使用される場合、それは適切には「プロセス動作グラフ」と呼ばれます。そこでの目標は、プロセスを予測可能または予測不可能として分類することです。対照的に、EMP 研究では、特別な種類の実験の結果を調べます。ここでは、測定誤差による不確実性にもかかわらず、部品間の差異を検出できるかどうかを判断しようとしています。データの性質と私たちの質問の性質の両方におけるこの変化は、EMP 研究のサブグループの意味と範囲の XbarR チャートが解釈される方法を変えるでしょう。
EMP アプローチはさまざまなデータ構造やデータ収集スキームに適応できますが、ここでは校正テスト (ゲージ R&R) で使用されるのと同じデータ収集戦略を使用した基本的な EMP 調査を説明します。単純な完全交差実験は、2 人以上のオペレーターが 3 ~ 10 個の部品をそれぞれ 2 ~ 3 回測定することで実行されます。この例では、6 人のオペレーターが 4 つの部品をそれぞれ 3 回測定した EMP スタディを使用します。
この測定システムは、特定の製品の電磁特性を測定する手持ち式テストベンチで構成されています。この手動テストベンチは生産現場で全数検査のために使用されるため、プラントの運用にとって非常に重要です。このテストは 6 人のオペレーターが定期的に実行しているため、6 人全員が EMP 研究に含まれていました。研究で使用された 4 つの部分は、4 つの異なる日のいずれかの製品ストリームから選択されました。
Richard Lyday は通常、各オペレーターが各ラウンドで各部品を 1 回測定し、2 回または 3 回のラウンドでデータを収集しました。ただし、主観的または複雑な測定の場合は、オペレーターが特定の項目をいつ再テストしているのか、テストの順序が何らかの方法でシャッフルまたは「ランダム化」されているのかをオペレーターが認識できないように、実験を「ブラインド」にする必要がある場合があります。
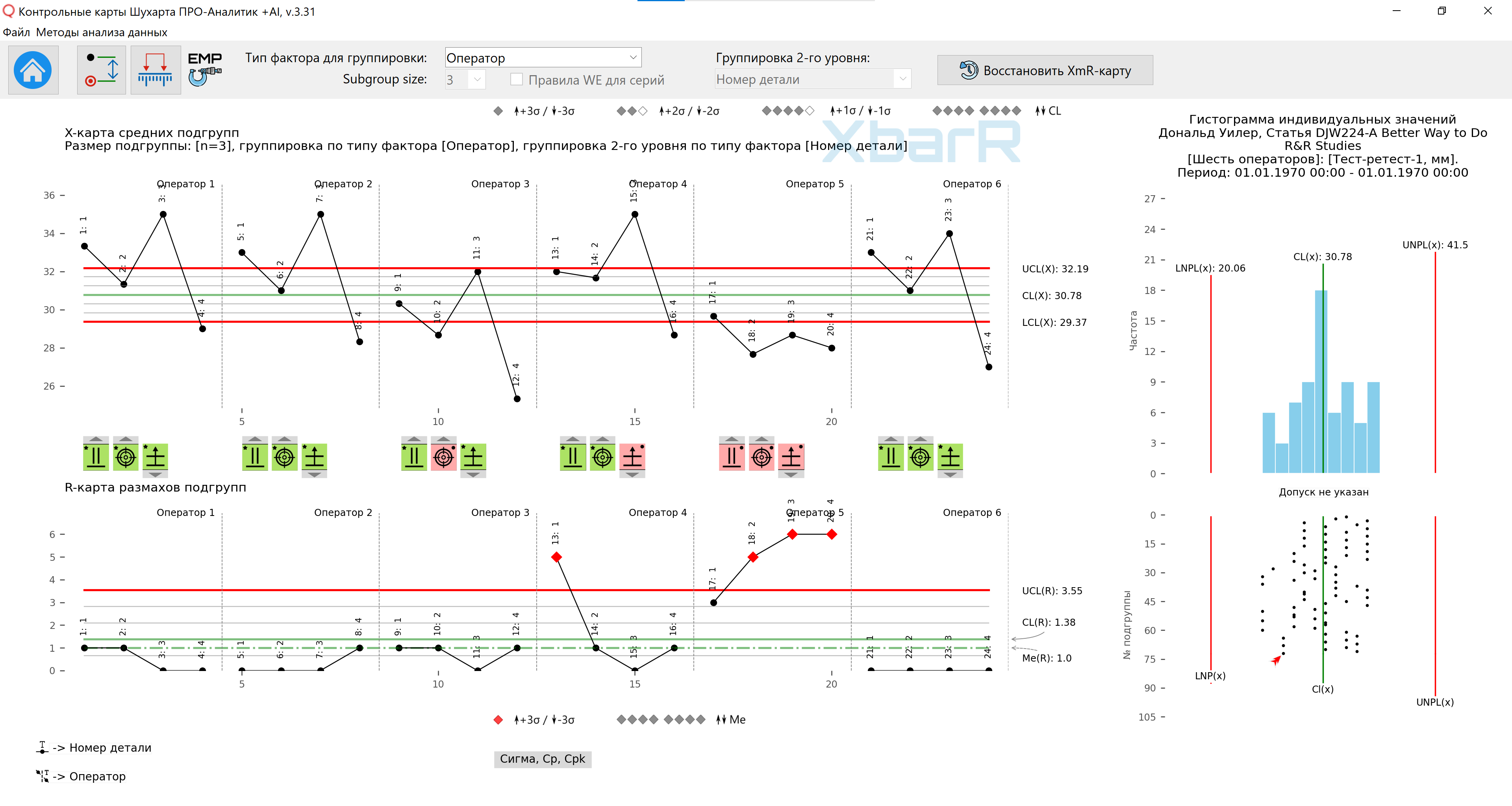
図 1: 手動テストベッドの EMP (並列性、位置、一貫性) の調査。当社のソフトウェアを使用して作成された図面 シューハート管理図 PRO-Analyst +AI 。
サブグループの平均と範囲の XbarR 管理図を理解する鍵は、サブグループ内にどのような変動源があるのか、またサブグループ間ではどのような変動源があるのかを理解することです。図 1 は、変動の 3 つの異なる原因を示しています。1 つは平均値マップのサブグループ間に現れる演算子と部品間の差異、もう 1 つは範囲マップのサブグループ内に現れる反復測定間の差異です。
サブグループ内で見つかるテストと再テストの変動は、一般に再現性と呼ばれます。範囲グラフにおけるサブグループ内の検査 - 再検査エラーと、サブグループ平均グラフにおけるサブグループ間に現れるその他すべての変動要因の分離は、EMP 研究の特徴です。この再検査誤差の分離のため、図 1 のサブグループ平均と範囲の XbarR 管理図に示されている管理限界は、再検査誤差のみに依存します。したがって、図 1 の管理限界は、測定誤差のみに起因すると考えられる変化量を具体的に示しています。
いつものように、サブグループ平均の Xbar 図はサブグループ間の差異を探しますが、サブグループ範囲の R 図はサブグループ内の一貫性をテストします。このグラフの特徴は、図 1 の範囲グラフがこれら 24 のサブグループを調べて、表示される再テスト エラーのサイズに矛盾があるかどうかを確認することを意味します。スパン管理上限を超える範囲値は、再テストエラーの不一致を示します。このような不一致は測定手順自体に重大な問題があることを示すため、これらの問題の理由を研究する価値があります。
平均値とサブグループ範囲の管理図の境界は堅牢であるため、範囲の R マップに一貫性がないにもかかわらず、平均値の X マップを使用して部品と演算子間の差異を推定することもできます。まず、パーツごとのバリエーションについて説明します。
パーツ間の違いはパーツの選択方法によって異なります。製品フローから特定の時間間隔で部品が選択される場合があります。別のケースでは、部品は単に製品の流れからランダムに選択されることもあれば、特定の期間中に起こり得る部品の違いを表すために意図的に選択されることもあります。部品の選択方法に関係なく、測定誤差による不確実性にもかかわらず、部品間の差異を検出する必要があります。これは、平均サブグループの X マップ上でコントロール境界によって形成される領域の外側にある点を見つける必要があることを意味します。すべて同じになるように部品を選択するまでは、管理限界外の点を見つけることを期待することになります。 Xbar 平均チャートを使用すると、部品間の変動と測定の不確実性を視覚的に比較できます。部品間の変動はバンドの幅で表され、最小値と最大値の平均値によって決まります。測定誤差は、平均サブグループ マップの制御境界間の帯域の幅で表されます。したがって、管理限界間の帯域の幅に対して平均値がカバーする帯域が広ければ広いほど、測定誤差にもかかわらず製品のばらつきを検出することが容易になります。
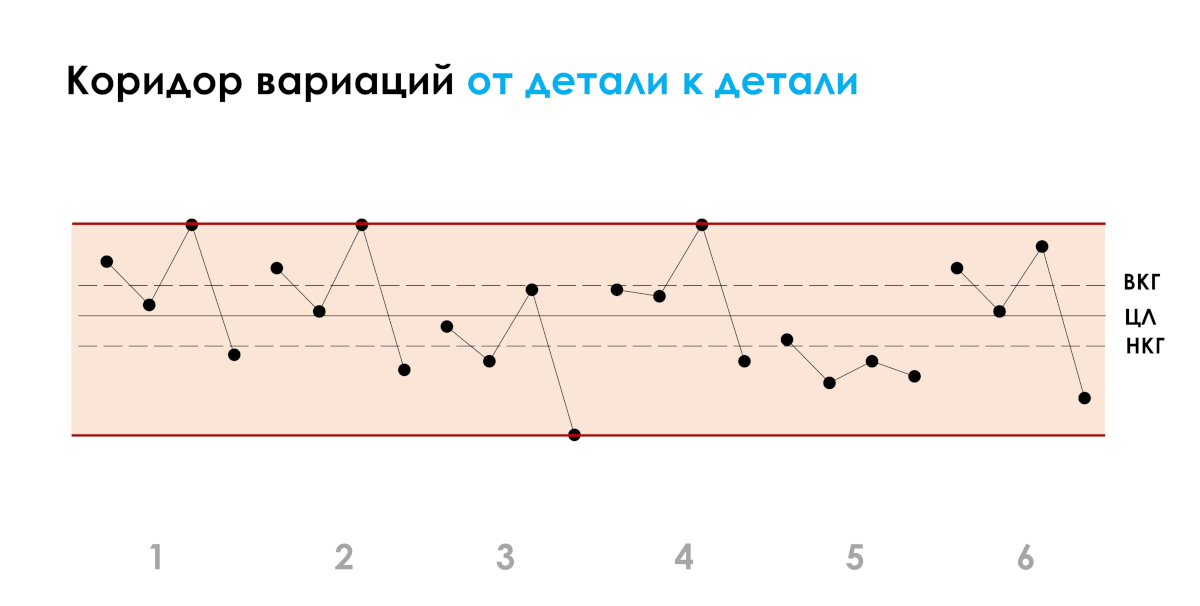
図2.1。部分から部分へのバリエーションの回廊。
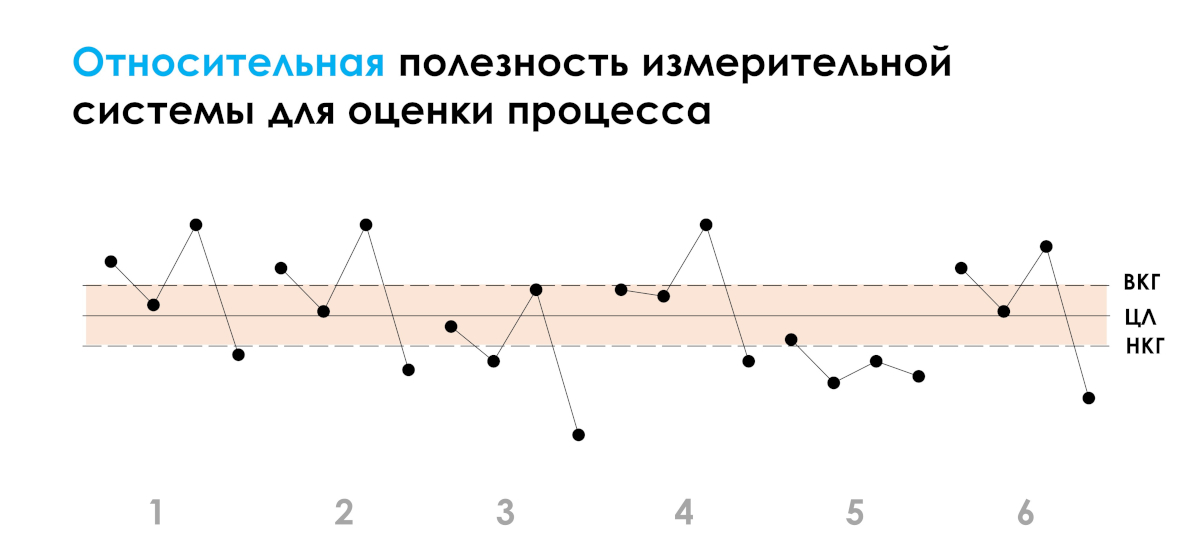
図2.2。サブグループ平均のコントロール X マップによって実証される、測定システムの相対的な有用性。
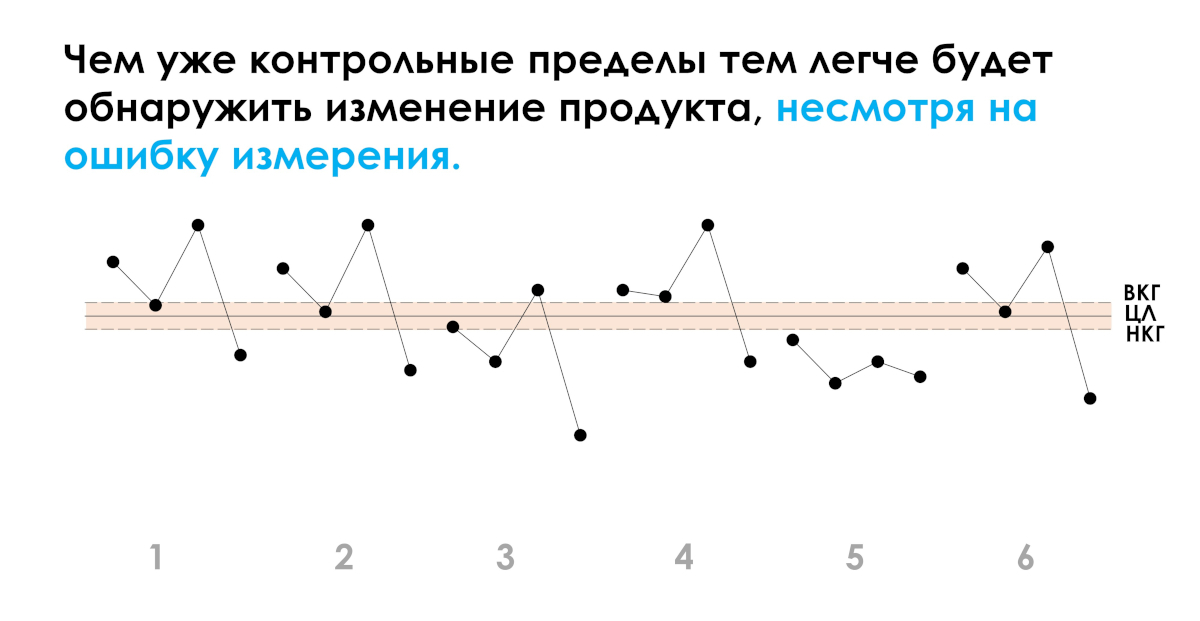
図2.3。管理限界が狭いほど、測定誤差があっても製品の変化を検出しやすくなります。
同時に、部品間の差異を検出したい場合、演算子間に差異がないことが望ましいと考えられます。平均マップを使用して演算子の違いをテストするには 2 つの方法があります。 1 つ目は値の推移の形式 (平行性) を使用し、2 つ目は値の推移の位置 (位置) を使用します。これらの両方の比較を容易にするために、EMP スタディでは、ある演算子から別の演算子に点を接続する線分が非表示になります。
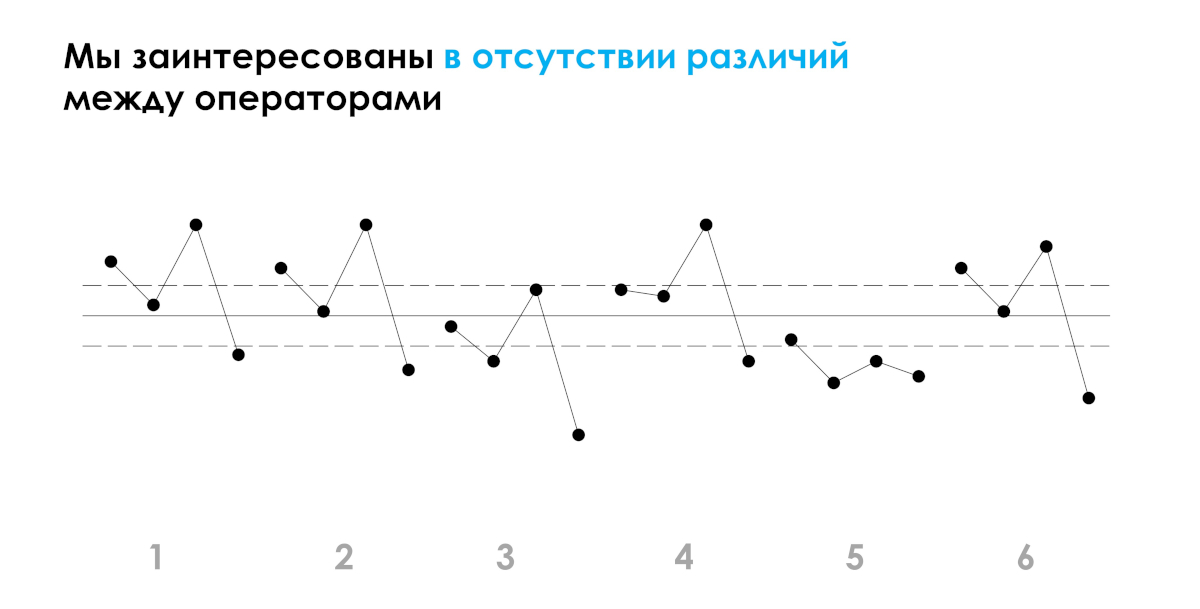
図2.3。平均マップを使用して演算子の違いをテストするには 2 つの方法があります。
値の形状を解釈する方法を確認するには、演算子間に差がなく、測定誤差がない場合にサブグループ平均のプロットがどのようになるかを検討することから始めると便利です。これらの条件下では、各演算子の値の進行の形式はまったく同じになります。セグメントごとに見ると、図 3 の演算子 1 と 2 の曲線のように、それらは互いに完全に平行になります。しかし、何が起こっているのかを把握するために測定誤差を導入すると、完全な平行性からわずかな偏差が見られ始めます (演算子 4 と 6 の曲線に似ています)。適度な並列性がある限り、心配する必要はありません。ここで、演算子 1、2、3、4、および 6 は、適切な程度の並列処理を示しています。一方、ステートメント 5 は並列性が著しく欠如していることを示しています。
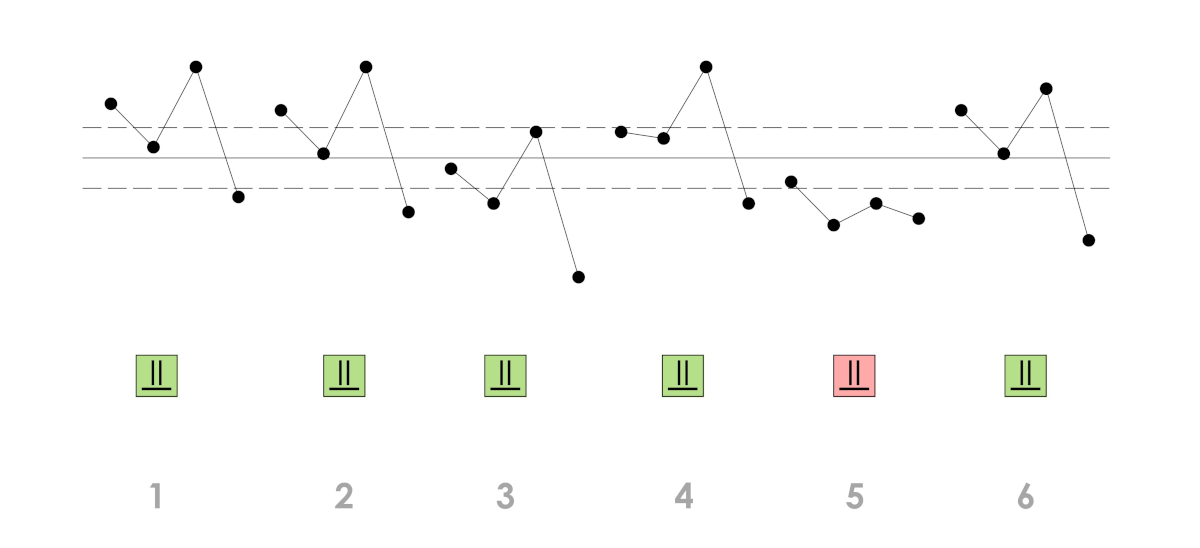
図 3. ステートメント 5 には並列処理がありません。
では、並列性がないとは何を意味するのでしょうか?重度の非並列性は、オペレータと部品間の相互作用の影響を示します。 (代数的には、相互作用効果と非並列性は同じものです。非並列性がなければ相互作用効果は不可能であり、その逆も同様です。) ここでは、演算子 5 がこれら 4 つの詳細を大幅に異なる方法で測定していることがわかります。オペレータと部品の間に相互作用の影響があってはいけないため、この相互作用は測定プロセスにおける重大な不一致を表しており、直ちに対処する必要があります。このような相互作用効果は、オペレーターが異なる方法を使用すること、一部のオペレーターが測定手順のステップをスキップすること、または単に 1 人以上の訓練を受けていないオペレーターの存在によって引き起こされる可能性があります。しかし、理由が何であれ、測定プロセスに問題があるので修正する必要があります。
同時実行性のチェックに加えて、レコードの進行状況の位置 (位置) を比較することもできます。これを行うとき、基本的には演算子の平均を比較することになります。図 4 では、演算子 3 と演算子 5 の両方の平均値が、他の 4 つの演算子の平均値よりも大幅に低いことがわかります。演算子の平均値間のこのような差異は、潜在的な演算子のバイアスとなります。
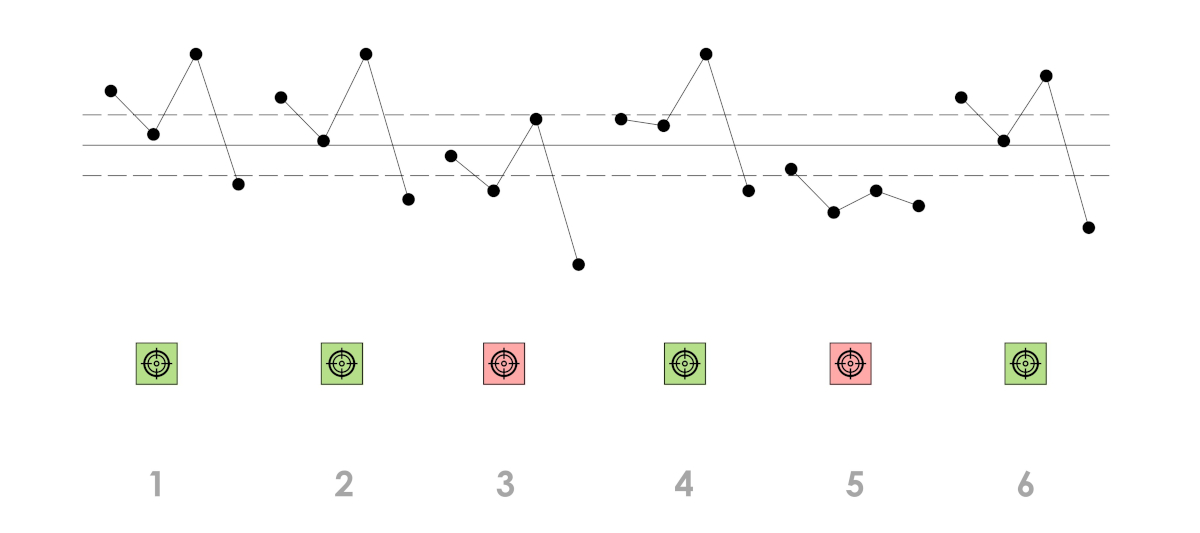
図 4. 演算子 3 と 5 の潜在的なバイアス。
測定プロセスの研究データに従って構築された、サブグループの平均と範囲のコントロール XbarR チャートは何を示しているのでしょうか?下の写真をご覧ください。
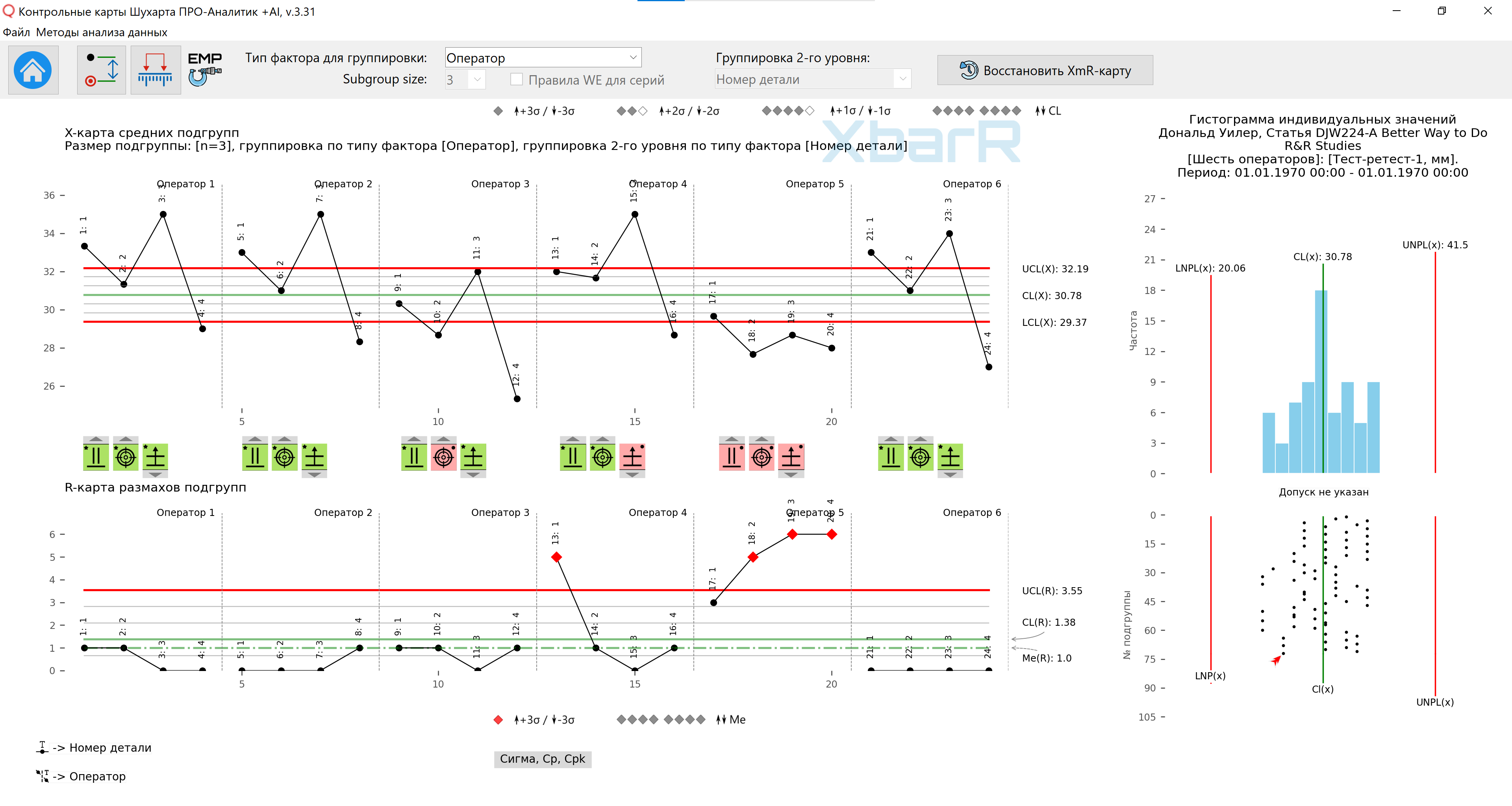
図 5. 手動テストベッドの EMP (並列性、位置、一貫性) の調査。当社のソフトウェアを使用して作成された図面 シューハート管理図 PRO-Analyst +AI 。
では、図 5 の EMP 図の全体的なメッセージについて何が言えるでしょうか?演算子 1、2、および 6 は良好な並列性を示し、サブグループ平均の Xbar チャートでこれら 4 つの詳細の平均値 (位置) が類似しており、サブグループ範囲の R マップでの再テスト誤差の一貫性 (再現性) を示しています。制約幅をこれら 3 つの値ストリーム (ステートメント 1、2、および 6 のデータ) と比較すると、手動テストベッドが製品の変更を検出できることがわかります。
演算子 3 は、Xbar チャートでは良好な並列性を示し、R 範囲マップでは再テスト エラー サイズが小さいことを示していますが、Xbar マップではすべての次元にわたって一貫して低い値です。これはオペレータの潜在的なバイアスです。この変化の原因を特定して除去する必要があります。
演算子 4 は適度な並列性と Xbar マップ上の平均値を備えていますが、範囲 R マップの上限を超える点があります。明らかに、パート 1 の彼の次元の 1 つ (サブグループ内の 3 つの次元) に問題があります。 R マップ上の他のサブグループ スパンと Xbar マップ上の妥当な並列性は、一般的に良好な結果を示していますが、この異常な測定の理由を特定する必要があります。
演算子 5 は、R マップ内のサブグループ スパンが大きく、並列処理が不十分で、Xbar マップ内の 4 つの部分の平均が不正確です。彼についてなんと言うと、彼は明らかに手動テストベンチの使い方を知りません。オペレーター 3 と 4 は、測定スタンドを使用する際に再訓練が必要な場合がありますが、オペレーター 5 は、デバイスの使用方法を学び、他のオペレーターが示す熟練度に匹敵するレベルを実証できるようになるまで、再割り当てされる必要があります。
もちろん、最初のステップは、オペレーターに同じ方法で測定してもらい、現在は測定していないことを納得させることです。オペレータ 3、4、5 は、オペレータ 1、2、6 と同じ方法でこれらの部品を測定していると考えている可能性があります。図 5 を示すことは、そうではないことを納得させる最初のステップです。
それで、私たちは何を学んだのでしょうか?
EMP 調査は、R&R 調査データをサブグループ平均と範囲の XbarR 参照チャートに配置することから始まります。このおかげで、具体的な計算を開始する前に、いくつかの定性的な推定を行うことができます。
- サブグループ範囲の R マップを使用すると、検査と再検査の誤差が研究全体で一貫しているかどうかを判断することができ、また、それがオペレーターごとに一貫しているかどうかも判断できます。テストと再テストのエラーに一貫性がない場合は、その理由を解明する必要があります。
- サブグループ平均の Xbar チャートを使用すると、測定プロセスで製品のばらつきを検出できるかどうかを示すことで、測定システムの相対的な有用性 (適合性) を評価できます。
- 平均サブグループの Xbar チャートを使用すると、演算子間の非並列性を判断できます。顕著な非平行性はオペレーターと部品の間の相互作用の影響を示しているため、測定プロセスにおける重大な不一致を警告します。
- 平均サブグループの Xbar チャートを使用すると、検出可能な演算子のバイアスの可能性を推定できます。このような症状が存在する場合は、測定プロセスを最大限に活用するために対処する必要があります。
EMP 管理図を作成する頃には、データに何が起こっているかがわかるようになります。興味深い質問をすることができ、問題が存在するかどうかを知ることができます。データ分析の基本原則の 1 つは、常にデータのグラフから始めることです。計算はグラフを補完するために存在しますが、グラフを置き換えることはできません。計算値のみに依存すると、データの多くの興味深い側面を見逃してしまう可能性があります。
分析の目的は理解することであり、最良の分析とは、必要な理解を提供する最も単純な分析です。また、何かを発見しても、それを他の人に伝えられなければ意味がありません。 EMP 研究では、グラフィカルな手法を活用して発見とコミュニケーションの両方を支援します。
私たちの中で 研修セミナー 当社の計測システムを用いた評価方法の本質をわかりやすく解説します。 ソフトウェア 。
当社のソフトウェアでは 「シューハート管理図 PRO-Analyst +AI(Windows、Mac、Linux用)」 以下の測定システム評価機能を利用できます。
-
安定した測定システムの誤差推定。
-
シューハート制御カードによって検出された測定システムの変位を確認します。
-
測定システムの有効増分(増分)の決定。
-
測定プロセス (EMP) の評価。