生産プロセスと作業の配給 (タイミング) という誤った慣行に対する統計的プロセス管理 (SPC)。また、シューハート管理図が生産計画の改善にどのように役立つかについても説明します。
資料作成者: AQT センター科学ディレクター セルゲイ・P・グリゴリエフ 。
記事への自由なアクセスは、記事に含まれる資料の価値を決して減じるものではありません。
「品質ベースの管理は、マネージャーの役割に対する理解を大きく変えます。マネージャーは、従業員が効率的に働けるシステムを構築することを主な任務とするリーダーにならなければなりません。この役割を遂行するために必要な条件は、リーダーが変動の一般的な原因と特殊な原因の違いを理解することです。」
プロセスとオペレーションに広く適用されている標準化手順は、標準化される作業の変動性の性質を完全に無視しています。このため、標準化される作業の状態の違い、つまり統計的に制御されている (予測可能な動作) か統計的に制御できない (予測不可能) かの違いを考慮して、標準化者と管理者について話すことさえ意味がありません。
ちょっと考えてみましょう!ランダムな時点でプロセスまたは操作の点推定を行うことで「正規化」し、このデータを計画と制御に使用します。
完全な混乱状態では、配給は、何も知らないプロセスについてある程度の洞察を得るのに役立ちますが、プロセス改善の障壁として機能します。標準化された指標が満たされているのに、なぜわざわざプロセスを改善するのでしょうか?従わない場合は、「有罪転轍手」の権利を剥奪し、罰金を科します。規範が良い方向に重なる場合、私たちは「関係者」に報酬を与え、おそらくは「規範」を厳格化する方向に修正します。
質問に答えてください: グラフ (図 1.) にプロセスの 1 つの重要な出力、たとえばシフトごとの出力が表示されている場合、縦軸のどこに「実際の」目標 (計画、基準、タスク) を設定しますか。次のシフトまたはシフト割り当てのこのインジケーターは? 1 ~ 4 のどのグレー ポイントまたはゾーンですか?答えを覚えておいてください。
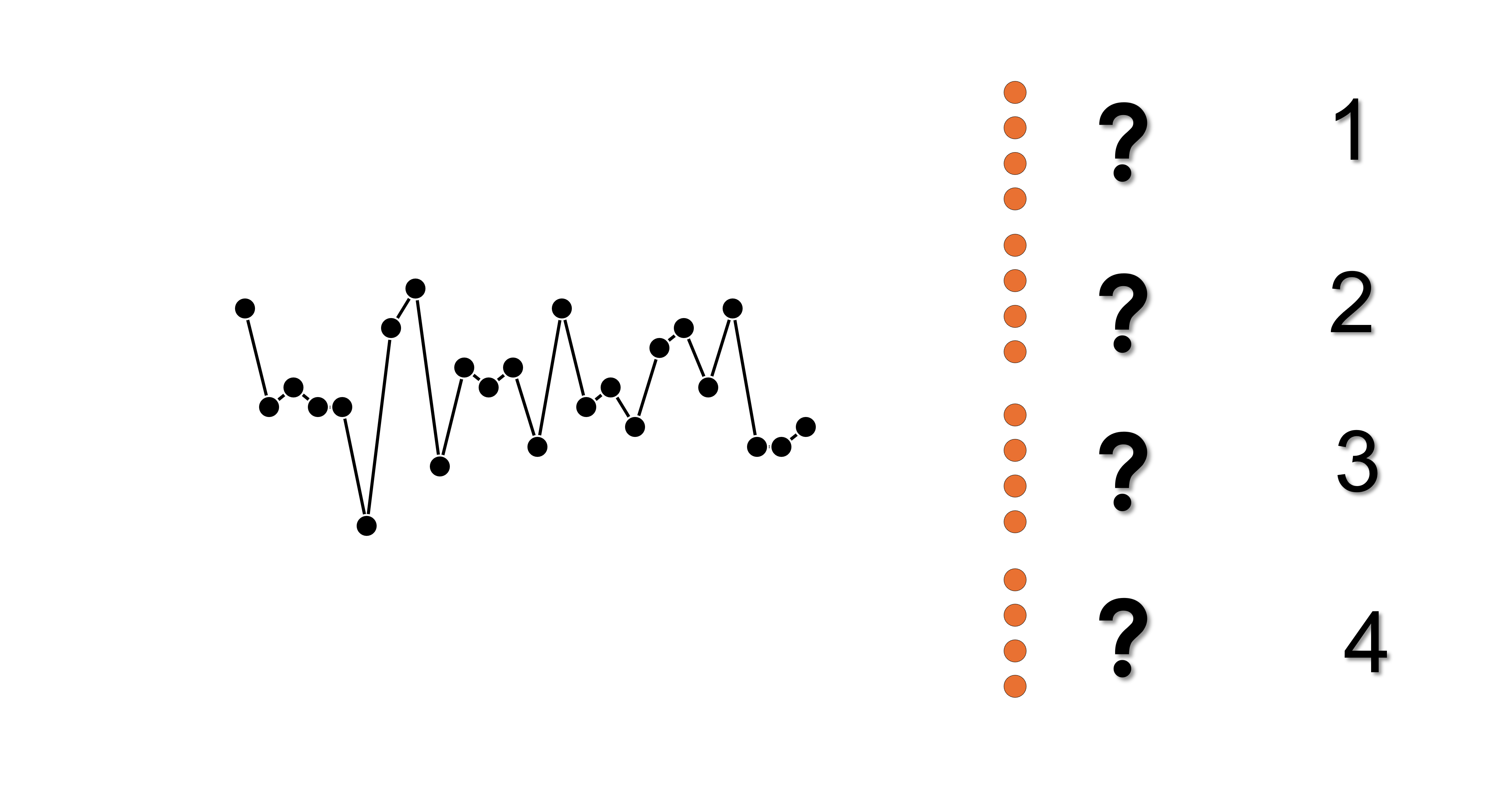
図 1. プロセスのタイムライン。プロセスの「本当の」数値目標はどの灰色の点にあるのでしょうか?
証拠1
「正規化」の対象となるプロセスは、統計的に管理された状態にあります。ゾーン 2 または 3 でターゲットを選択した場合:
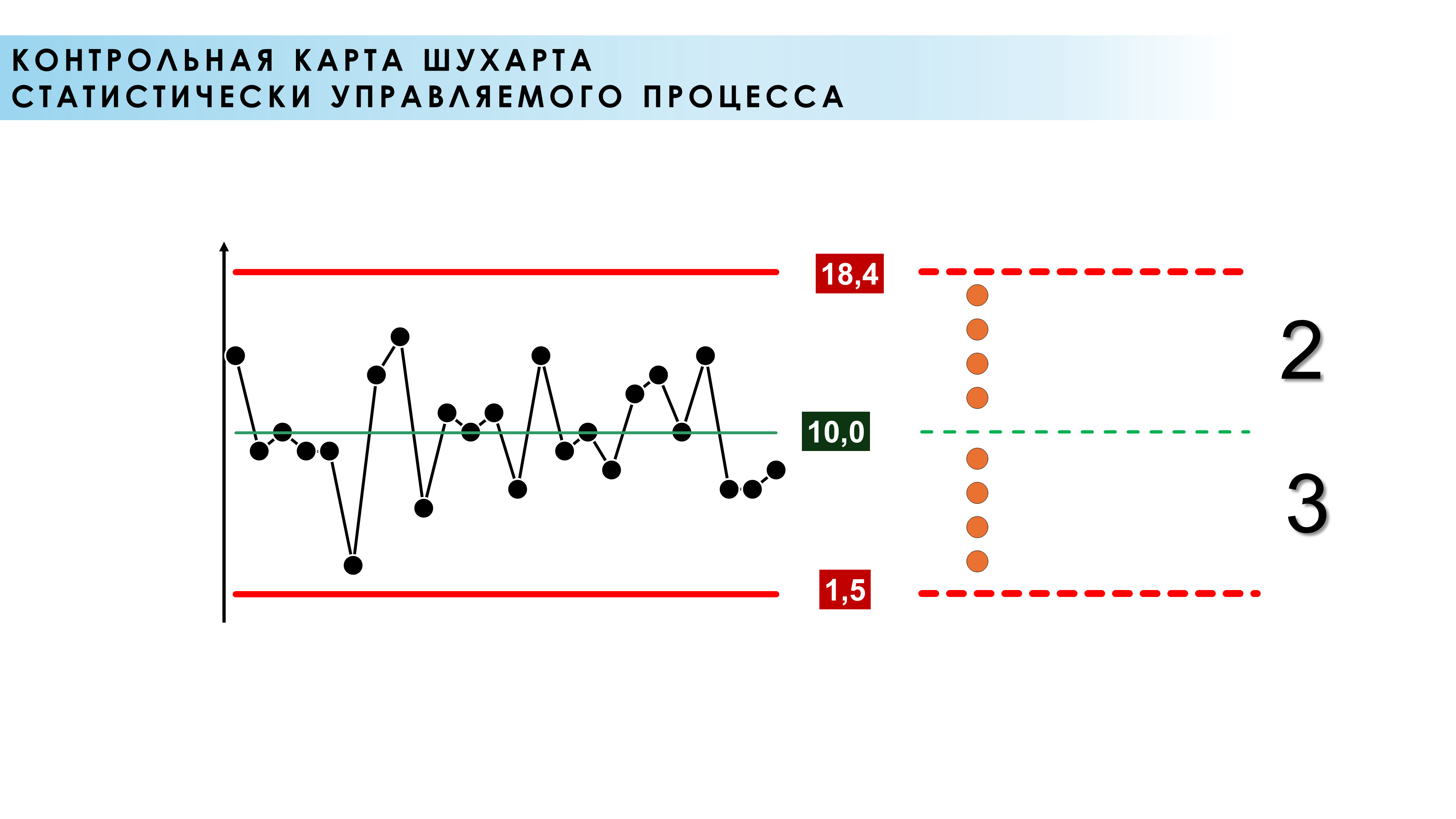
図 2. 統計的に制御されたプロセスのシューハート管理図。ゾーン 2 または 3 のプロセスの数値目標。 CL - 中央線、ВКГ - 上方管理限界、LKG - 下方管理限界
回答: プロセスが妥当な程度の統計的制御を示している場合、プロセスの動作は予測可能であり、プロセスは最良の状態にあります。このようなプロセス (およびそのプロセスに携わる人々) は、できる限りのことを行います (図 2 を参照)。このようなプロセスの過去の挙動に関する知識は、その将来、つまり経験則に従って分布したデータによる管理限界内のランダムな変動を予測するために使用できます (図 3)。この記事の内容をより深く理解するには、まず次の記事を読むことをお勧めします。 変動性(変化、変化しやすさ)の性質は統計的思考の基礎です 。
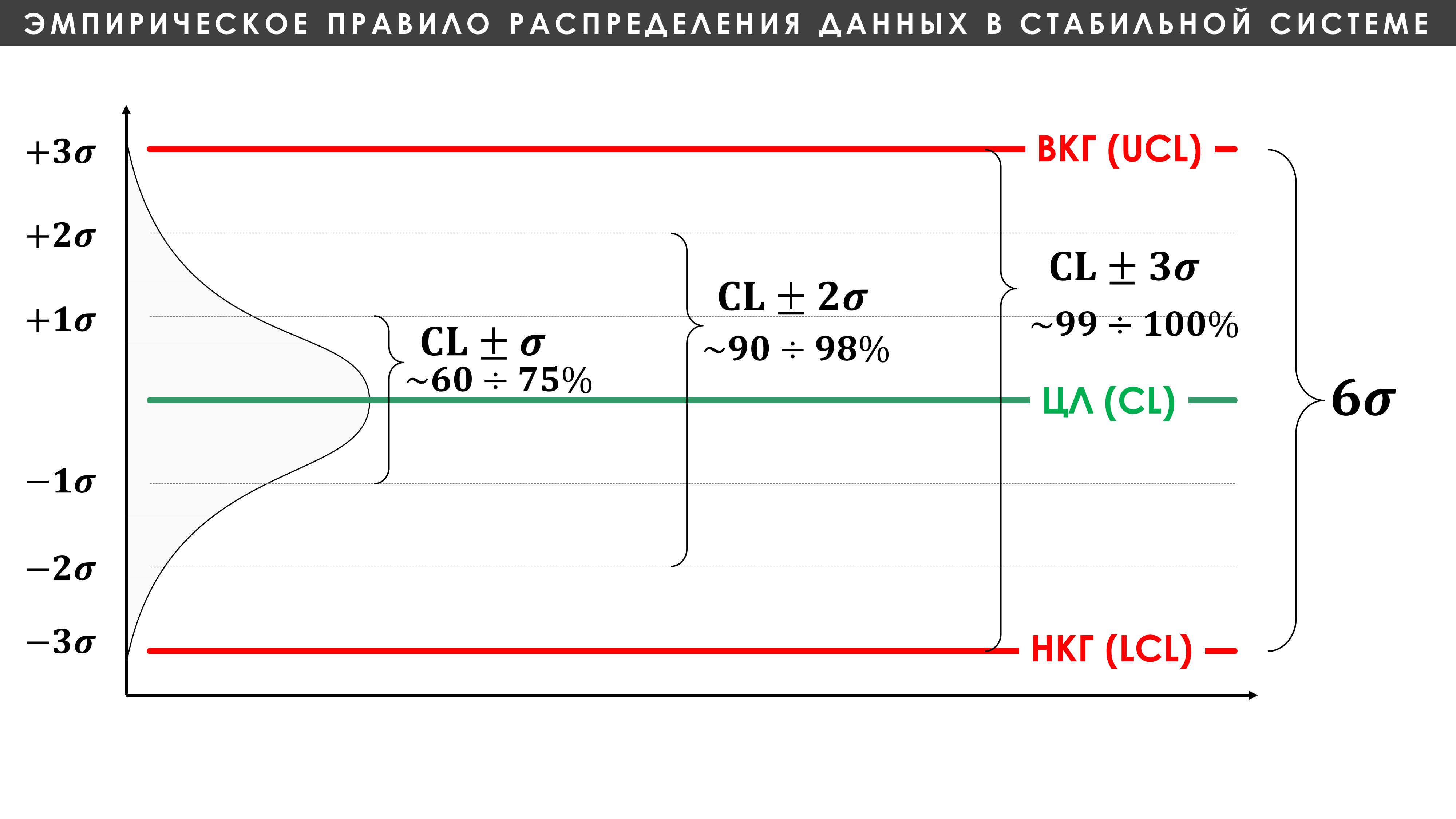
図 3. 安定したシステムにおけるデータ分散の経験則。シューハート管理図。 LCG - プロセスの下限管理限界、ВКГ - プロセスの上限管理限界。
「経験則は、位置の尺度と分散の尺度を使用してデータを記述する便利な方法を提供します。均一なデータのセットが与えられた場合、次のようになります。
1) データの約 60 ~ 75% が平均値の両側の 1 シグマ単位以内にあります。
2) データの約 90 ~ 98% が平均値の 2 シグマ単位以内にある。
3) データの約 99 ~ 100% は平均から 3 シグマ単位以内にあります。
シグマ単位 (σ) は、データのスケールの尺度です。一般的な散乱統計は、公開されている公式* を使用して (σ) 単位に変換できます。
* σ 単位の計算式は、[11.1] GOST R 50779.42-99 (ISO 8258-91) を参照してください。

図 4. 時間の経過とともに変化せず、統計的に制御された状態 (安定したプロセス) にあるプロセスのサブグループの平均と範囲のデータ分布と対応するコントロール XbarR チャート (XR マップ) のデモンストレーション。
考えてみてください。標準化者は、統計的に制御された状態のプロセスを使用して作業を行ったのでしょうか?どうして知っていますか?どの日(地点)ですか?
この場合(図 2)、縦軸に沿った管理限界の上限と下限の間の任意の点で設定される特定の数値目標と基準の形でプロセスの作業に介入することは、限られた範囲内での「ルーレット ゲーム」です。範囲。このようなゲームは計画とは何の関係もなく、ましてやプロセスの改善とは何の関係もありません。
ゾーン 1 または 4 でターゲットを選択した場合:
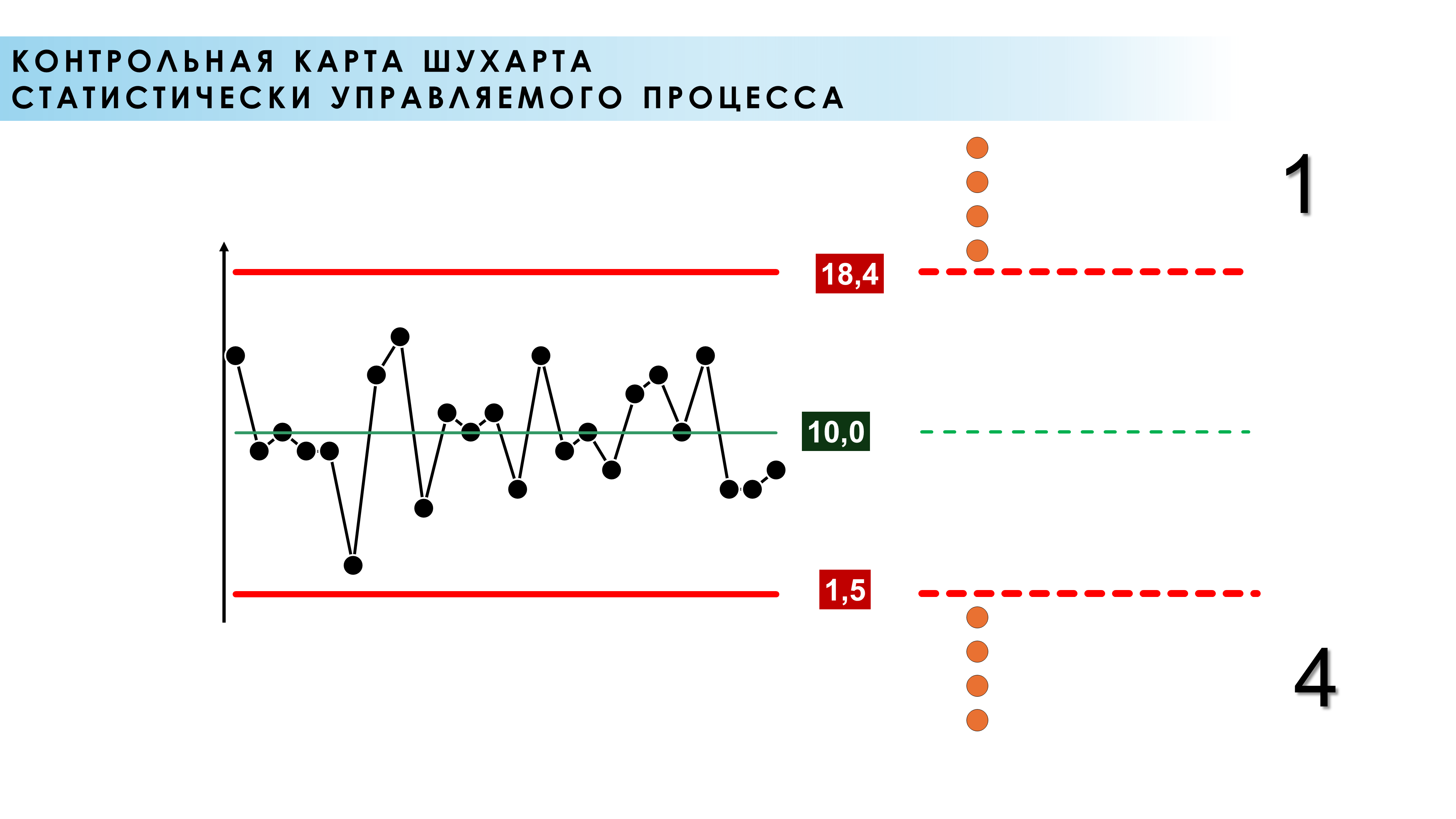
図 5. 統計的に制御されたプロセスのシューハート管理図。あなたが設定した「実際の」数値プロセス目標は、プロセスの自然管理限界の上限または下限を上回りますか (管理限界外)? CL - 中央線、ВКГ - 上限管理限界、LCG - 下限管理限界
統計的に管理されたプロセスの管理限界範囲外の目標は、作業者にとって意味がありません。
目標がシステムの能力より高い場合 (管理上限値を超える場合)、そのような目標は作業者にイライラと不満を引き起こします。同じ条件下で、管理下限値 (ゾーン 4) を下回る発電に対して合理的な管理による計画を立てるというオプションについては、ありそうもない状況として説明しません。
統計的に制御された状態にあるプロセスについて、管理上限値を超えるか下限値を下回る点 (図 5、ゾーン 1 および 4) が期待されるのは、次の 3 つの場合のみです [1]。
1. 単純なデータの歪み。
2. システムの歪み(たとえば、選択した指標 3 などの部分最適化により、他の同様に重要な指標が損なわれる)。図6を参照してください。 (歪み前)と図7。 (歪み後)。
3. 経営者によるシステム(プロセス)の変更。これはまさに企業の経営者が行うべきことです。図 8 と 9 を参照してください。
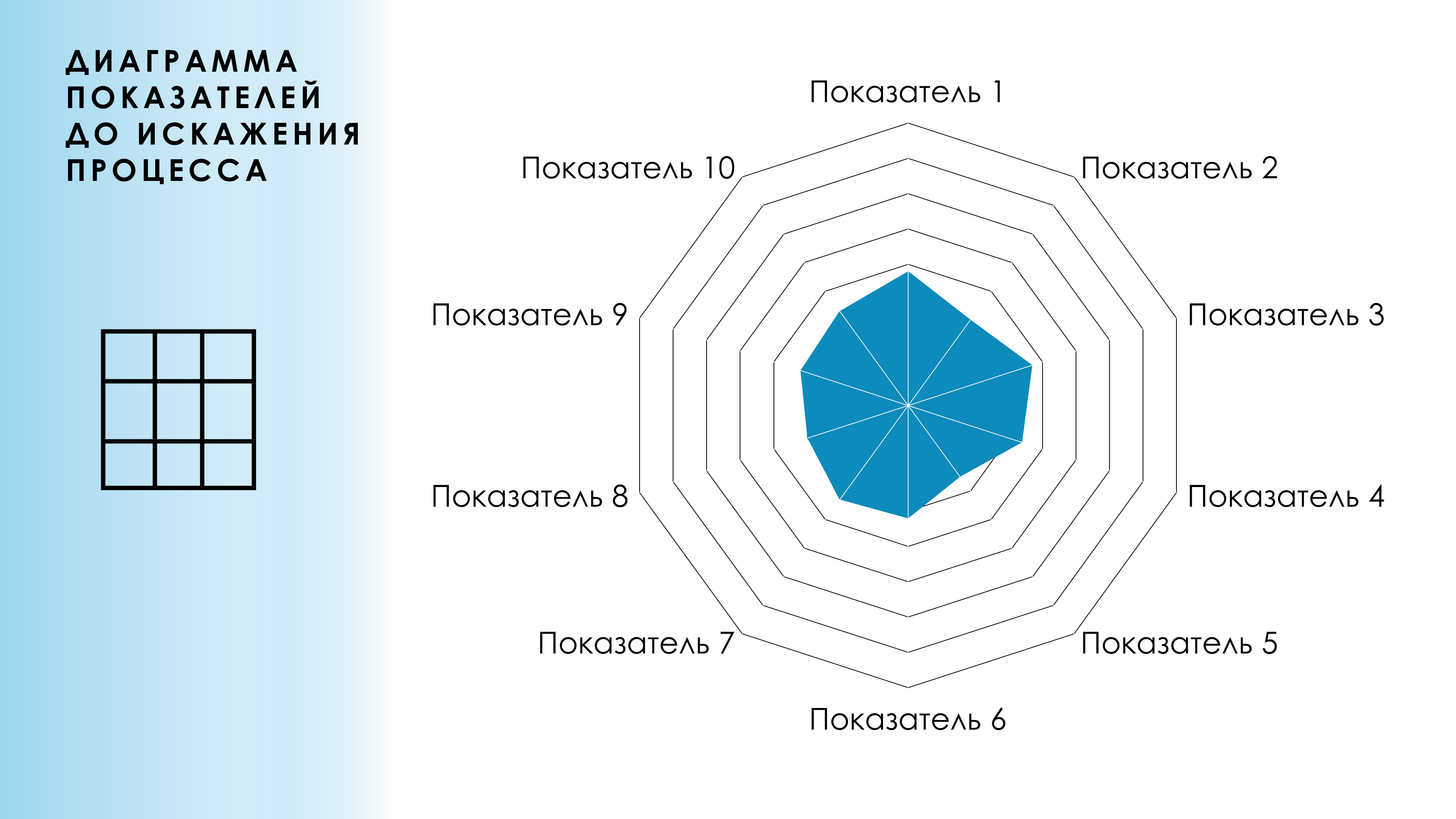
図 6. プロセス歪み介入前の追跡された指標。
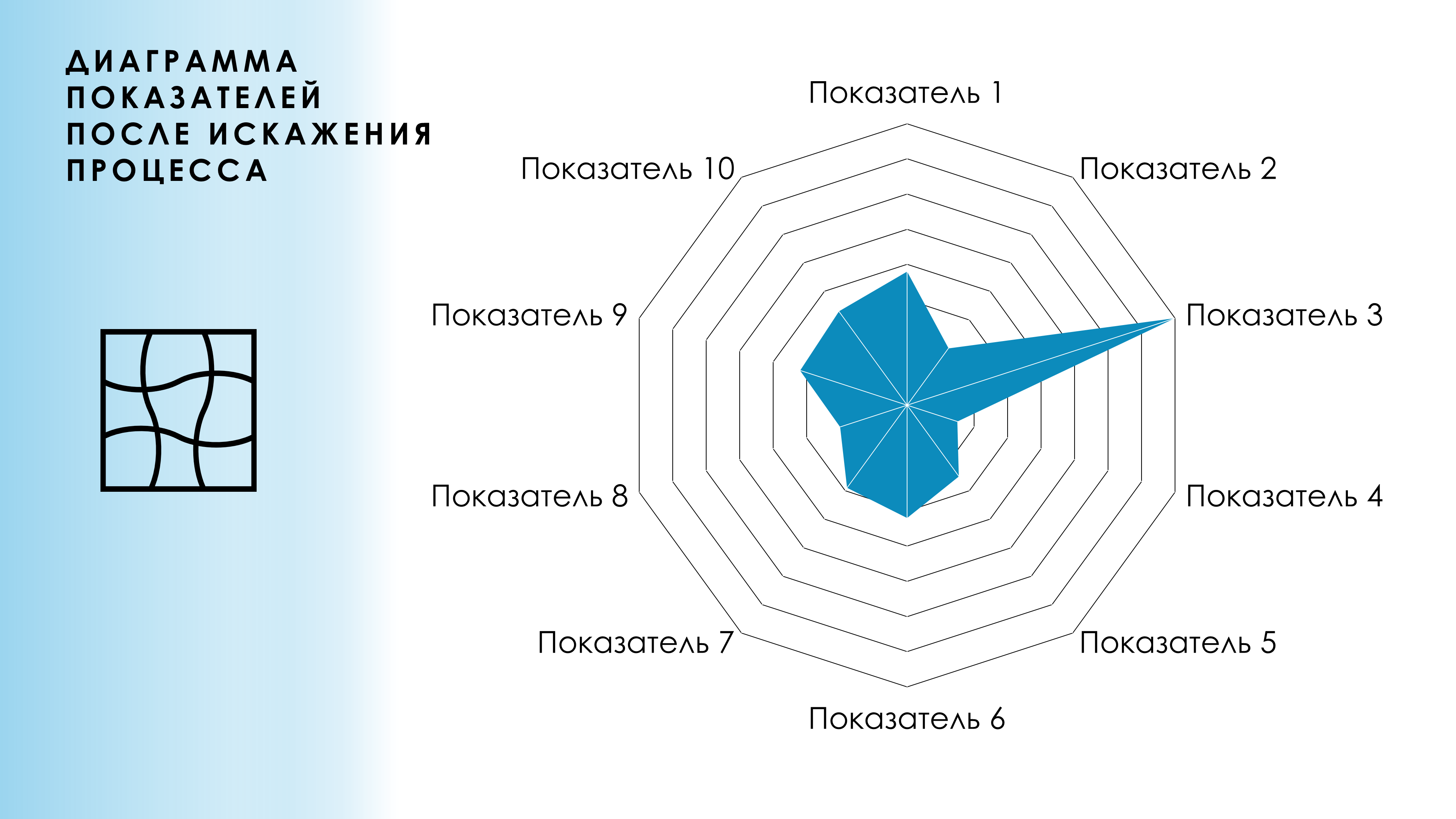
図 7. プロセス歪み介入後の追跡されたメトリクス。
最善の決断
合理的な程度の統計的制御を実証するプロセスにおいて、管理限界の範囲内で観察された平均を上回るまたは下回るランダムな変動を引き起こす特定の原因を探索することは、費用対効果が高くありません。さらなる改善(平均的なプロセスを望ましい目標に向けてシフトし、データのばらつきを減らす)を行うには、プロセス設計のレベルとプロセスへのすべての入力の改善、つまり次のようなシステム上の変更がトップマネージャーの能力の範囲内で必要となります。原材料と材料、設備と工具の技術的条件、人材トレーニング、環境、管理スタイル、技術仕様の完全性と明確さなど。労働者は自分の活動の結果においてこれらの要素に影響を与えることができますか?統計的に管理されたプロセス管理図を使用すると、管理者が行った変更の結果を常に追跡できます。図 8 と 9 を参照してください。

図 8. 統計的に有意な期間におけるプロセス (システム) 変化の評価。変動を一定に減少させながら、平均を上回るプロセスに目標を向けます。
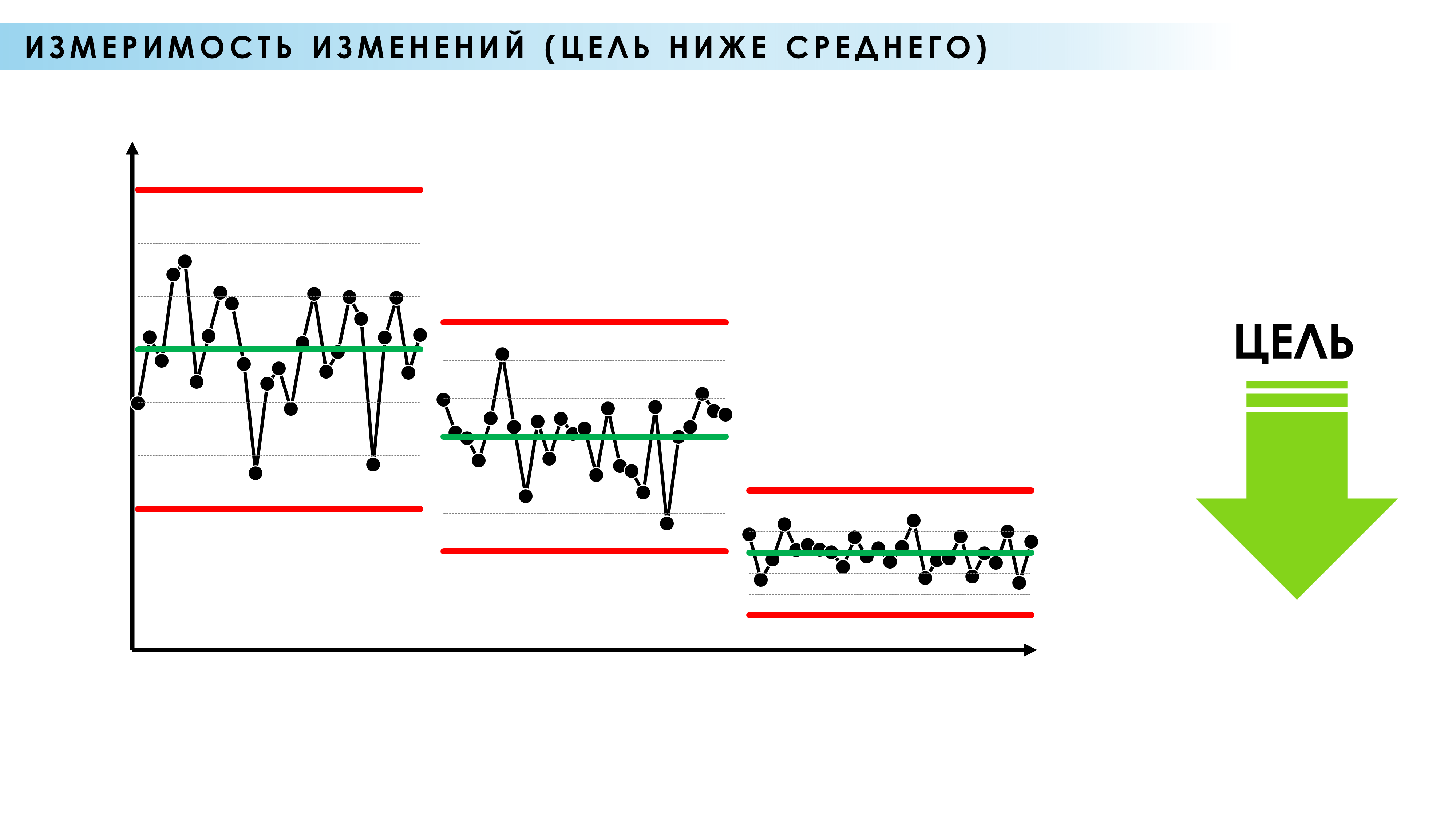
図 9. 統計的に有意な期間におけるプロセス (システム) 変化の評価。ばらつきを常に低減しながら、平均を下回るプロセスに目標を向けます。
配給の話に戻りましょう
私が話をした管理者たちは、労働者が「配給」の際に意図的に「低速」モードを使用しているという事実に常に言及しています。驚くべきことに、科学的な説明はありませんが、労働者は無意識のうちに、自分の仕事に対する偶然の影響を平均より多かれ少なかれ感じています。確かに、経営者は、標準化されたパラメータが経営者が望む方向に平均からランダムに変動することを通常のこととして受け入れるでしょう。そして、平均値の「望ましくない」側における同じランダムな変動は、完全な分析の対象となり、特別な原因が探られます。そして、そこにないものであっても、「求める者は必ず見つけ出す」のです。
企業経営者が変動性の性質を理解していなければ、労働者と経営者が協力する環境は存在できません。その結果、経営者に対する不信感や恐怖感が持続してしまうのです。作業員の恐怖の結果、プロセスの問題(プロセス改善に重要な情報)が確実に隠蔽されることになります。これは、生産業務を標準化するプログラムを開始したときに達成したかったことでしょうか?
実験の説明を参照 「ファネルとターゲット」 そして 「赤いビーズ」 - 変動の性質と一般的な管理慣行の優れたデモンストレーション。
「組織におけるすべての問題(または改善の機会)のうち、変動の特別な原因に関連するものはわずか 6% です。したがって、それらは一般の従業員の活動分野にある可能性があります(ただし、必ずではありません!)。この場合、トップマネージャーは、従業員が働くシステムの潜在的な改善の少なくとも 94 % を占めています。
いかなる制御も、労働者の専門的スキルのレベルも、システムの根本的な欠陥を克服することはできません。」
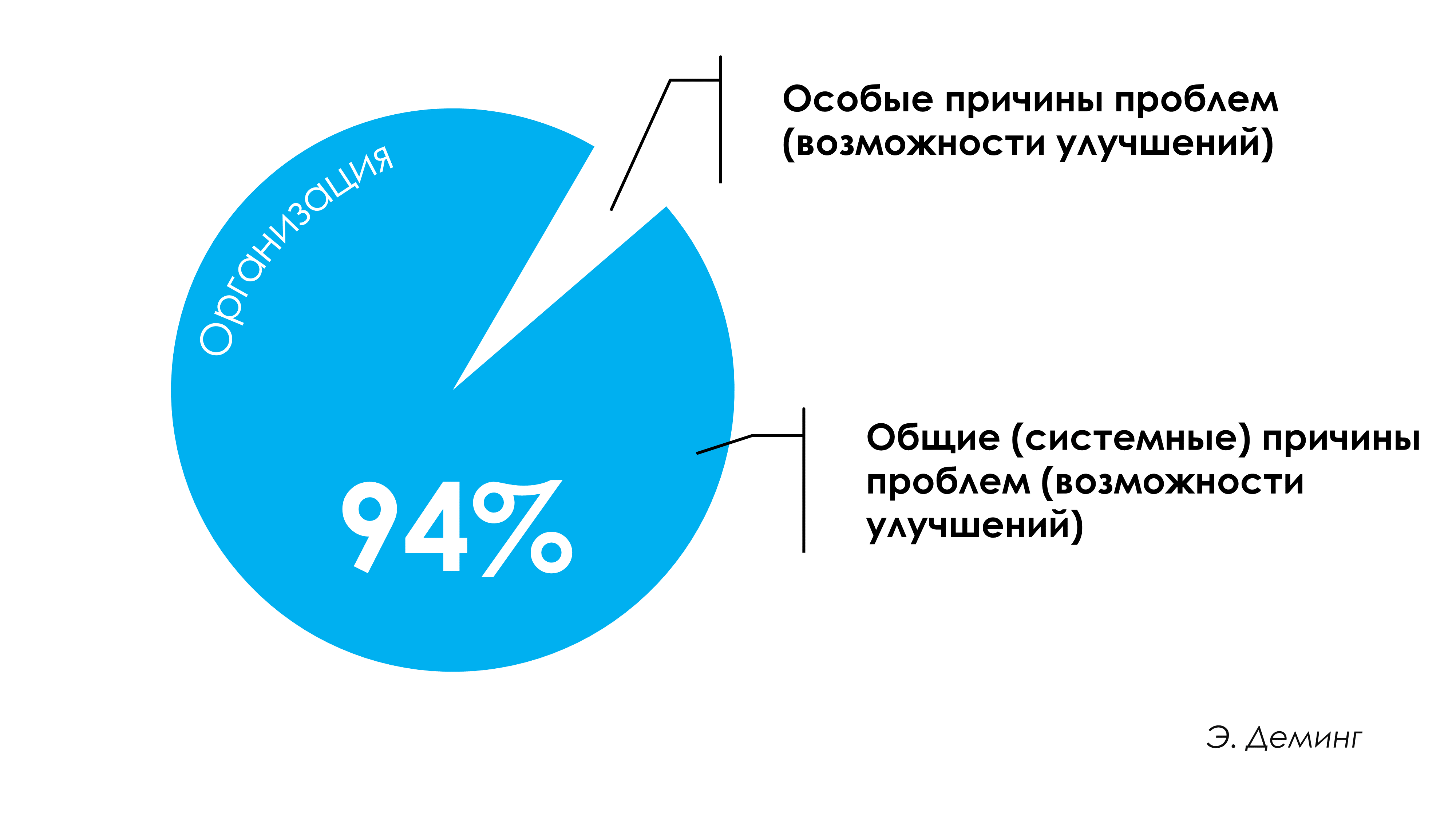
図 10. 経営トップは、従業員の働くシステムを改善する潜在的な機会の少なくとも 94% を占めています。 E.デミング
証拠2
「正規化」の対象となるプロセスは、統計的に制御できない(予測できない)状態にあります。
プロセスが統計的に制御不能な状態を示している場合、その動作は予測できません (以下の図 11 および 12 の管理図を参照)。過去に基づいてそのようなプロセスの可能性を予測し、その再現性を議論することには意味がありません。

図 11. 統計的に制御できないプロセスのシューハートの管理図と、それに対する無意味な数値目標。 CL - 中央線、ВКГ - 上限管理限界、LCG - 下限管理限界。

図 12. 統計的に制御できない状態 (不安定なプロセス) にある時間変動プロセスのサブグループ平均と範囲のデータ分布とシューハート管理図のデモンストレーション。
考えてみてください。標準化者は、統計的に制御された状態のプロセスを使用して作業を行ったのでしょうか?どうして知っていますか?もう一度言いますが、どの日(時点)ですか?
管理されていないプロセスの総コストは、管理者が考慮していないコストも含めて最大になります。このようなプロセスを正常化するのは無謀です。まず第一に、経営者はそのようなプロセスを統計的管理の状態にし、変動の特別な原因を排除する必要があります。その影響は最悪の結果をもたらした点に現れます。より良い結果をもたらすためにポイントが管理限界を超えた具体的な理由を見つける必要があります。おそらくこれは従業員またはその方法の独自性の結果であり、これらの方法が全体的な目標とよく一致しているかどうかを確認する必要があります。ビジネス システムに基づいて、他の従業員をトレーニングすることができます。

図 13. 管理者が考慮していないものも含め、管理されていないプロセスの総コストは最大になります。
では、どのように生産計画を立てるのでしょうか?
「では、基準や具体的な数字の形でのシフト計画がない場合、どうやって生産計画を立てることができるのでしょうか?」と反論する人もいるかもしれません。シューハート管理図を使用してプロセスを研究する場合、単なる恣意的な基準や割り当て以上のものがあります。プロセスがどのような機能を備えているかはわかっており、統計的に制御された状態に保持されているプロセスでは、この能力は予測可能です。より良い解決策のヒントについては、パラグラフ 11 を参照してください。「恣意的な量的基準とタスクを排除する」 エドワーズ・デミングのマネジメントの14のポイント 。
計画には、「何もないところから引き出された基準」やランダムに得られた測定結果ではなく、安定したプロセスの能力、生産性の平均とばらつき(たとえば、時間あたりの製品数)に関する知識を使用する必要があります。 (平均値付近のデータ分布の形状に関係なく) 適度な統計的制御可能性を示すシステム内のデータ分布に関する経験則を理解します (上記の図 3 を参照)。
もちろん、これは役員室での次の会議で望ましい「数字」を考え出すよりも困難です。統計的プロセス管理の分野の専門家を雇い、プロセスの特性の研究に取り組み、オフィスから作業場、作業場へと足を運ばなければなりません。しかし、これは間違いなくより効果的です。
例えば、ライン状につながった工程の生産チェーンにおけるボトルネック(最も生産性の低い工程)の生産性の平均値に基づいて計画オーダーが実行され、統計的に管理された状態を示します。
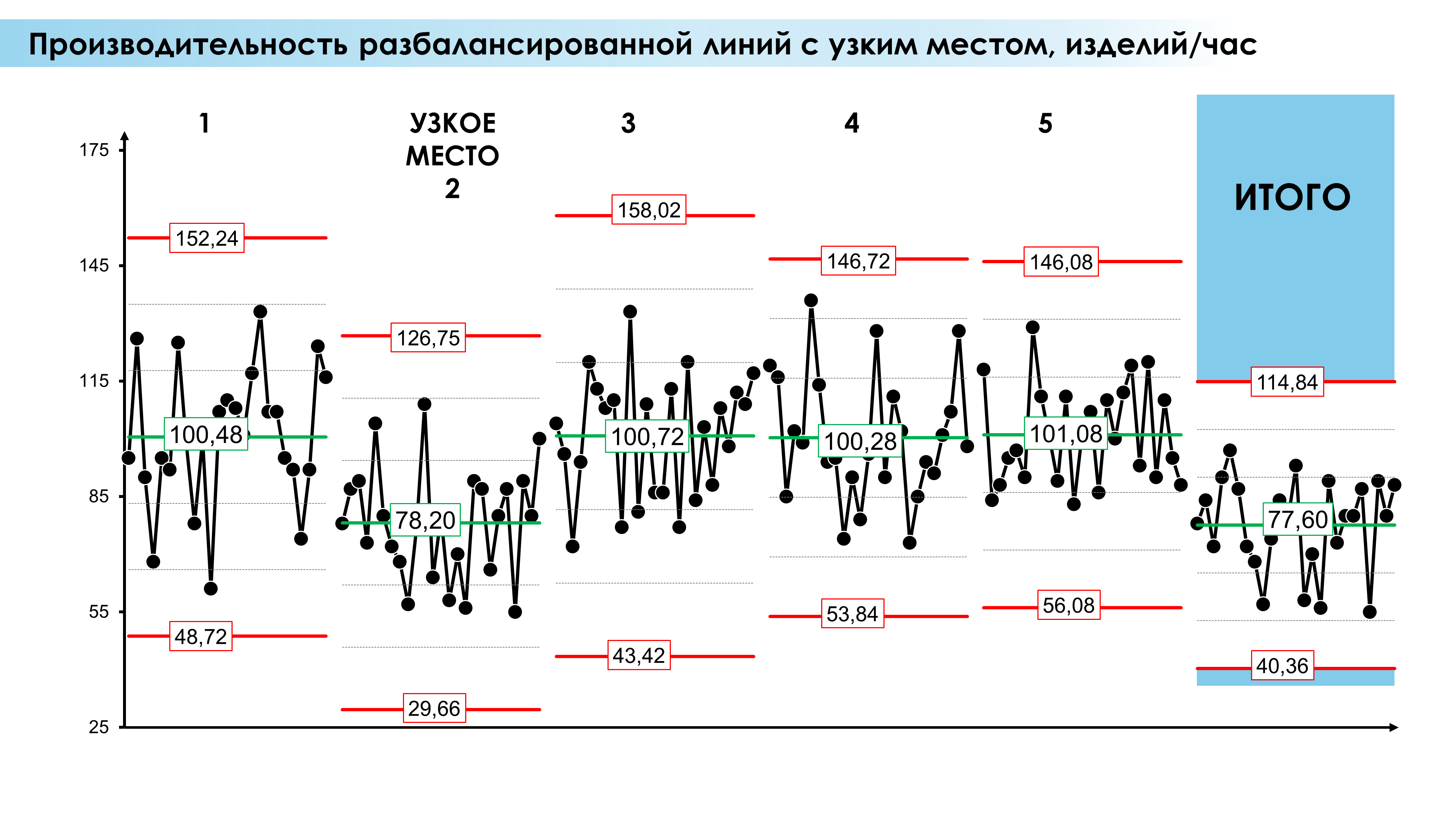
図 14. シューハート管理図を使用して実証された、ボトルネックのある不均衡な生産ラインの結果としてのパフォーマンス。シミュレーション方法に関して、アンバランスなラインのパフォーマンスを分析する方法は、Donald Wheeler と David Chambers の著書から借用されました。 「統計的プロセス管理: シューハート管理図を使用したビジネスの最適化」、366 ~ 370 ページ [4]。図面は当社が開発したものを使用して作成されました 「シューハート管理図 PRO-Analyst +AI(Windows、Mac、Linux用)」 。
一連のプロセスのボトルネックは、そのようなプロセスの前に最大の相互運用ストックが存在するかどうかによって簡単に判断できます。
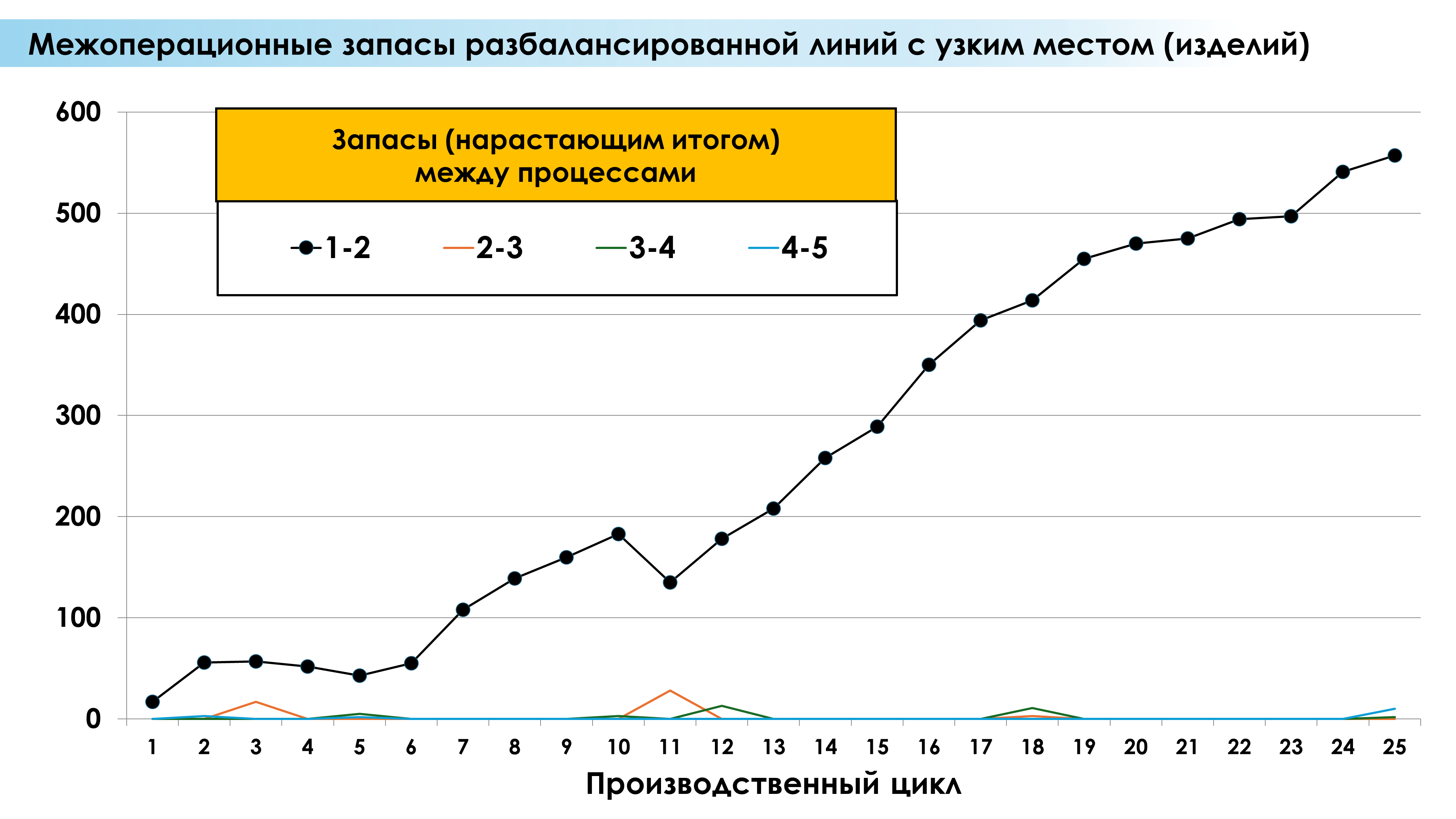
図 15. ボトルネックのある不均衡な生産ラインにおけるボトルネック前の相互運用可能な在庫の蓄積のグラフ。
シフトごとに量を計画するのではなく、FIFO 原則 (キューの最初のオーダーの一部が残され、他のオーダーはキューの最後に到着する、オーダーのライブ バッファ) に基づく「無限」のローリング生産計画で、生産に投入できるオーダーを維持するのが理にかなっています。このオーダー バッファは、インターオペレーション ストックです。現在のバッファ ボリュームをラインのボトルネックの上限パフォーマンス制御限界よりも低く維持し、ボトルネックがランダムな時間にダウンタイムなしで動作して最大のパフォーマンスを達成できるようにします。生産用のオーダーを準備するプロセスがボトルネックでない場合は、数サイクル後にはボトルネックの前にこのようなバッファ ストックが自然に形成されるため、追加の作業は必要ありません。
管理図を使用すると、生産チェーン内のプロセスの統計的制御可能性の状態や、レポート期間が終了するずっと前にプロセスのパフォーマンスの良くも悪くも変化を監視できます。生産ラインの工程が安定している間は、製品の種類ごとにボトルネック(工程)の平均的な生産性をもとに、ライン(一連の一連の工程)の生産性を計画します。
1980 年代に開発されたゴールドラットの制約理論 (TOC) との類似点はありますか?シューハート管理図はずっと以前に開発され、TOC とは異なり、予測可能または予測不可能なプロセス動作を考慮しており、判断ではなく基礎科学に基づいています。
以下は、ボトルネックのないバランスのとれたラインのパフォーマンスの例です。バランスの取れたラインの最終パフォーマンスは、常にそのようなラインのプロセスの平均をわずかに下回ります。
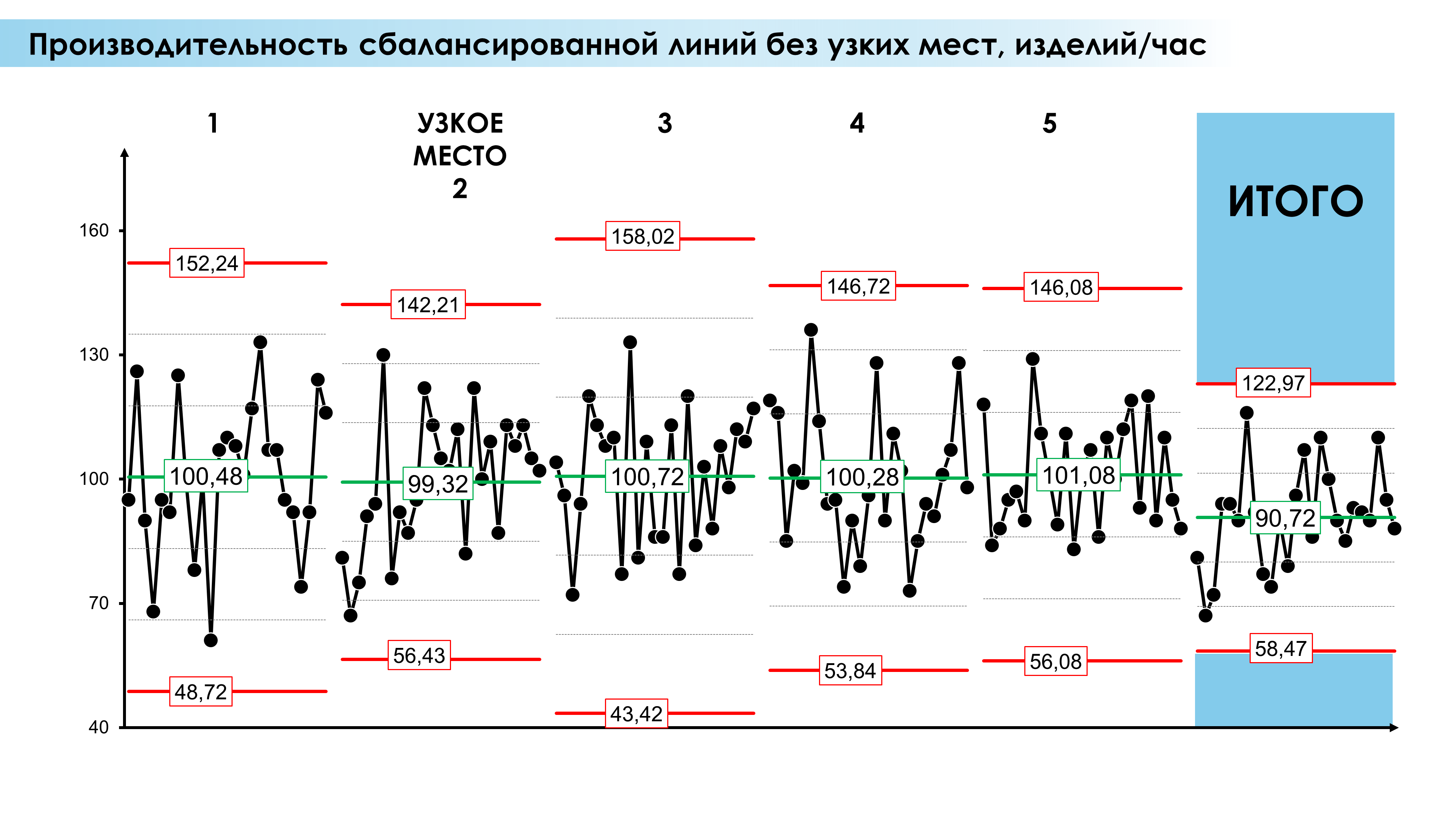
図 16. シューハート管理図を使用して実証された、ボトルネックのないバランスのとれた生産ラインの最終パフォーマンス。シミュレーション方法に関する分析方法は、Donald Wheeler と David Chambers の著書から借用しています。 「統計的プロセス管理: シューハート管理図を使用したビジネスの最適化」、366 ~ 370 ページ [4]。図面は当社が開発したソフトウェアを使用して作成されました 「シューハート管理図 PRO-Analyst +AI(Windows、Mac、Linux用)」 。
バランスのとれた生産ラインの工程前の工程間在庫は、工程停止を防ぐために必要なレベルに維持する必要があります。バランスのとれた生産ラインで工程を停止する場合など、工程間在庫が維持される工程の上限管理限界を超えて蓄積しても意味がありません。すべての工程が安定して継続的に稼働している場合、ほとんどの場合、自然に発生する少量の工程間在庫で、ライン全体の継続的な稼働に十分です (下の図を参照)。
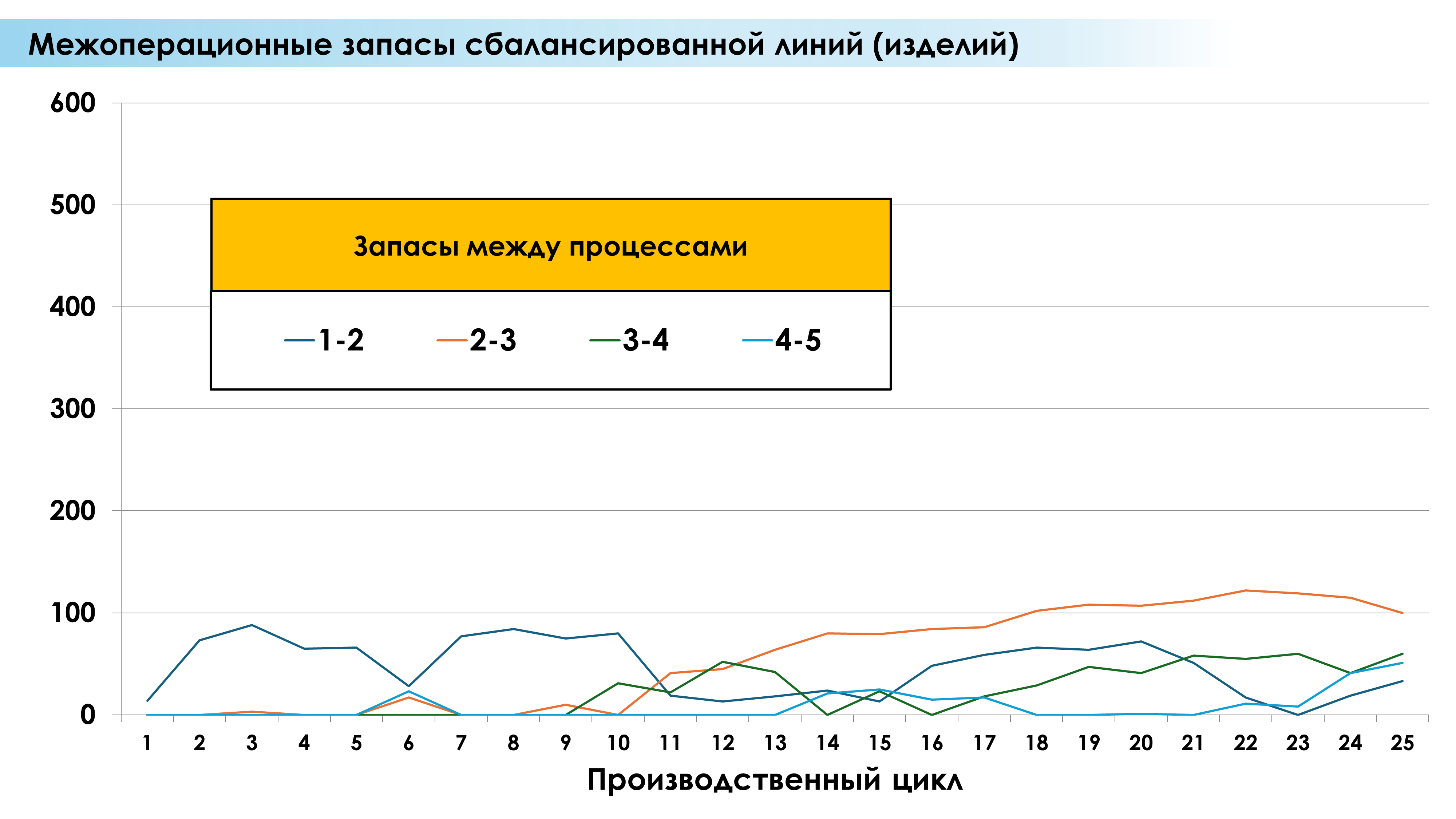
図 17. ボトルネックのないバランスのとれた生産ラインにおける相互運用可能な在庫蓄積スケジュール。
すべてのプロセスインプットの変動を削減し(原材料、設備、操作の安定性を高めるなど)、イノベーションを導入することにより、すべてのプロセスを継続的に改善します。石川特性要因図、管理シート、パレート図、個別値の密度ヒストグラム、散布図、シューハート管理図は、これに最適なツールです。さらに、シューハート管理図は最も重要なツールです。これらすべてが、より正確な計画の可能性につながります。これは生涯にわたる仕事であり、システム全体を最適化するという目標によく適合します。

図 18. 特性要因図。石川図。魚の骨格。
プロセスは改善されましたか、それとも悪化しましたか (ボトルネック)?管理図には、平均値の変化と平均値付近のデータの範囲が表示されます (範囲管理図から簡単にわかります)。プロセスにおける持続可能な変化の最初の兆候は、システムの変化を示す信号になります。変更された状態の 8 つの新しい点を追加することにより、プロセスの新しい状態の統計的安定性を追跡するための新しい管理限界を構築できます。
シューハート管理図を使用して、プロセス (システム) のポジティブな変化とネガティブな変化を迅速に診断する方法に関する映画をご覧ください。
ビデオ 1. プロセス (システム) の変化を迅速に診断する方法。
注文準備日 (計画) の予備計算には、合理的な程度の統計的制御可能性 (予測可能性) を示すプロセス指標のみを使用できます。たとえば、アンバランス ラインの連続生産では次のようになります。
- 「ボトルネック」にある各製品の平均絶対準備時間 (圧倒的多数の場合、準備時間はバッチ サイズに依存しないため、絶対値)。
- 「ボトルネック」にある各製品の単位時間当たりの平均生産性。
- 計画外のボトルネックダウンタイムの平均。
技術チェーンの「ボトルネック」の特定の製品に対応する 1 日の合計時間から、計画されているすべての機器のダウンタイム (メンテナンス、修理、非稼働時間など) が差し引かれます。
原因の種類と過去の時間別の計画外ダウンタイムの管理図は 2 つの目的に役立ちます。1 つはその数と期間を削減するための作業であり、もう 1 つは計画外ダウンタイムに関して合理的な程度の統計的制御可能性を示しているプロセス (ボトルネック装置) についてです。計画ではそれらを考慮し、前のステップで残っている作業時間からそのようなダウンタイムの平均時間を差し引きます。
残りの作業時間については、製品の種類ごとの注文、平均準備時間、平均生産性を考慮して注文を配分します。統計的に制御できない状態にあるプロセスは、定義上、予測不可能です。それらの平均は計画 (予測) に使用するには不合理です。計画システムを改善するには、そのようなプロセスを統計的に安定した (制御可能な) 状態にしてから、そのようなプロセスの変動を減らすことに取り組む必要があります。
重要
製品を生産するのは計画された数値(ノルム)ではなく、この計画された目標を気にしないプロセスであることを理解することが重要です。データを収集して分析し、ショップレベル(現場)で人々やプロセスを扱う場合、私たちはプロセスとその中の人々について多くのことを知っています。私たちは生産性を向上させたいと考えています。問題を理解して「出力」を監視し、数値的に測定可能な指標にシューハート管理図を使用することで、プロセスへの「入力」とプロセス自体を改善し、目標に従ってシステム全体を最適化します。 。

図 19. 機能モデリング方法論 IDEF0 [16] 。