お金はあるけど知識はいらない?支配的な経営スタイルの常套手段は、お金があるうちはお金がなく、知識は役に立たないというものです。
資料作成者: AQT センター科学ディレクター セルゲイ・P・グリゴリエフ
記事への自由なアクセスは、記事に含まれる資料の価値を決して減じるものではありません。
前文
以下に示す資料には (明らかな理由により) 数値が含まれていませんが、提示された特定の欠点に関しては、一見すると成功している企業の多くに起因すると考えられます。
会社「N」は非常に成功した企業とみなされています。 1 日に 1 ~ 3 回、遠足の代表団が常に訪れています。
「典型的な状況は、企業の経営者が品質や生産性の向上に熱心だが、どうすればよいのか全く分からない。啓発を求めて、一見繁栄しているように見える他社を訪問することである。そこで、こうした経営者は、彼ら(訪問者)は会社の運営方法を学びますが、その一部がガイドラインを使用しなければ、どちらの会社も正しい手順とは一致しません。 「問題は、なぜそれが成功するのか、そしてさらに成功させることができるのかということです。訪問者がツアーを楽しんでくれることを祈るばかりです。それは彼らのせいではなく、彼らの問題なのです。」
生産設備から従業員用トイレの安全メガネの棚に至るまで、これほど目立つ順序を私はどの企業でも見たことがないことに注意してください。後でわかったことですが、これは欲望と資金だけでできる唯一のことでした。
私の訪問の初日は、社内のすべての部門の責任者が集まる毎週の会議に出席することから始まりました。レポートから、マネージャーが会社の活動全体を最適化するために協力していないことは明らかであり、全員が自分の部門の目標 (KPI) に忙しく、実際には部分的な最適化であり、それは全体的な目標に害をもたらすだけです。会社。
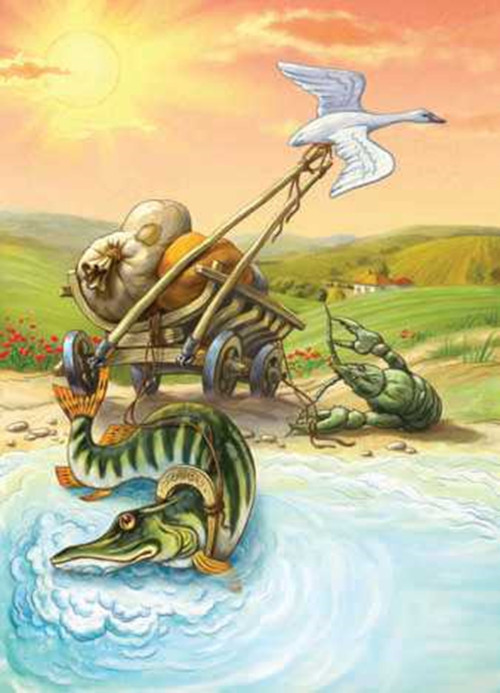
「同志間に合意がなければ、仕事はうまくいかず、そこからは何も生まれず、ただ苦しむだけだ。ある日、スワン、キャンサー、パイクはたくさんの荷物を運び、三人で力を合わせて荷物を運びました。彼らは皮から這い出ましたが、荷車はまだ動きません。彼らにとって荷物は軽いように見えるでしょう。そうです、白鳥は雲に突入し、蟹座は後退し、パイクは水に引き込まれます。誰が悪いのか、誰が正しいのかを判断するのは私たちではありません。
会議では、講演者らは計画を報告期間の事実と比較し、また前報告期間との関係を数字付きの表の形で比較した。一部の場合は、対応する列を含むグラフで数値が補足されました。まれに、その事実が計画された指標に達し、発言者を不必要に当惑させた。それは明らかでした 変動性の性質 そして、パフォーマンス指標を分析し、将来の行動を予測するための統計的手法の使用については、企業内の誰も知りません。
生産と品質管理
生産時の品質を「許容範囲内/許容範囲外」で管理するために、プラグやステープルなどのゲージが使用されます。旋削加工の場合、これはごく普通のことです。しかし、このように製品を良品と不良品に分けると、部品製造プロセスの継続的かつ効果的な改善に必要な個別データの背後に隠された最も重要な情報が労働者や会社経営者から奪われてしまいます。
ところで、白黒テレビはかつてかなりの需要がありました。

図 1. 品質管理でゲージを使用するときに得られる情報。図中のパーセンテージはこの会社とは関係ありませんが、わかりやすくするために示されています。
研究に統計手法 (シューハート管理図) を使用していないことは、社内で入手可能な離散データであっても、生産プロセスの継続的改善という目標を追求する組織的な活動が社内に存在していないことを示しています。
もちろん、同社は不良部品の割合に関する統計を保持し、誰もが見られるようにグラフを表示しますが、このデータを次にどうすればよいのかは誰にもわかりません。
同社の経営陣にとって特別な誇りの源は、インストラム・ランド社から軽率に模倣された「ダイヤモンド」システムです。その簡単な本質は、労働者が生産した欠陥製品を「自発的に」放棄することです。許容限界に関して。従業員が欠陥製品を自発的に引き渡した場合、罰せられることはありませんが、引き渡しを怠った場合には罰金が科せられます。
「懲罰」という言葉は、この会社の「ダイヤモンド」システムに関するデモンストレーション資料から引用されたものであり、私の意見では、会社の現在の従業員に対する軽蔑的に聞こえます。不当な「処罰」の可能性は状況を悪化させるだけです(これについては下記で詳しく説明します)。
「外的動機は、「欠陥ゼロ」を求める人々の考え方です。人は自分が持っているものを守るために戦い始めます。彼は罰を避けようとしている。しかし、これらはすべて屈辱的であり、人格の低下につながります。それは日雇い労働の日給にすぎません。しかし、一定の水準を超える給与はモチベーションにつながりません。給料は確かに内発的動機をもたらしませんし、多くの人が考えがちなほど強力な外発的動機ではありません。私たちは個人に立ち返って、その人がありのままであることに満足を与えなければなりません。そうです。」
「Brilliant」システムの作者であり、Instrum-Rand 社のゼネラルディレクターであるヴァディム・ソローキン (1993 年) は、現在 GAZ グループの社長兼ゼネラルディレクターを務めていますが、ここでは「Brilliant」システムは導入されていないことに注意することが重要です。ブリリアント社は、欠陥部品の納入を怠った場合に罰金を科すことを今も続けています。しかし、ロシア企業の経営者は、提出を怠った場合に強制的な罰金なしにこの制度を受け入れることはできない。彼らのパラダイムは、悪質な管理スタイルを監視しています。そうでなければ、経営陣は仕事を続けなければならなくなるでしょう。
「コピーにはリスクが伴います。すでに理論に精通している場合は、何かに挑戦する必要があります。アメリカ人は優れた模倣者です(たとえば、品質サークル、カンバン、ジャストインタイムなど)。しかし、日本人は理論を最初に学び、その後で始めますアメリカの経営陣は、「品質サークル」の仕事における役割を理解せず、それを真似しようとしますが、しばらくすると、経営陣と協力し対話する「品質サークル」はどこでもうまく機能することが判明します。
オリジナルの「Diamond」システムにも、次のような重大な欠点があります。
- 許容範囲は、プロセスに関連するアクションの境界として使用され、コミットによるビジネス損失を最大化します。 第一種および第二種のエラー ;
- 各オペレーターとコントローラーの測定システムの安定性、偏り、誤差のチェックについては一言も触れられていません。
- 欠陥部品を生み出す生産プロセスの安定性をチェックすることについては一言も触れられていない。
- 協力的な環境で作業するオペレーターが無料で提供しないのと同じように、特定された欠陥製品の提供に対して支払いが行われます。
「何かをしてもらうために人々にお金を払えば払うほど、人々の関心は、しなければならない活動から報酬へと移っていきます。」
次に、企業に関係するすべての関係者は、許容範囲内で欠陥がある納品された製品を処理して、欠陥の原因を特定し始めます。 「ダイヤモンド」システムの作成者、この会社の経営者、および欠陥製品の分析に携わった人々は、許容限界に対して欠陥のある製品と欠陥のない製品が、安定したプロセスの自然な成果物である可能性があるという事実を見失っています。つまり、完全に均質であること - 1 つのシステムによって生成され、その責任は労働者ではなく企業の経営者にあります。この場合、同じ「成功」があれば、このプロセスで製造された欠陥のない製品を研究することが可能になります。
「同じでない 2 つの数字は異なるものとみなされます。残念ながら、これは算術では当てはまりますが、データの解釈では当てはまりません。この世界では、2 つの異なる数字が同じものを表すこともあります。」
許容限界に比べて欠陥のある製品を生産するプロセスが統計的に制御できない状態にある場合、そのようなアクションはプロセスの出力に何らかのプラスの影響を与える可能性がありますが、効果 (労力/結果) は常に大幅に低くなります。制御不能の特別な原因が欠落していること。シューハート管理図によって許容範囲内にある点で検出できる可能性があり、これにより次のような問題が発生します。 観察者の「夜盲症」 - プロセスを改善するための追加の機会を利用しない。
許容範囲の制限を使用してプロセスの参加者に対して措置を講じるのは無知です。プロセスが統計的に管理された状態にある場合、このような対策は安定したシステムの稼働を妨げ、悪化を招くだけです。この現象の説明については、エドワーズ・デミングの実験を参照してください。 「ファネルとターゲット」 ドナルド・ウィーラーによる記事 「公差フィールドの正しい使用方法と誤った使用方法」 。
説明。許容限界は消費者の要件 (外部および内部) であり、多くの場合、プロセスの能力とは関係ありません。シューハート管理図上のプロセス境界は、プロセスの実際の能力です。もちろん、プロセスの能力がその要件を満たしているか、さらにはそれを超えていることが望ましいです。ただし、要件への準拠は、次の 2 つの方法またはそれらの組み合わせで達成できます。 1. プロセス能力を向上させる。 2. プロセスの要件 (許容範囲) を変更します。たとえば、許容範囲を拡大するために消費者と合意します。
ビデオ 1. プロセスを改善するには何をする必要がありますか?
ビデオ内の要素の記号: НГД と ВГД - それぞれ許容差の下限と上限 (Eng、LSL、USL)。 m0 - 公称公差フィールド。 НГП および ВГП - プロセスの下限および上限の自然な境界 (英語の LNPL および UNPL)。 CL - プロセスの中心線 (プロセスの平均)。
同時に、プロセスが許容範囲を超えて動作する場合は、消費者に出荷する前に製品を不良品と良品に分類して 100% 管理する必要があり、その結果、ドナルド・ウィーラー氏の記事で説明されている結果が生じます。 : 「仕様上の製品は実際に準拠していますか?」
不良品を生産するプロセスの統計的に安定した(安定した)状態は、そのプロセスが稼働するシステム内で最善のパフォーマンスを発揮できることを示していることに注意してください。この場合、状況を大きく変える可能性があるのは、労働者ではなく会社の経営者が責任を負うシステム的な変更のみである。
「組織におけるすべての問題(または改善の機会)のうち、変動の特別な原因に関連するものはわずか 6% です。したがって、それらは一般の従業員の活動分野にある可能性があります(ただし、必ずではありません!)。この場合、トップマネージャーは、従業員が働くシステムの潜在的な改善の少なくとも 94 % を占めています。
いかなる管理も、労働者のいかなるレベルの専門的スキルも、システムの根本的な欠陥を克服することはできないだろう。」
逆に、統計的に不安定な (不安定な) 状態にあるプロセスは、工場レベルで特定して排除する必要がある特別な理由の影響下で最大のコストで動作します。プロセスの安定した状態と不安定な状態を区別する兆候 (規則) を理解することが重要であり、これらは許容限界ではありません。記事内の説明を参照してください。 変動の性質 。
「統計的管理は、それぞれの特定の原因を追跡し、点が管理限界を超えるたびにそれを特定し、適切な措置を講じることによって達成できます。」
管理対象として選択されたすべての製品(良品および不良品)の管理測定の値を連続値の形式で記録しないことで、プロセスの統計状態に関する情報や、公称値および許容限界に関するデータ分布の統計が隠されます。このような記録は、このデータが埋め込まれている欠陥レポート内の不良品に対してのみ保存されます。
製品の一般的な流れから選択されたすべての測定値を記録し、機械オペレーターが直接シューハート管理チャートを維持することで、次のことが可能になります。
- 検査対象に選択された部品がオペレーターによって測定されるとすぐに、観察された変動を引き起こす原因の種類 (一般的なシステムまたは特殊な理由) を特定します。
- 証拠に基づいた方法を採用し、違反行為のリスクを最小限に抑えながらオペレーターを支援する 第一種および第二種のエラー 。
たとえば、品質指標が合理的な程度の統計的制御を示しており、分布ヒストグラムが許容範囲フィールドに対して右または左にシフトしている場合、そのようなシフトの理由として次のことが考えられます。測定システムのバイアス。オペレータによる機械の設定、または機械の技術的条件。この場合、結婚の理由について労働者に尋問するのではなく、調査の対象がある。企業の品質管理方法を変更する決定を下すのは経営者の責任です。
以下のスライドの 2 つの部分は、同じ割合の不良品を示しています (グラフ提供: Donald Wheeler)。改善に役立つ情報はどこにありますか?

図 2. 生産における品質管理においてゲージ (左側の白黒図) と統計的手法 (右側のカラー図) を使用することで得られる情報。
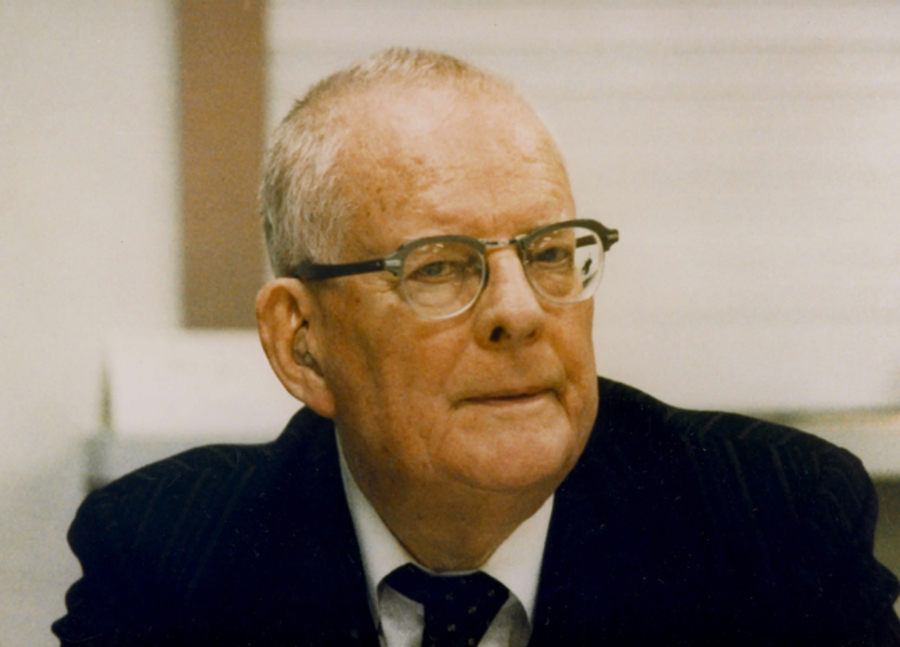
「知識に代わるものはありません。しかし、知識を活用するのは恐ろしいことです。」
同社の計量サービスでは、測定器の使用方法を従業員に訓練するための優れたスタンドを設置し、設備を整えています。研修のために別の従業員がいます。しかし、得られた測定値を正しく記録する方法を誰も学生に教えていないという事実には誰も興味がありません。品質レポートの一部の演算子は、測定結果を記録するときに、数値の整数部分と小数部分を「-」記号で区切ります。したがって、「-」サインイン レポートは、生産現場のコントローラーから部門までのすべての段階を通過し、すべてのデータがコンピューター上の単一のデータベースに入力されます。レポート内のこれらのエントリを見る人は誰もこれに注意を払いません。
この企業のすべての設備には、「3 つの NOT」(「欠陥を受け入れない」-「欠陥を作らない」-「欠陥を転嫁しない」)をスローガンにした標識が設置されています。これらのスローガンは今日ロシアの産業界で非常に人気があり、いたるところに掲示されています。あたかも、従業員が望めば、企業経営者が設計したプロセスの結果である欠陥を排除できるかのように。
「スローガンやポスターの宛先が間違っている!」
この簡単な考察から少し脱線して、話をします。
私が率いていたある製造工場では、完成品の新たな欠陥、つまり構造の 2 つの部品の溶接接合部に目に見える段差が発見されるという状況に直面しました。これは完成品の外観と強度特性に大きな影響を与えました。製品。
私たちは企業の経営陣と協力して、設計部門に至るまでの生産業務の「上流」チェーン全体を追跡しました。結局のところ、勤勉な労働者が対処できない問題は「まったく価値がない」ということがわかりました。事実は、CADで作業している設計者が、おそらく「より強くなる」と信じて、溶接があってはいけないゾーンに入る溶接の位置をマークしたということです。設計者は、設計中にミスを犯したことさえ知りませんでした。次に、作業環境において非公式の高い権限を持つ最高クラスの専門家である溶接工が責任を持って仕事を行い、部品を抵抗スポット溶接ステーションに移送し、そこで製品の 2 つの部品が接続されました。
溶接工が行った作業は定義上欠陥ではなく、技術仕様に従って行われたことを強調したいと思います。前回の作業で行われた溶接により、スポット溶接部位に許容できない隙間が生じました。抵抗溶接工も責任を持って仕事をしましたが、抵抗溶接の接続は信頼性が低く、2 つの部品の接合部に目立った段差が生じていました。ここで、抵抗溶接工は接合部の段差の高さを疑問に思ったかもしれませんが、観察された欠陥の操作上の定義を与える人は誰もいませんでした。そのような定義は単に存在せず、彼は自分が最善を尽くしていることを知っていました。より有資格で権限のある作業員が以前の作業に取り組んでいました。次に、構造は研削および研磨ステーションに移送され、そこで勤勉な作業員が部品が接合されている場所を「ゼロにする」(洗浄および研磨)必要がありました。前回の作業中に発生した段差は、この作業員に多大な困難を引き起こしましたが、観察された欠陥の運用上の定義を彼に与える人は誰もいませんでした。
作業員が剥離作業中に抱いていた疑問は、以前の作業がより経験豊富な作業員によって行われたことを理解したときに消えました。彼は剥離作業により多くの時間を必要とし、接合線を完全に隠すことは不可能でしたが、彼の仕事は段差をゼロにすることであり、以前の作業で発生した理由を理解することではありませんでした。 「ノー」とは何かという具体的な定義を彼に与えた人は誰もいませんでした。つまり、この組み立て単位は最終的に完成品の組み立てになりました。
私たちは、上記の一連の生産作業の参加者全員をワークショップに集め、完成品を組み立てるまでの後続の各作業で彼らの作業がどのような困難を引き起こすかを実証しました。実際のところ、彼らは皆、自分の仕事に責任を持って取り組んでおり、次の作業で製品に新たな問題が発生していることを単に知らなかっただけです。以前の工場で作業員に近づき、彼が直面している問題について話すなどということは誰も思いつきませんでした。当然のことながら、この欠陥は再び発生しませんでした。経営陣は自分たちのことだけを考えるべきだった。
ここに「3 つの NOT」と書かれたポスターが貼ってあると役に立つでしょうか?!そして、この場合も他の場合も、企業経営者が設計したシステムで働く従業員に向けて、品質の向上と生産性の向上を求めるポスターは役に立たず、正当な憤りを引き起こすことになります。品質を向上させ、生産性を向上させ、会社全体の目標に基づいてすべての部門の活動を最適化するために経営者が何を行っているかを説明するポスターを掲示することをお勧めします。
すべてがどのように終わるかを見てください E. デミングの赤いビーズの実験 その中で主人は、金銭的な報酬、脅し、説得、スローガンを用いて、労働者に欠陥なく働き、職務に対して責任ある態度をとるように動機づけようと試みます。
「組織におけるすべての問題(または改善の機会)のうち、変動の特別な原因に関連するものはわずか 6% です。したがって、それらは一般の従業員の活動分野にある可能性があります(ただし、必ずではありません!)。この場合、トップマネージャーは、従業員が働くシステムの潜在的な改善の少なくとも 94 % を占めています。
いかなる制御も、労働者の専門的スキルのレベルも、システムの根本的な欠陥を克服することはできません。」
さらに特急審査の結果を踏まえて
企業の従業員と訪問者の安全に対する外部への懸念(安全メガネ、ヘルメット) - 本当に危険な場所を除くあらゆる場所で。プロセス最適化部門が入るオフィスビルへの中庭からの入り口前では、屋上から重さ3kgにもなるつららが定期的に飛来します。危険区域を柵で囲ったり、危険を警告したりする兆候さえありません。営業日の朝にこのリスクについて部門長にコメントした後、その日が終わるまで何も変わりませんでした。
製造された欠陥製品に関する書面による報告書の中で、作業員は欠陥の原因が眠れぬ夜の疲労によるものであると説明しています。疲れた旋盤オペレーターに製品の欠陥が起こるなんて、そんなことは誰も気にしませんでした。
調査結果は、未使用埋蔵量に関する報告書の形で企業のトップにプレゼンテーションで提示され、企業の継続的な改善と競争力の向上を目的とした対策案の提案に伴う問題点が特定されます。どうやらこの報告については社長以外誰も知らなかったらしい。