CAD で設計するとき、額面通りに構築されたデジタル モデルをテストすることに依存していますか?その後、コンポーネントの組み立てや実際の状態での完成品の動作に問題が発生することが予想されます。
資料作成者: AQT センター科学ディレクター セルゲイ・P・グリゴリエフ
記事への自由なアクセスは、記事に含まれる資料の価値を決して減じるものではありません。
生産プロセスの変動を分析すると、悪影響を軽減できます。 避けられない変化 製品の寸法品質、コスト、市場投入までの時間など。
以下は、デジタル モデルが果たすべき目標を考慮せずに、デジタル モデル自体で広範な部分最適化が行われている証拠です。
私たちのチームは、ロシアの研究生産会社での会議で、製品の設計と生産における主要な品質指標の変動性という観点から、実際の生産プロセスの能力を理解する必要性についての報告書を発表しました。
レポートのセクションの 1 つは、当社とサプライヤーの両方の実際の生産プロセスの統計的状態と能力を理解せずに、設計された製品の品質に関する問題に特化していました。特に、この企業の 1 つの企業の副総設計者 (ZGK) は、新しいデータセンター (データ保管および処理センター) の建設により、本格的なテストが削減されると報告しました。
ZGK ステートメントに対する当社の態度: 実際のプロセスの可能性を知らない限り、そのようなステートメントには注意することをお勧めします。実物大の試作品(プロトタイプ)であっても、連続製品ではありません。
「プロトタイプのテストが不十分。
プロトタイプは単一であり、そのパラメータは人為的に公称値に近いものになっています。変動に関する知識がなければ、変動を予測することはできません。」
フルスケール テストをデジタル モデル テストに置き換えることを考えるときは、何をどの程度無視してもよいかを理解する必要があります。簡単に言うと、デジタル モデルのテスト結果が実験モデルの本格的なテストとどのように異なるか、さらにはシリアル製品とはさらに異なることを理解する必要があります。無視しても構わない要因の影響が重要ではないと仮定すると、これらの要因の結果および説明されていない (無視され、未分化、および/または数値的に測定不可能な) 要因は、その固有の変動性を考慮すると、テストの目的の観点から、想定を超えています。これは真実ではないと思いますか?どうやってこれを知っていますか?そのような結論を下すにはどのようなデータが必要ですか?
世界的に有名な例を挙げましょう。
第二次世界大戦中、アメリカとイギリスの空軍司令部は、アメリカの統計研究グループ (SRG) の秘密プログラムで働いていたエイブラハム ウォルドに、航空機の胴体のどの部分を追加の保護手段で保護する必要があるかを調査するよう命じました。鎧。軍は、空戦中に最も被害を受ける航空機の部分に追加の保護装置を設置することを提案しました。ヴァルドは戦闘任務から帰還した飛行機を研究し、命中弾の位置を記録した。その結果、彼は逆に穴の数が最小限だった領域(胴体の中央部と後部)に追加の保護装置を設置することを推奨しました。この勧告は、ワルドが見ていなかった攻撃、つまり攻撃を受けた飛行機が単純に戻ってこなかった攻撃から保護する必要があるという結論に基づいていた。その後、既知のデータのみの分析に基づいて下される決定は「生存者バイアス」と呼ばれるようになりました。
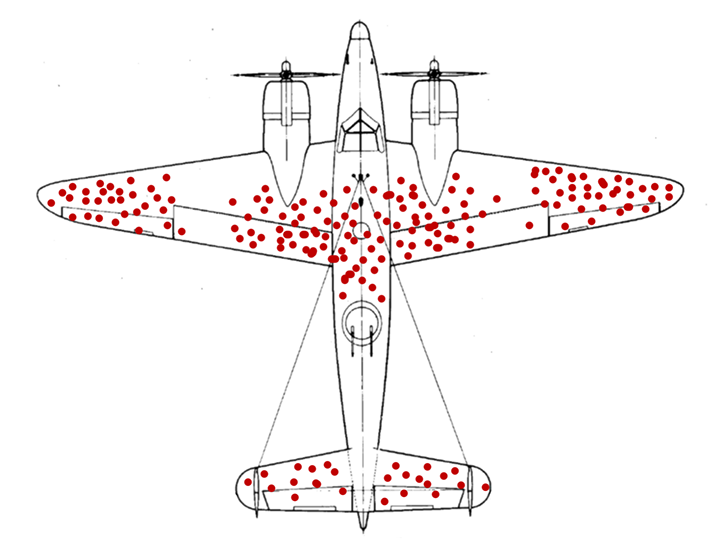
図 1. エイブラハム・ウォルド氏。生存者バイアス。帰還したアメリカ軍機の弾痕の統計を表す赤い点のある飛行機。
その後、デジタル モデルの結果を実際のプロトタイプのテストと比較する予定の場合、いくつのプロトタイプを作成してテストする予定ですか。 1; 5; 8; 25?これらのプロトタイプは同じものになるでしょうか?どうやってこれを知っていますか?プロトタイプの均一性を主張するには、自社の製造プロセスおよびプロトタイプの製造に関与するサプライヤーの製造プロセスの統計的制御可能性の証拠が必要です。すべての重要なパラメーターについて、これらのプロセスのシューハートの管理図をデモンストレーションできますか?
私たちの声明の説明
コンピュータ支援設計システム (CAD) での設計は、名目上のデジタル モデルで実行されますが、ハードウェアで行われるものではありません。設計者は、実際の製造プロセスに固有の変動性に関するデータを使用して、必要に応じて設計、材料、技術、公差の変更を決定したり、実際のプロトタイプの製造を開始する前に製造部門やサプライヤーにプロセスや技術の改善を要求したりする必要があります。
私たちは、この企業の主要な製造会社の企業公開情報を注意深く調査しました。この出版物では、同社の従業員が生産中に遭遇した問題について十分に詳細に報告しています。
特に、組立工場のプロセスエンジニアは次のように報告しました。
「技術者は組み立てプロセス中に発生する問題に対する最適な解決策を探す必要があるため、現在の状況に迅速に対応する必要があります。いくつかの緊急事態が発生する可能性があることを考慮すると、彼は急いですべてに対応しなければなりません。これは組立工場のプロセス エンジニアの通常の作業ペースです。」
この技術者は、製品の組み立て中に緊急事態が頻繁に発生することに慣れており、彼自身もこれが正常であると認識しています。したがって、組み立て中に問題が持続すること(安定性)が確認されます。そして、安定性はシステム的な問題の兆候です。システム的な問題に対処するのは技術者ではなく管理者の責任です。
鍛冶屋は次のように言いました。
「鍛冶屋は、鍛冶場でワークピースを加熱するとき、その温度を視覚的に判断し、金属が鍛造の準備ができているかを感じます。加熱すると炭素やその他の合金元素が燃え尽きるため、過熱しないことが重要です。たとえば、初心者は 4 回の加熱で金属から目的の形状を達成します。経験豊富な鍛冶屋にはたった 2 つしか必要ありません。」
設計者はこの製造プロセスの不確実性を考慮に入れましたか?さまざまな鍛冶屋がさまざまな条件下で「目で見て」決めた温度まで無制限に加熱すると、どのような合金が得られるか知っている人はいますか?この場合、デジタル モデルの強度の自動計算は、実際の製品の機械的特性や耐食性などの予測に役立つでしょうか?!
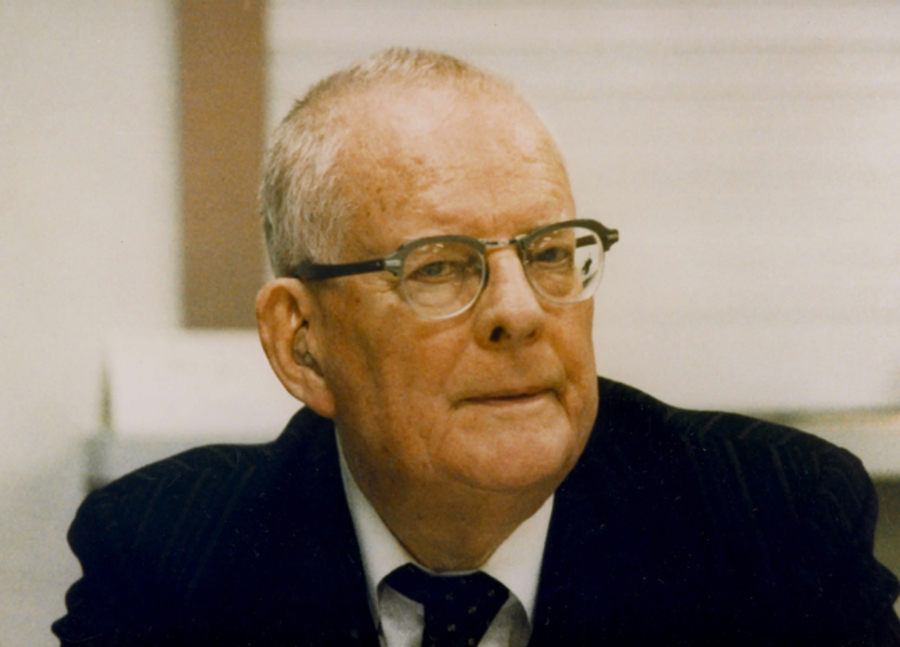
「実践は純粋な科学よりも正確であり、トレーニングよりも正確です。シューハート氏によると、製造業やサービス業で必要とされる知識とスキルの基準は、純粋な科学の基準よりも厳しいです。」
上のエドワーズ・デミングの引用は、ロシアの産業が多くの分野で負けている一方で、ロシアの科学が国際レベルでの競争に自信を持って耐えているという現状を部分的に説明している。
企業経営者が品質に対する責任を理解していないことを示す他の例も挙げましたが、この記事では公開しませんでした。
公称公差の部品と、設計時に定められた要件を満たした合金から構築されたデジタル モデルが、実際のプロトタイプとどのように異なるのかが、より明確になってきたことを願っています。シリアル製品について話している場合、これらの違いはさらに大きくなります。設計、生産、供給、サプライヤーとの協力に関わる部門間に障壁が存在することを考えると、数百、さらには数千の部品を備えた製品の本格的なテストを拒否すると、巨額の損失が発生することになりますが、その本当の理由は決して認識されません。この法人の経営。
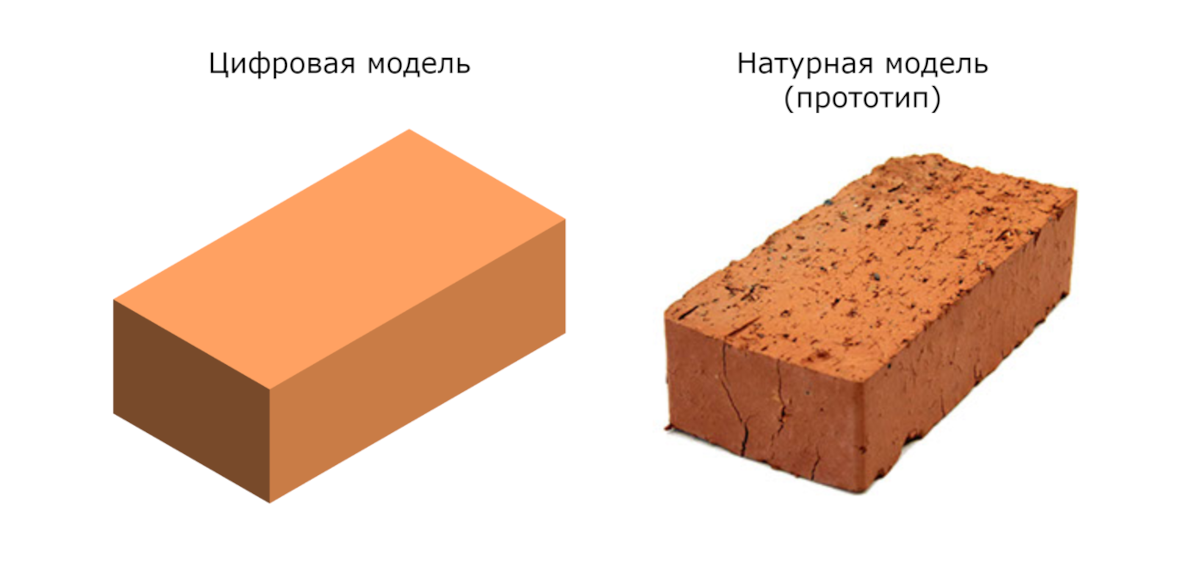
図 2. デジタル モデルと自然モデル
次に、会議の出席者に、すきまばめのシャフトと穴の公差フィールドの最も単純な 2 次元の組み合わせのオプションを検討するよう依頼しました。実際の部品の幾何学的寸法のばらつきは、デジタル モデルと実物大のモデルを区別する最小のものです。
以下は、シャフトと穴の公差フィールドのペアの条件付き表示です。設計者はCADで部品を同等に作成します。最良の場合(最も先進的なロシア企業の場合)、デジタルモデルは、相互作用する部品の公差フィールドの組み合わせと、相互作用の結果として得られる従属公差フィールドへの適合性がチェックされます。
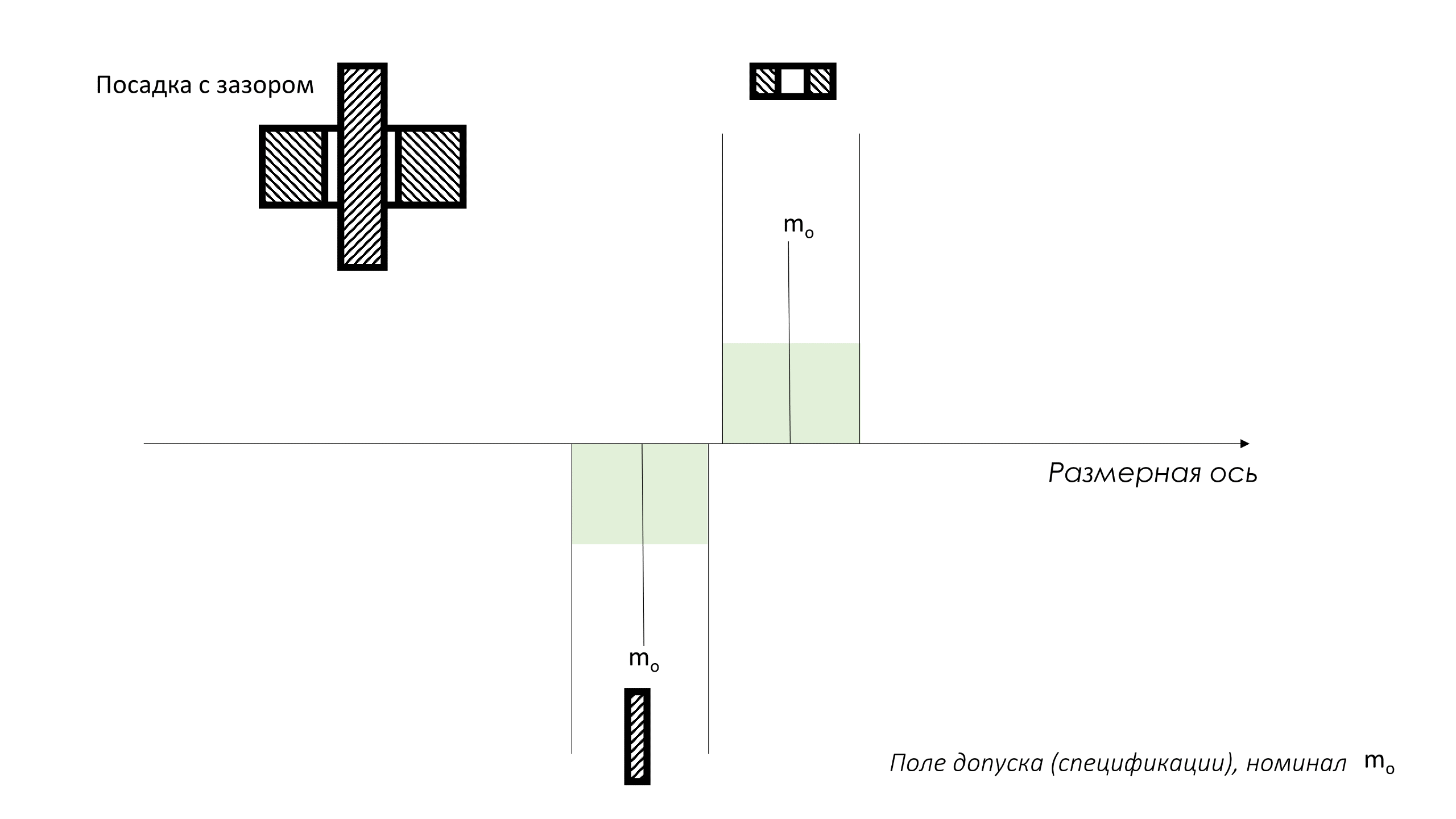
図 3. シャフトと穴の公差フィールドの組み合わせの条件付き表示 (すきまばめ)。
この場合、部品を製造する理想的な製造プロセスは、以下の図 4 に示すように、個々の測定値の分布密度に対応する必要があります (対称の釣鐘型曲線は任意に選択されます)。安定しており、完全に中心にあり、分布は次のとおりです。個々の値はある程度の空き領域のある許容範囲内にあります。この場合、すべての部品が 100% 適切であることが事前にわかっています。プロセスの安定状態を確認し、そのようなプロセスの分布の平均(中心線)を公称公差領域に合わせて調整するために、制御用の部品のまれなサンプリングを実行するだけで十分です。
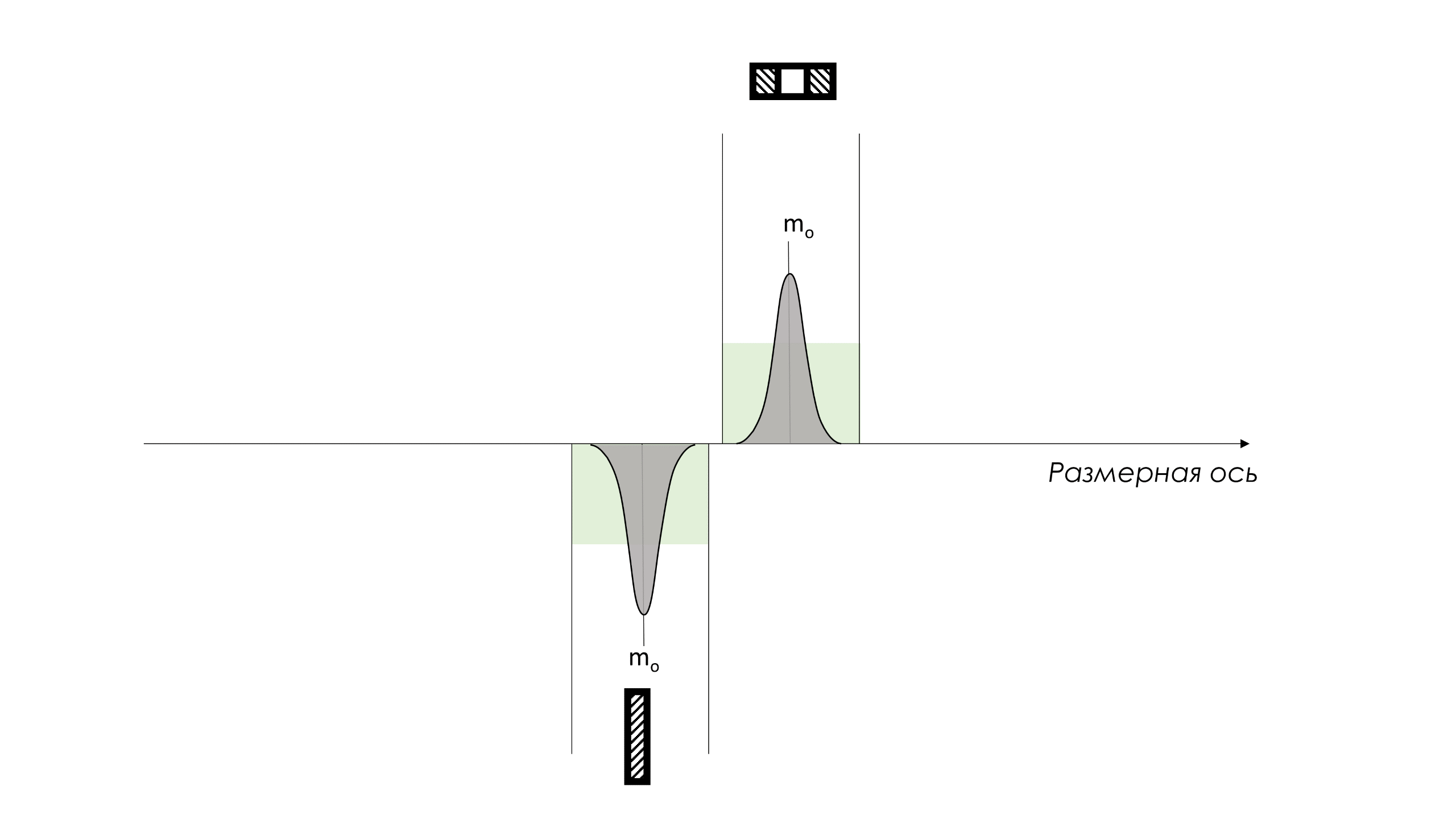
図 4. 安定した完全に中心にある生産プロセス。個々の値はある程度の空き領域のある許容範囲内に分散されています。
ここで、以下の図のオプションを考えてみましょう。生産プロセスが統計的に制御された (安定した) 状態にあり、その広がり 6σ は許容範囲の幅 (たとえば、Cp≥1.33) よりも小さいですが、中央にありません。そうなると、製品によっては許容範囲を超えて不良品になってしまうこともあります。額面どおりの詳細は何一つありません。製造されたすべての部品を公差範囲に適合する部品とそうでない部品に分けて 100% 管理する必要がありますが、コストがかかり非効率的です。この場合、部品のほぼ半数が公差範囲を満たさないことが事前にわかっています。式の説明を参照 再現性指標 Cp および Cpk の計算 。
再現性指数の計算式:Cp = 許容範囲 / 6σ
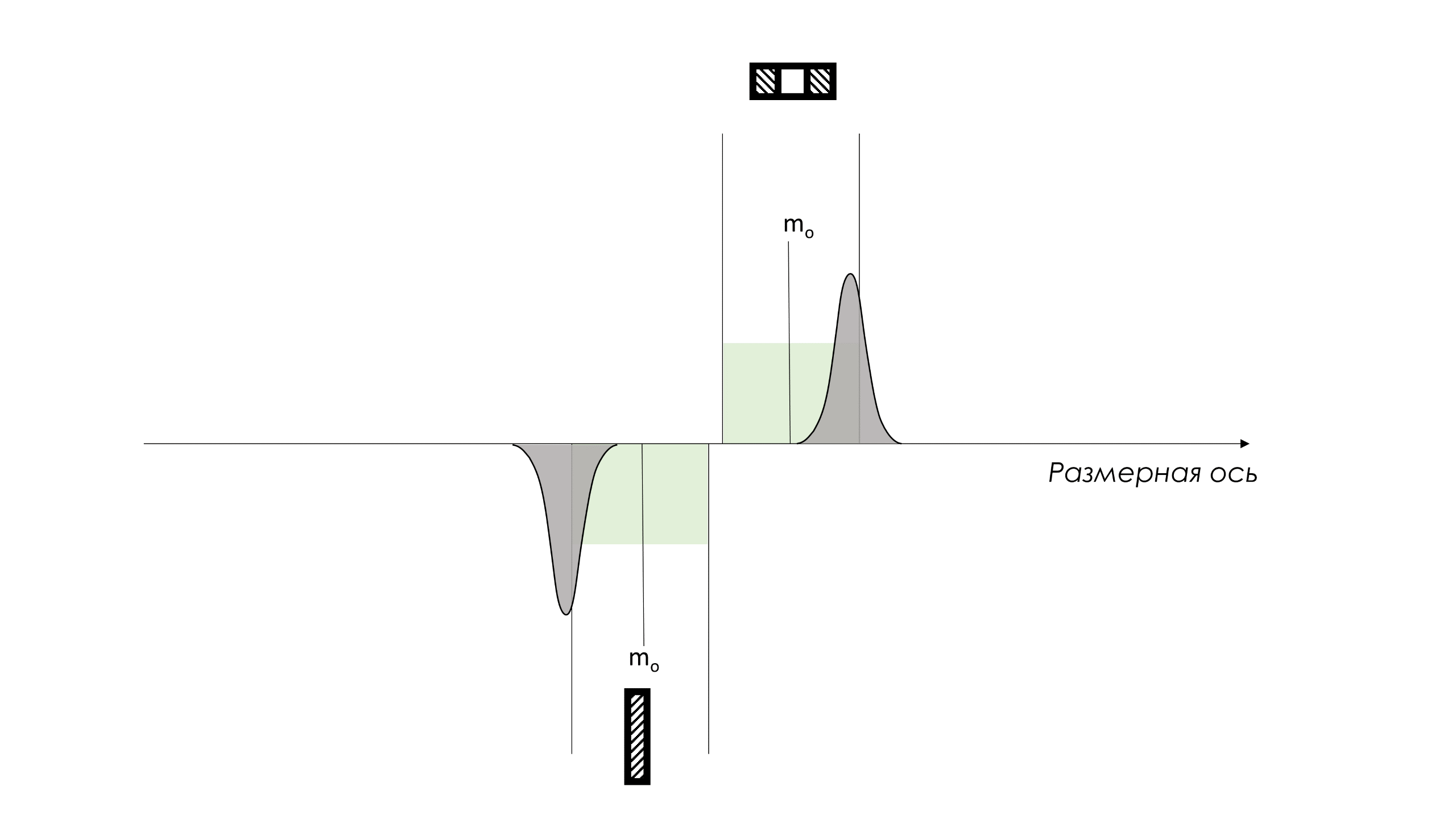
図 5. 生産プロセスは統計的に制御された (安定した) 状態にあり、その広がり 6σ は許容範囲の幅 (たとえば、Cp≥1.33) よりも小さいですが、中心にありません。
次に、生産プロセスが統計的に制御された状態にあり、その広がり 6σ が許容範囲の幅よりも大きく (たとえば、Cp<1.00)、完全に中心にある (たとえば、 、Cpk≒Cp)。また、製造された製品の一部は公差範囲外になります。生産されたすべての部品は、公差範囲に適合する部品とそうでない部品に分けられ、100%管理されなければなりません。この場合、一部の部品が公差を満たさないことが事前にわかっています。
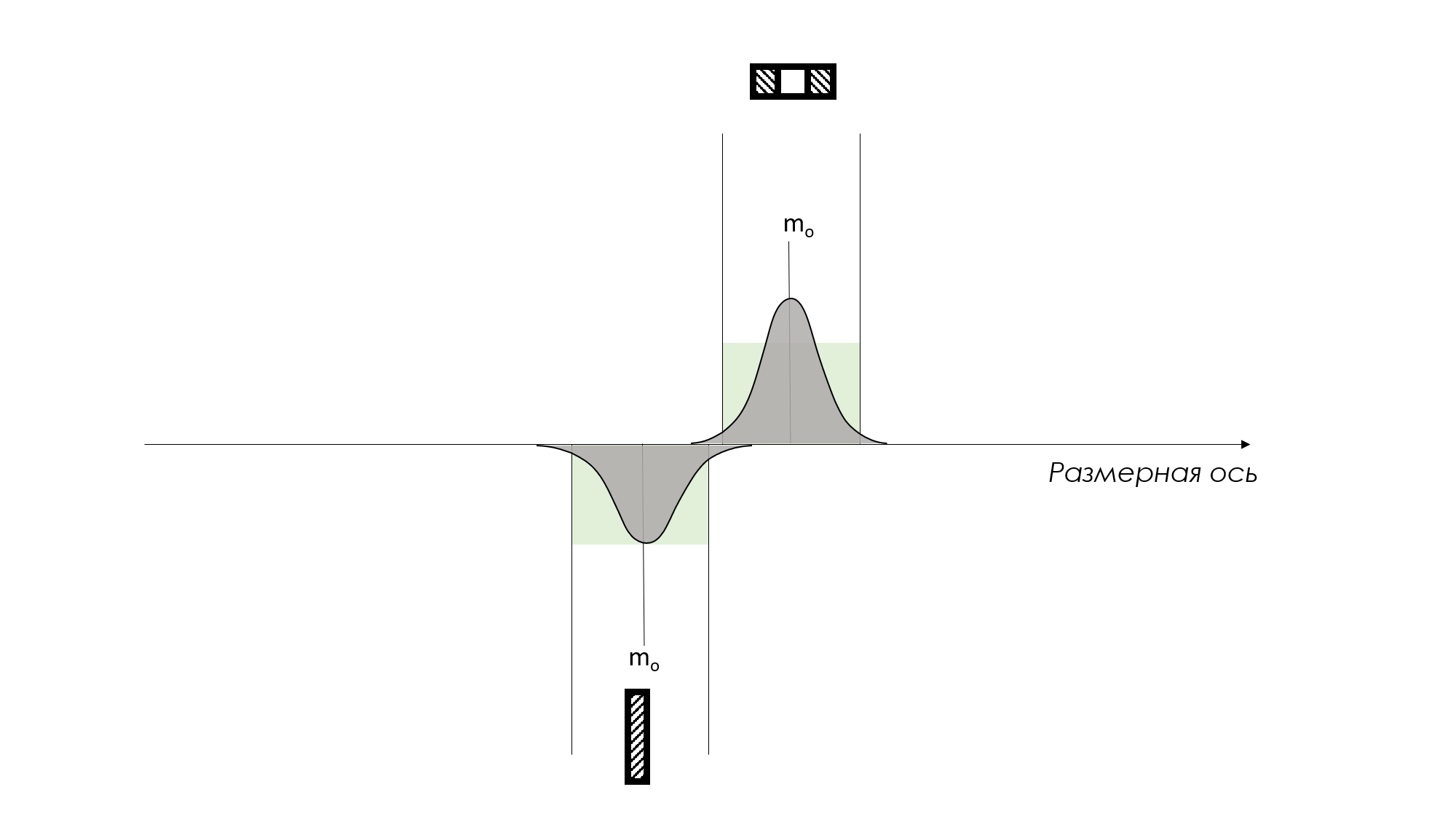
図 6. 製造プロセスは統計的に制御された (安定した) 状態にあり、その広がり 6σ は公差フィールドの幅より大きく (たとえば、Cp<1.00)、完全に中心にあります (たとえば、Cpk≈Cp)。
次に、生産プロセスが統計的に制御された状態にあり、その広がり 6σ が許容範囲の幅よりも大きく (たとえば、Cp<1.00)、中央に配置されていない (Cpk<) 場合のオプション (以下の図 7 を参照) を検討します。 CP)。そうなると、さらに多くの製品が許容範囲外となります。その結果は明らかです。生産されたすべての部品は、公差範囲に適合する部品とそうでない部品に分けられ、100%管理されなければなりません。この場合、半分以上の部分が不適切となることが事前に分かっている。
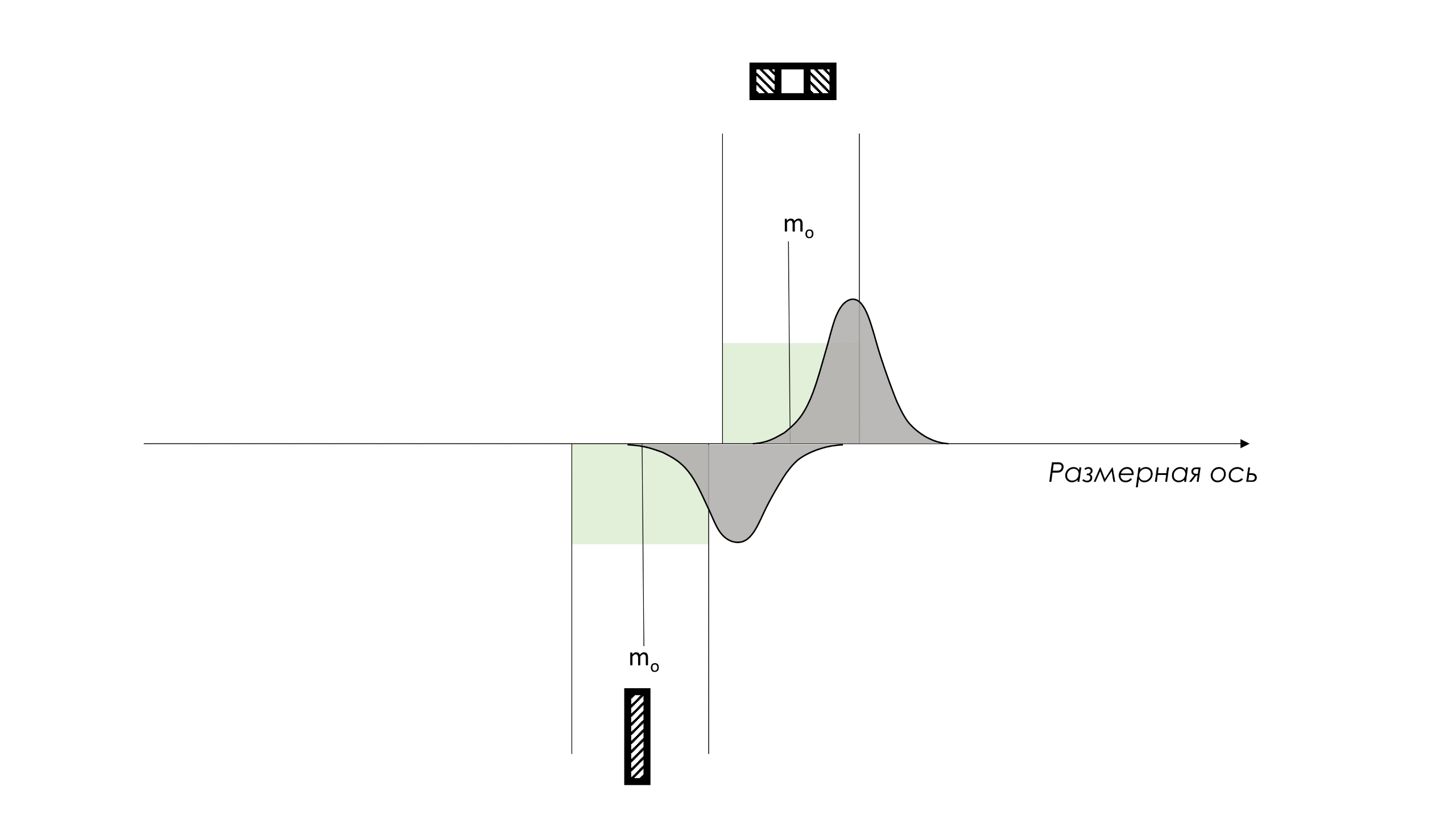
図 7. 生産プロセスは統計的に制御された (安定した) 状態にあり、その広がり 6σ は許容範囲の幅よりも大きく (たとえば、Cp<1.00)、中心化されていません (Cpk<Cp)。
以下の図 8 は、上の図 7 で説明した条件に一致する別のオプションです。繰り返しますが、その結果は明らかです。生産されたすべての部品は、公差範囲に適合する部品とそうでない部品に分けられ、100%管理されなければなりません。この場合、半分以上の部分が不適切となることが事前に分かっている。
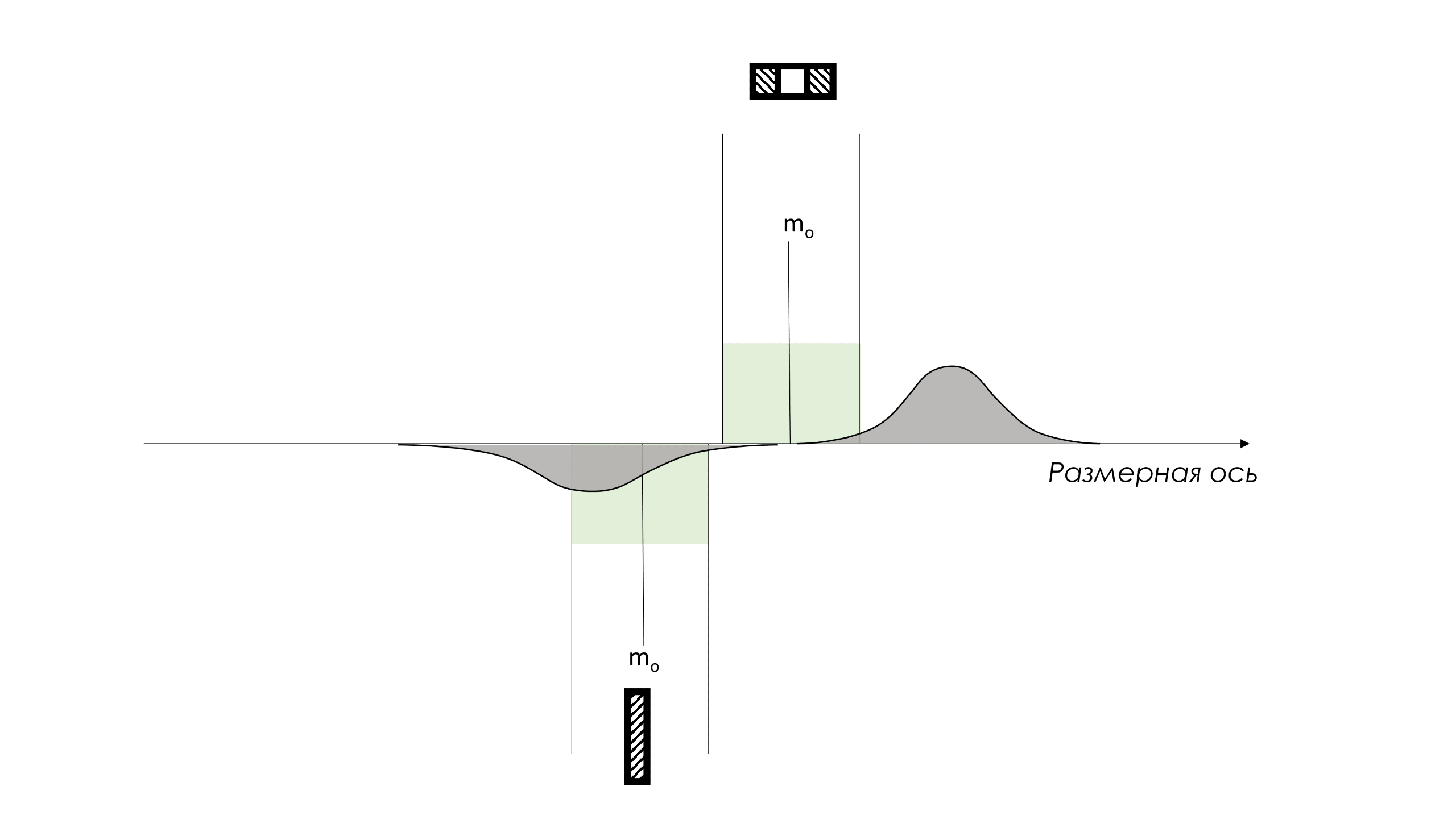
図 8. 図 7 のオプションの特別なケース。生産プロセスは統計的に制御された (安定した) 状態にあり、その広がり 6σ は許容範囲の幅 (たとえば、Cp<1.00) よりも大きく、中央に配置されます (Cpk<Cp)。
以下の図は、実際の生産プロセスが統計的に制御できない (予測できない) 状態にある場合の別のオプションを示しています。それらのスプレッド 6σ は予想外に狭くなり、その後拡大し、その平均も公称公差フィールドに対する位置が予想外に変化します。生産されたすべての部品は、公差範囲に適合する部品とそうでない部品に分けられ、100%管理されなければなりません。どれくらいの詳細が矛盾するか、おそらく 100% 矛盾するかは誰も事前にはわかりません。統計的に制御できないプロセスの動作を予測できる人は誰もいません。生産プロセスの予測不可能性による企業の損失総額は最大です。このようなプロセスで製造される部品は均一ではありません。
デジタル モデルは理想的かもしれませんが、会社全体としての損失は最大になる可能性があります。
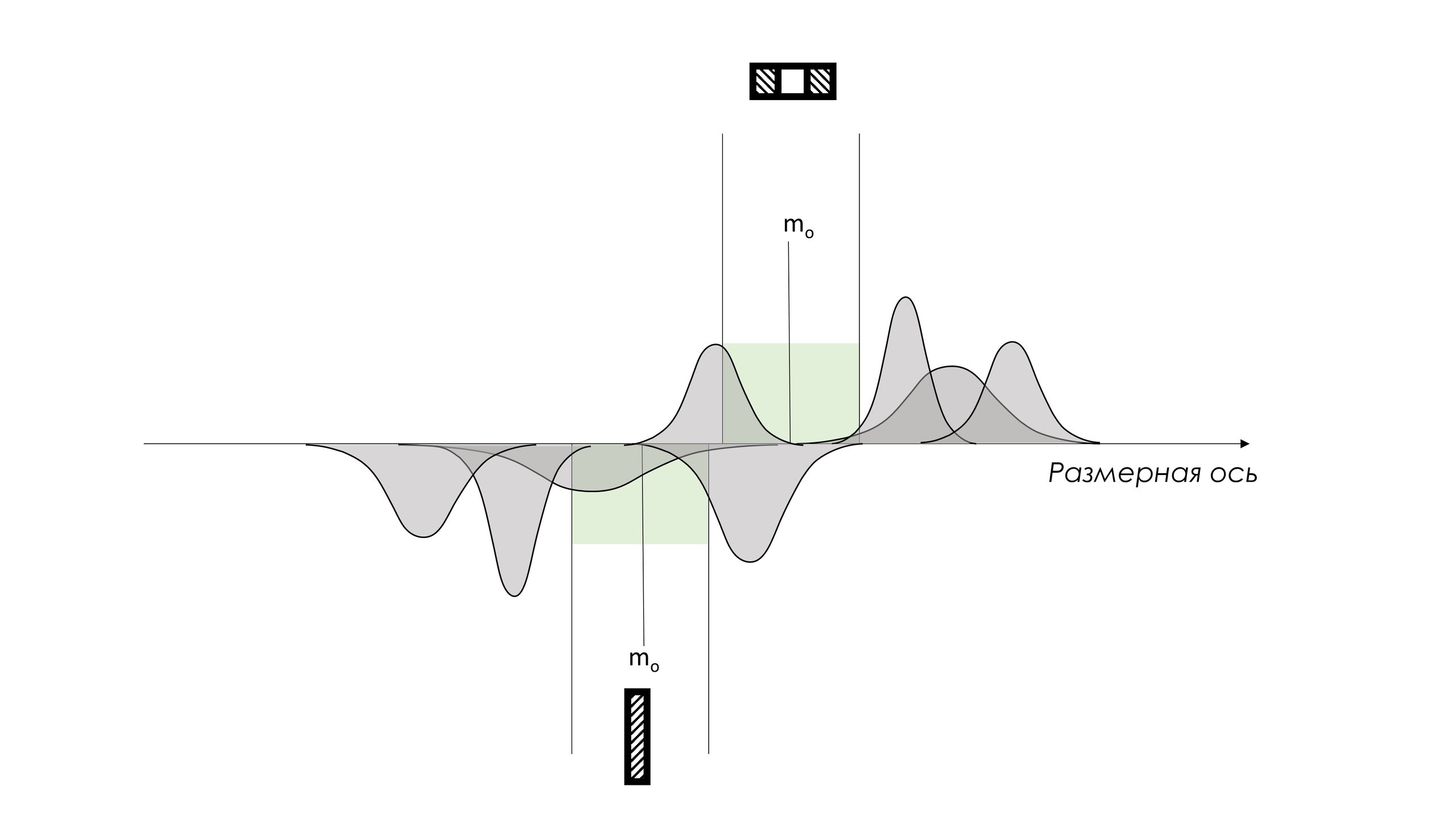
図 9. 生産プロセスは統計的に制御できない (予測できない) 状態にあります。それらのスプレッド 6σ は予想外に狭くなったり拡大したりし、その平均も公称公差フィールドに対するその位置が予想外に変化します。
この件に関する追加の重要な点は、測定システムの安定性の必須要件、より厳格な製造仕様における測定システムの誤差を考慮した測定システムの偏りの分析です。後者については、次の記事で説明します。 記載されている製品は実際に仕様に準拠していますか? 。
最後に、会社のすべての部門の活動を、システム全体として目標に応じて最適化する必要があるのではなく、デジタル モデルでの部分最適化に関連する問題にたどり着きました。たとえば、信頼性の高い製品の生産などです。オペレーターの所有コストを最小限に抑えたシリアル エンジン。
「部分最適化は、最適化よりも達成が容易です。しかし、部分最適化は安くはありません。部分最適化は改善の幻想を生み出すかもしれませんが、実際には、実際の進歩を妨げる障壁を生み出します。さらに、一部の部分最適化は、多くの場合、他の部分に害を及ぼすため、全体的な変化がさらに害を及ぼします。」 「それは有益ではありません。また、真に利益をもたらす変化を起こすことがより困難になります。」
さらに会話を続けると、この企業の生産管理者も設計者も、実際の生産プロセスが実際にどのように機能するかを知っていないことが明らかになりました。しかし、シューハート管理図は、状態を評価してプロセスを改善するためにはまだ使用されていません。
このような状況では、設計エンジニアは再び公称材料の公差フィールドと理論的特性に満足することになり、生産担当者は管理者の助けやばらつきの性質の理解なしに、 第一種および第二種のエラー 必要な特性を持つ部品を製造し、完成品を組み立てる試みです。
会社のさまざまな部門に個別の KPI を設定すると、事態はさらに悪化するだけです。
あなたの会社で何が起こっていますか?
エドワーズ・デミングは準備した 経営に役立つ質問 、その一部を次に示します。
- 生産プロセスは安定していますか?
- どうやってこれを知っていますか?
- どのようなデータがありますか?
- 製品設計、実際の生産、納品の間のギャップを埋めるために何をしていますか?
上記の質問に対する明確な答えがない場合、デジタル アセンブリ プロセスに頼って、フィールド テストをデジタル モデルのテストに置き換えることはできません。
「私たちは、材料、人的労力、機械時間の無駄を嘆いていました。企業が既存の潜在能力を活用し開発できないことで知識が無駄になることは、さらに嘆かわしいことです。」
デジタル モデルが果たすべき全体的なシステム目標を考慮せずに、デジタル モデル自体に部分最適化が行われている証拠が数多く見られます。すべては、生産プロセスに十分な注意を払わず、悪名高い開発生産性と、しばしば軽率なコスト削減を部分的に最適化するためです。
「成果物は、それが作成された目的を考慮せずに考えることはできません。」
製品開発者の効率が開発時間とコストの削減という観点から重視される環境では、現実の製品テストを仮想テストに置き換えることに依存することは間違いであり、会社全体にとって非常にコストがかかる可能性があります。これはすべて手抜きの試みです。シューハート管理図を使用して生産プロセスとアフターセールスデータを分析すると、設計プロセスの最適化がそれらにどのような影響を与えたかがわかります。
「ただし、改善手順が目標を達成しているかどうか、またそれが適切であるかどうかを判断するには、生産パフォーマンスの系統的な分析が必要です。」
実行された改善手順の有効性を分析するための最も簡単なツールは、シューハート管理図です。
以下の抜粋は、マービン・マンデルの『サービスおよび政府組織の生産性の測定と強化 - 東京都港区赤坂 8 丁目 4-14 青山第一マンション 107』、1975 年からのものです。 – ページ 3 ~ 4) がこれに光を当てています。問題:
「アウトプットは…システムが作成された目的を考慮せずに考慮することはできません。
背景を説明するために、いくつかの例を分析してみましょう。アメリカの偉大な発明家トーマス・エジソンは、この手続きを改善する投票機をアメリカ議会に提案したと言われています。彼は国会議長と上院議長にその装置をデモンストレーションしました。発明者のアイデアによれば、すべての議員と上院議員は椅子に 3 つのボタンを備えており、赤は「ノー」、緑は「はい」、白は「棄権」を意味します。
エジソン氏は、投票の開始時に参加者が対応するボタンを押すと、各人がどのように投票したか、全体的な結果がどうなったかに関するレポートが即座に表示されると提案しました。エジソンは上院議長と上院議長に対し、自分の装置が逐次点呼投票の方法で発生するエラーを排除し、投票時間を大幅に短縮し、その他の利点を提供すると誇らしげに保証した。
下院議長と上院議長が判決の途中で彼の発言をさえぎり、そのような制度はまったく望ましくなく、下院や上院の仕事を改善するどころか、議会の秩序を完全に混乱させるだろうと宣言したとき、彼は完全にショックを受けた。米国議会の円滑な機能。エジソンの観点からは改善でも、議会の観点からは逆に悪化でした。点呼プロセスの長さは、議会が何をすべきかを決定する審議プロセスに不可欠でした。
エジソンの提案、つまり即時投票は議会の目的と矛盾していた。」
何をするか?
まず第一に、管理スタイルを変更し、 致命的な病気と変革への障害 。
製品を設計するときは、公差表の使用を超えて、形状、材料特性、その他の特性に固有の変動を伴う現実世界のプロセス能力を考慮してください。
製造仕様 (公差) は、測定システムの誤差を考慮する必要があり、少なくとも 96% の確率で欠陥製品を管理していないことを考慮する必要があることに注意してください。つまり、測定システムの 2 つの可能性のある誤差に対する顧客の公差よりも狭いことになります。フィールドの両側からクライアントがアクセスします。測定システム自体が安定している必要があります。説明については、この記事を参照してください。 記載されている製品は実際に仕様に準拠していますか?
経験豊富なインストラクターの指導の下、シューハート管理図を使用して、設計の変更や公差の変更を推進したり、必要に応じて製造部門やサプライヤーにプロセスの改善を要求したりできます。また、空の応答文に満足せず、製品とプロセスの主要な特性の管理図の形式で品質特性を統計的に確認することを要求してください。
以下の短いビデオで、生産プロセスを改善するための推奨事項を示しました。
ビデオ 1. プロセス改善ロードマップ。ビデオ内の要素の記号: НГД および IOP - それぞれ下限および上限許容限界 (Eng、LSL、および USL)。 m0 - 公称公差フィールド。 LGP および ВГП - プロセスの下限および上限 (英語の LCL および UCL)。 CL - プロセスの中心線 (平均)。
設計、製造、購買、販売部門間の情報交換とチームワークの確立における本格的な支援は、世界標準クラスの新しい品質管理ツール (QMS ソフトウェア) によって提供されます。 SPC R&D モジュール QM を使用し、シューハート管理図を使用して自社の生産プロセスとサプライヤーのプロセスの両方の主要な品質特性の変動に関するデータを使用します。
当社は、当社のすべての機能を統合して提供します。 ソフトウェア ロシアの企業アプリケーションへ: CAD (CAD)- 、 PLM- 、 ERP 、 MES- 、 LIMS システム 、トレーニングを実施し、従業員に効果的な科学的かつ実践的なサポートを継続的に提供します。
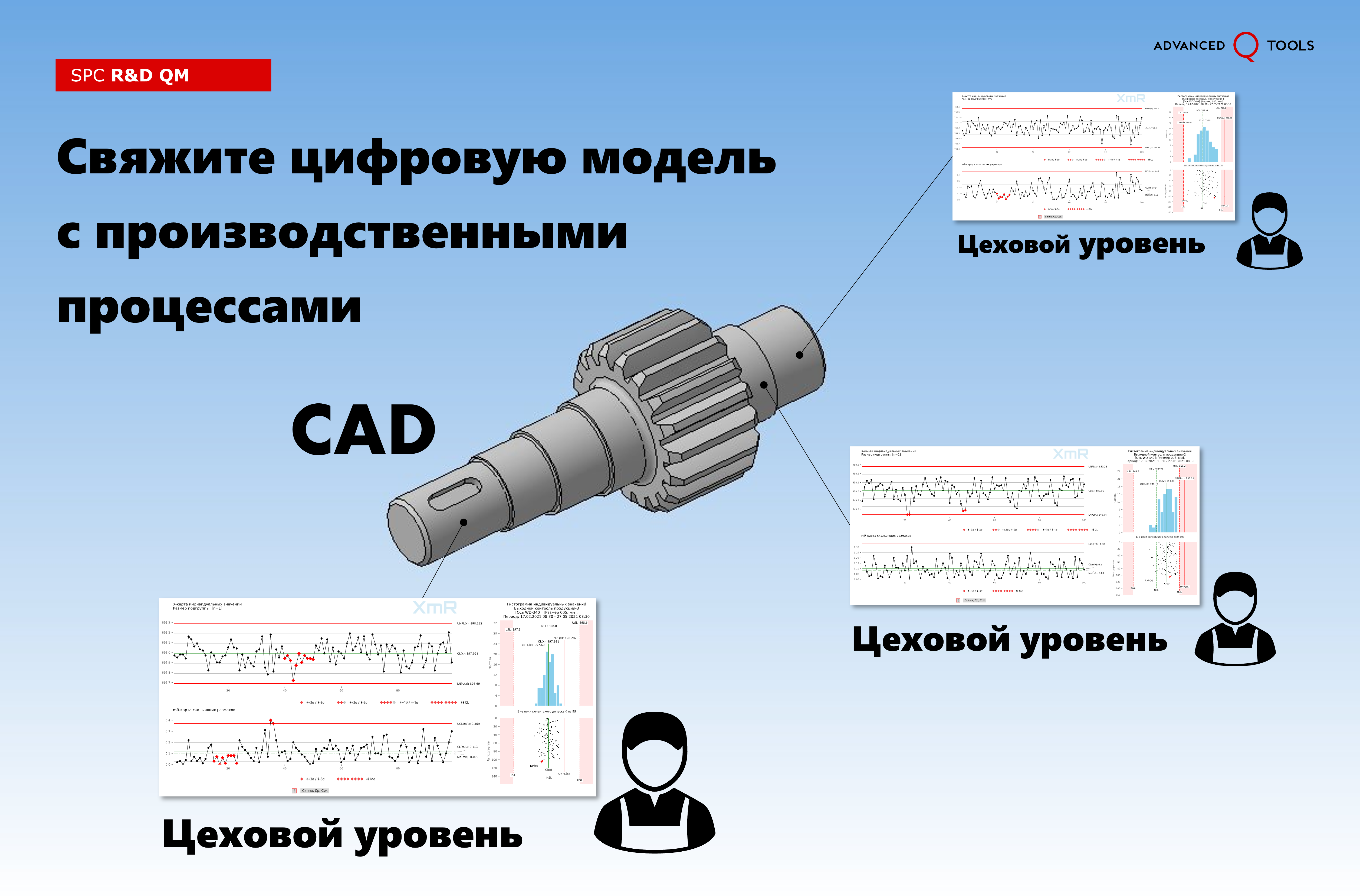
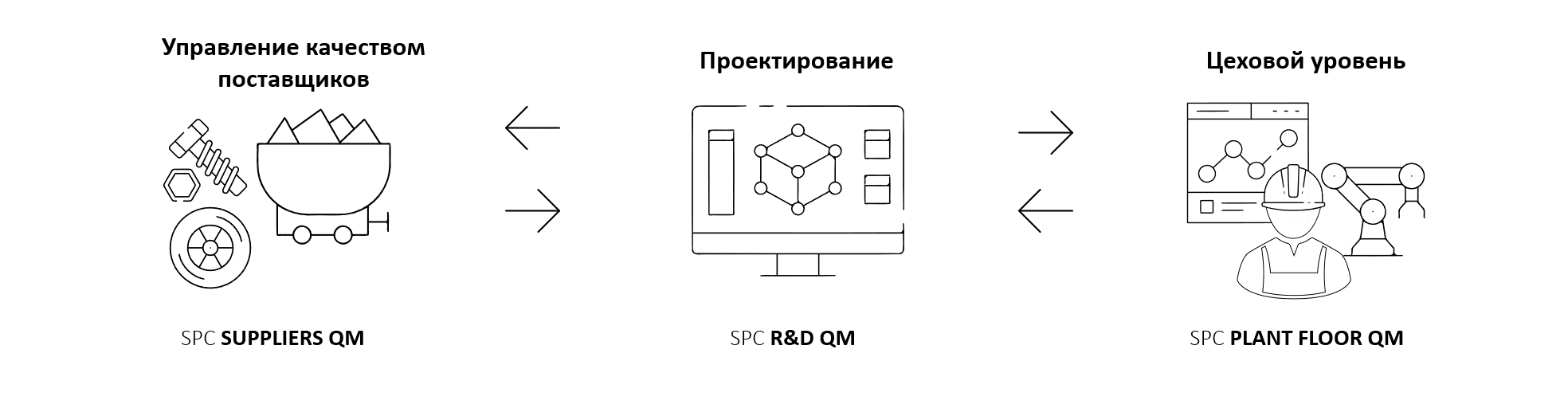
図 10. 次世代品質管理ツール SPC R&D QM。サプライヤーの品質管理、設計、生産機能の相互作用。
製品設計モジュールで統計的プロセス制御を使用する一例は、次のとおりです。 IBS QMS – シーメンス PLM ソフトウェアによって開発された、業界を超えた QMS (品質管理システム) クラスのソリューション。
繰り返しになりますが、統計的工程管理 (SPC) 手法を深く理解せずに断片的かつ非体系的に使用しても、企業全体に大きな改善はもたらされません。
「管理図を効果的に使用しようと計画している組織は、まず分析を行う必要があります。 すべての障壁 デミングによって説明されました。
「統計的工程管理を実装する」だけではだめです。管理図は単独では機能しません。これらを使用すると、労働者と経営者に一定の要求が課せられるため、組織はこれらの要求を満たすためにあらゆる手段を講じる必要があります。管理図の考え方が企業文化の一部、さらには組織そのものの構造の一部になれば、労働者や経営者からの時折の介入はもはや何も妨げられなくなります。
統計的プロセス制御は、まず第一に、特定の方法によってサポートされる全体的な世界観です。それは考え方であり、それがすべてです。このような考えがなければ、メソッドはまったく役に立ちません。継続的改善のための管理図の重要性を強調できるのは上級管理職だけです。上級管理者がこれに対して積極的なサポートを提供すれば、管理図の導入による潜在的な影響は予想を超えるでしょう。 」
最後に、密接に関連している 4 つの部分のうちの 1 つを思い出していただきたいと思います。 深い知識システム 、エドワーズ・デミングによって形式化されたもの、つまり、システムの理解という観点から。そして、システムのどの部分(部門)の部分最適化にも夢中になるのではなく、主な目標に向けてシステムのすべてのコンポーネントの相互作用を改善することに重点を置くことを提案します。
「システムとは、組織の目標を達成するために連携する、組織内の相互に関連する機能や活動の連鎖です。
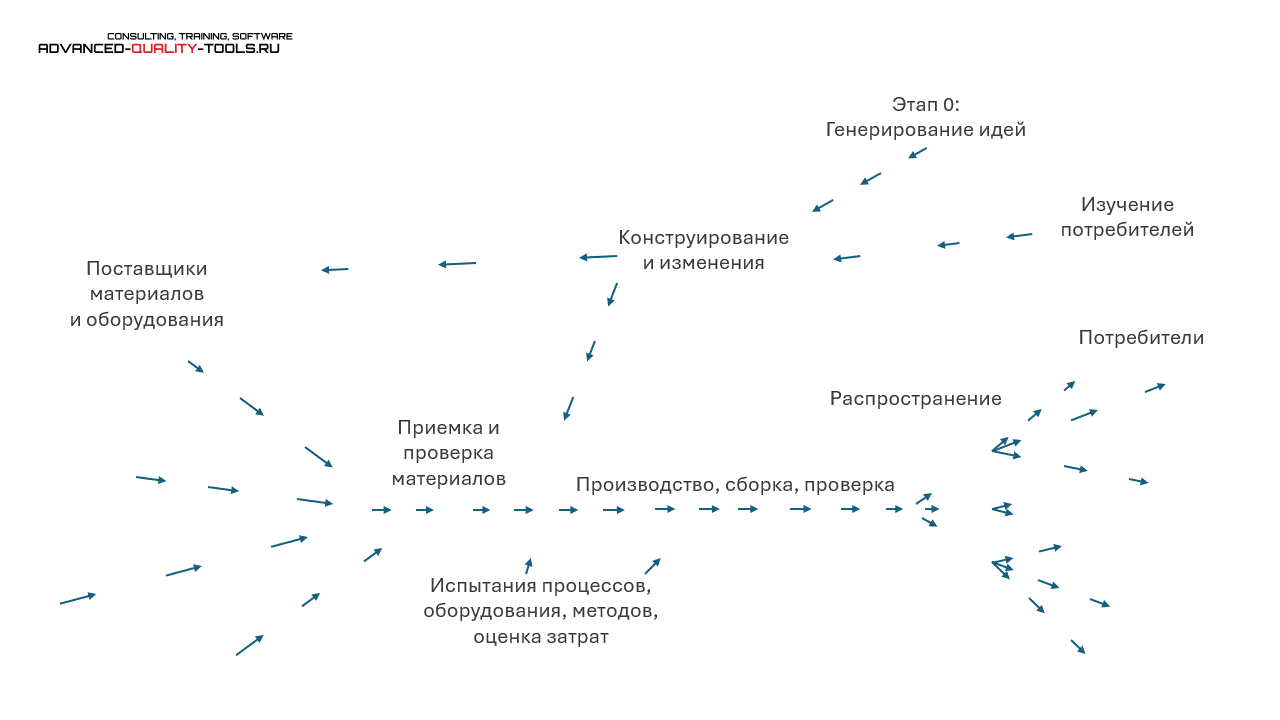
図 11. 生産はシステムとして考慮される (エドワーズ・デミングによる講義資料、1950 年、日本)
この図は、物の流れだけでなく、会社をシステムとして運営するために必要な情報の流れの方向性を示しています。フレームワークを使用すると、製品やサービスの継続的な改善や継続的な学習のためのフィードバックが得られます。」
参考のため
外国の産業企業は、設計プロセスを改善するために二次元 (2D) 統計分析手法を使用し始めて久しいです。以下は、1998 年のボーイングの文書のページのスクリーンショットです。セクションからダウンロードできます。 参考文献 私たちのサイト。
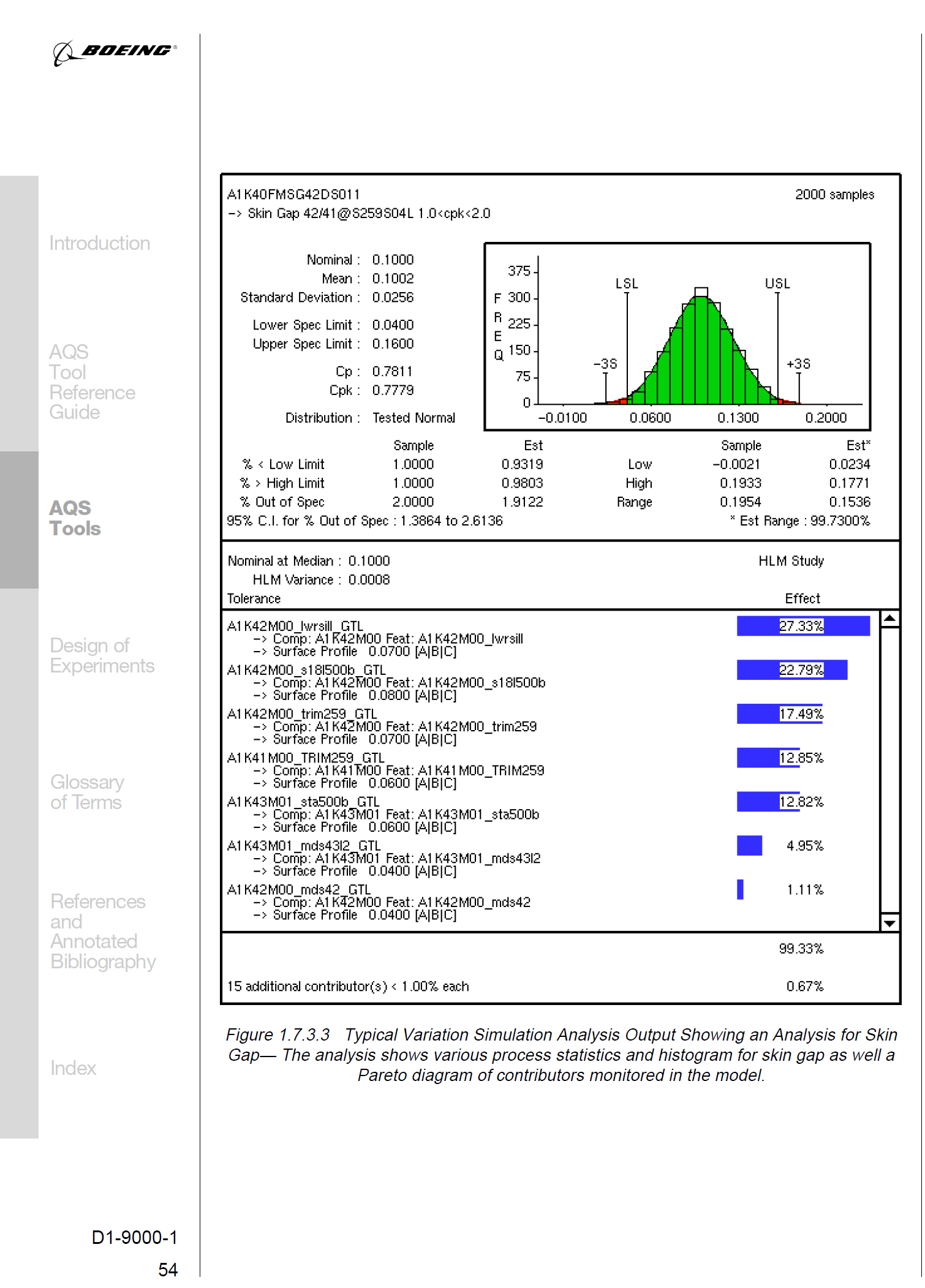
図 12. GD&T (幾何寸法と公差) 分野における 2 次元 (2D) 統計的変動解析。ボーイング社の小冊子「高度な品質システム ツール」のページ | 「高度なボーイング品質システムツール」、1998年。
さらに、GD&T (幾何学的寸法と公差) の分野における 3 次元 (3D) 統計的変動解析も、欧米の大手企業で長年使用されてきました。
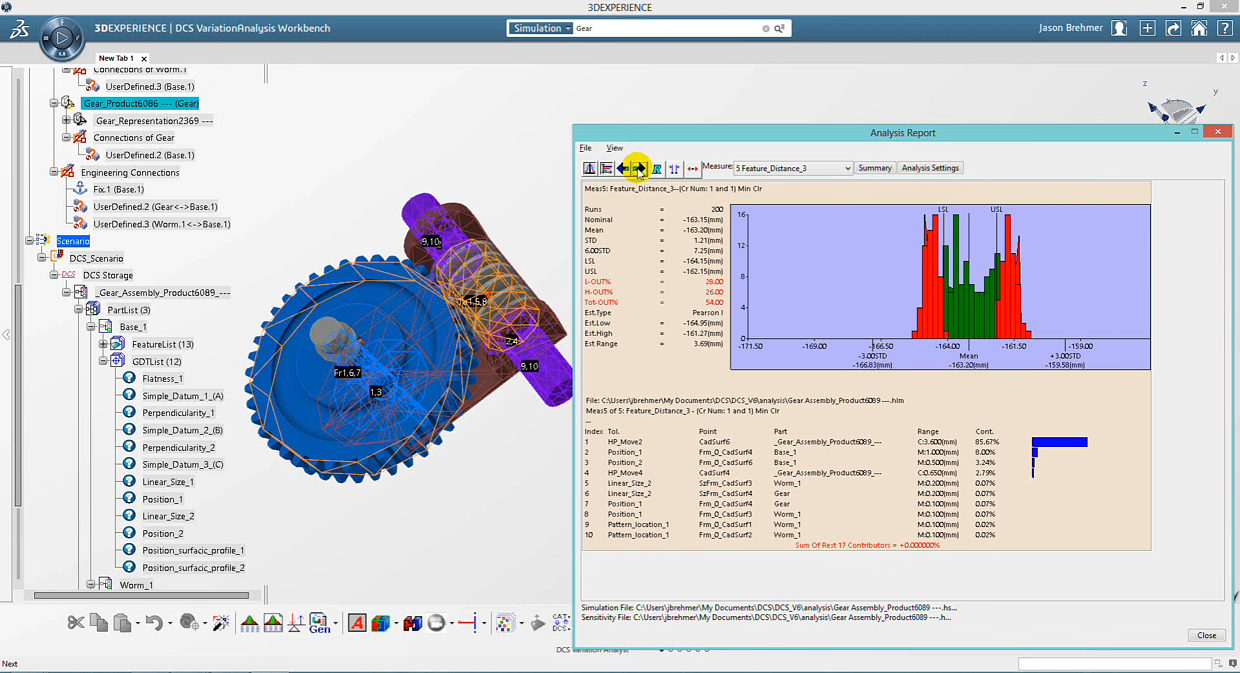
図 13. GD&T (幾何学的寸法と公差) の分野における 3 次元 (3D) 統計的変動解析。アメリカの会社 Dimensional Control Systems Inc. のソフトウェア製品 3DCS variation Analyst は、スタンドアロン ツールだけでなく、CAD CATIA V5、SOLIDWORKS、CREO、NX、3DEXPERIENCE に統合されたツールとしても使用されます。
これらの企業は、GD&T (幾何寸法および公差) の分野で自動シミュレーション ツールを使用して、デジタル モデル内の公差フィールドが正しく配置されていることを検証します。したがって、たとえば出版物では、 [22] 1998 年のボーイング社の「Advanced Quality System Tools」(51 ページ)には、3 次元統計的変分分析の目的と動作原理が説明されています。この問題の詳細については、ドキュメントを参照してください。 [23] ボーイング社レポート ISSTECH-95-030、「公差スタック分析方法」、Fritz Scholz 著 (1995) のセクション 参考文献 私たちのサイト。
そして彼らは間違いを犯すかもしれない
3D 統計的ばらつき分析は、設計された製品 (デジタル モデル) のばらつきを理解するための次のステップですが、生産プロセスの実際のばらつきとは関係がないため、高度な部分最適化です。
2D、3D統計変動解析の弱点
1. プロセスは統計的に制御できない (予測できない) 状態にある可能性があるため、そのような分析は純粋に理論的になります。
2. 安定したプロセスの制御された特性の広がりは、許容範囲よりも広く動作するか、許容範囲を超える可能性があります。同時に、生産管理が許容範囲外の製品の一部を、たとえば「品質クラス」を下げることによって保存することを決定した場合、変動分析では組み合わせの可能なオプションのアイデアが得られません。そういった部分。
3. 安定したプロセスの制御特性の広がりが許容範囲内で動作する場合、現実には起こらないオプションの計算を無駄に行うことになります。
4. プロセスが公差フィールドの中心に正しく配置されていない場合は、上記の段落 2 および 3 で間違いを犯すリスクがあります。