新しい機械、ロボット、デバイスは万能薬ではありません。
資料作成者: AQT センター科学ディレクター セルゲイ・P・グリゴリエフ 。
記事への自由なアクセスは、記事に含まれる資料の価値を決して減じるものではありません。
生産性と品質管理における最も物議を醸すトピックの 1 つである、一般的なロボット化と新しい機器の購入に対する情熱に関する資料を紹介します。新しい機器の購入を本格的に検討する時期はいつですか?
「現在の問題を解決し、自動化、設備、新しい機械を導入することで業界を変革するという仮定
「品質はお金では買えません。」
この事件を書くきっかけとなったのは「画家とロボットの決闘」という記事だった。
「2年前、トゥルボデタール工場では、パイプライン接続部品に防食コーティングを施すプロセスのロボット化を試みました。彼らは、コーティングの厚さをわずか 1 ミリメートル減らし、基準の下限値内で物質を均一な層に塗布すれば、1 年でかなりの節約ができると計算しました。
現在、この工場での作業は塗装工によって行われています。彼らは重いペイントガンを手に持ち、ホース(「ボアコンストリクター」)を首からかけ、そこからポリウレアベースの2成分コーティング剤が供給され、衣服は白い防湿オーバーオール、顔にはほぼガスマスクのようなマスクを着用しています。大変な肉体労働です。同時に、なぜ楽にしないのでしょうか。
有名企業の万能ロボットアームがテストのために持ち込まれました。画家とロボットの間で行われた決闘を見たことがあるはずです!作業員らから「片腕の山賊」と呼ばれたこの男は、コーティングを均一に塗ることができず、さらに側面に大量のユリア樹脂を飛散させたため、コーティング成分の消費量が3倍に増えた。
機器インテグレーター会社の代表者がどんなに奮闘しても、結局は欠陥品でした。決闘に勝つ可能性はすべてロボット側にありましたが、機械の手は震えず、スプレーガンを持っていても疲れず、熱くも冷たくもありません。その間、塗装職人は落ち着いて曲がり角の塗装を終え、機械が簡単な作業に苦戦する様子を観察し、コントロールパネルを手に持ち、作業を続けました。
トゥルボデタールの画家たちは、ロボットを肉体的にも精神的にも打ち破った。
良い点が 1 つありました。鉄鋼の競合他社が工場に参入したことで、塗装職人の労働生産性が前例のないほど上昇しました。最初のプレゼンテーションからの歩留まりはすぐに 98 ~ 100 パーセントに増加しました。同時に、画材の消費量は急激に減少しました。
工場はこのプロセスをロボット化するというアイデアを諦めていません。ただ、価値のある提案がまだ見つかっていないだけです。ここで、ロボットの購入は価格の問題ではないことに注意してください。すべてはもっと複雑です。 Trubodetal では、コンベア生産ではなく、ピース生産が行われ、1,000 を超える標準サイズの膨大な範囲の接続部品が製造されているため、製品の形状を個別に「見て」、最も多くの設定を行う汎用ロボットが 1 台必要です。経済的な塗料供給モードで、繰り返し操作を実行し、スキャンして結果を記憶すると、彼は自分の間違いから学び、プログラマーの介入なしで、まったく異なるタイプとサイズの製品の塗装にすぐに切り替えます。指定されたコーティングの厚さが異なります。そうしないと、製品の種類ごとに個別のロボットが必要になりますが、もちろん、これは非常に贅沢なことです。」
コメント
この記事は、デジタル化とロボット化の全体的な有効性に関する現代の情報トレンドから明らかに際立っています。
同時に、この記事は、Trubodetal の従業員による変動の性質についての誤解の証拠を示しています。
「私たちが計算したところによると、コーティングの厚さをわずか 1 ミリメートル減らし、基準の下限値内で物質を均一な層に塗布すれば、1 年でかなりの節約が可能になります。」
残念ながら、人間もロボットも、現在または 50 年後には「基準の下限内に収まる物質を均一な層に塗布する」ことはできないでしょう。これは現実の可変世界では不可能です。さらに、塗装業者が「最低ライン」を目指す場合、コーティングプロセスが統計的に制御された状態 (プロセスが可能な最良の状態) にある限り、約半分の時間で厚さは最低ラインよりも小さくなります。図 1 を参照してください。 。
コーティングプロセスが統計的に不安定な状態にある場合、誰もその結果を予測できません。
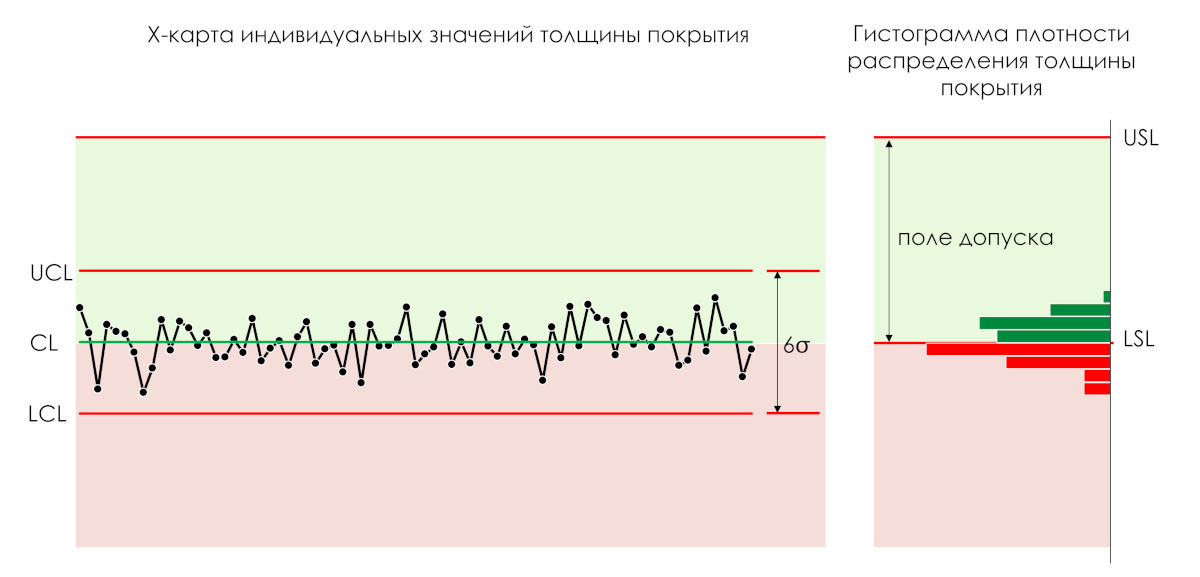
図 1. 許容下限を中心とした安定したプロセスコーティングの厚さ値のシューハート管理図と分布密度ヒストグラム。 UCL - プロセスの上限管理限界、CL - プロセスの中心線、LCL - プロセスの下限管理限界、6σ - プロセス スパン、USL - 許容範囲の上限、LSL - 許容範囲の下限。
私の発言を理解するには、次のことを理解することが重要です 変動性の性質 つまり、材料の特性、プロセスの「入力」と「出力」は変動性によるものであるということです。たとえば、部品の表面に 2 成分ポリウレアベースのコーティングを施すプロセスでは、変動性を考慮することが重要です。
- バッチ内およびサプライヤーバッチ間の両方の 2 つのコーティング成分のそれぞれの品質指標。
- 処理対象の表面に塗布する前に調製されたコーティングの二成分組成物(成分の混合物)の品質指標。
- コーティングのための表面処理の品質の指標。
- コーティングチャンバー内の環境品質インジケーター。
- コーティングを人間が行うかロボットが行うかに関係なく、製品の表面に 2 成分コーティングを塗布するための品質指標。
- 投入材料の品質、プロセス操作の品質、および最終出力を測定するために使用する測定システム (安定性、測定システム誤差、一貫性、バイアス)。
プロセスを悪化させるリスクを冒さずにプロセスを改善するには、以下のことが同様に重要です。 操作上の定義 部品のコーティングプロセスのすべてのコンポーネントの変動性を評価するために必要となる(方法、基準、決定)。
コーティングの厚さを決定するために使用している機器が実際に何を測定しているのか、つまり、特定の領域の最小、平均、または最大の厚さを理解することが重要です。

図 2. 顕微鏡で見たときの保護コーティングの厚さと保護表面の曲率。
さらに、誤差とオフセットについて理解しておく必要があります。 測定システム
ばらつきをなくすことはできませんが、ばらつきを減らすことはできます。まず第一に、プロセスを統計的に安定した状態にする必要があります。また、許容範囲の値が規制されておらず、製造許容範囲の下限で良好なコーティング品質が確保されている場合は、平均プロセスを設定してプロセスを統計的に安定した状態にした後でのみ、製造公差フィールド内のコーティング厚指標 (6σ 幅フィールド) を、プロセス下限と製造公差の下限の間に安全ギャップを設けて、その下限にできるだけ近づけます。同時に、保護コーティングを改善して、より薄い厚さでより優れた保護を提供し、コーティングプロセスの変動を最小限に抑える必要があります。シューハート制御カードによってばらつきの減少が検出された場合は、平均値を再度調整して、製造許容値の下限に向けてシフトします。
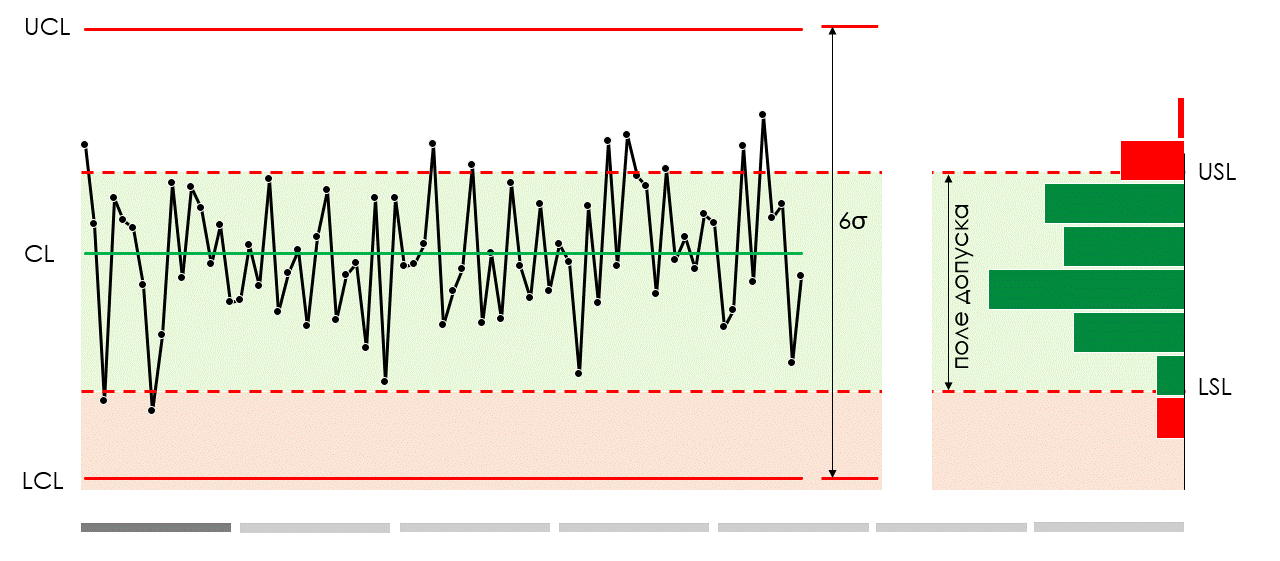
図 2. コーティングの厚さを最小限に抑えながら、公称値以外の公差内でプロセスを設定する正しい方法。
製造公差 (測定システムの誤差を考慮して狭められた通常 (顧客) 公差の領域) に関して、製品を不良品と良品に分類する必要性の詳細については、Donald Wheeler による記事を参照してください。 記載されている製品は実際に仕様に準拠していますか?
継続的改善へのこのアプローチは、シューハート・デミング PDSA サイクル (誤って PDCA と呼ばれることもあります) と完全に一致しています。
ビデオ 1. シューハート・デミング サイクル PDSA (Plan-Do-Study-Act、デミング サイクル)。品質管理分野の主要規格である ISO 9001 および多くの業界規格の基礎となっています: IATF 16949 (自動車産業) 、ISO TS 22163 (IRIS - 鉄道産業)、EN/AS 9100 (航空)、GOST RV 15.002 (防衛産業)、STO GAZPROM 9001 など。PDCA (Plan-Do-Check-Act) と呼ばれることがよくあります。
「PDSA サイクルの概念を初めて知ったとき、15 分以内にこのモデルについて知っておくべきことはすべてわかったと思いました。数十年にわたる積極的な実践と研究を経て、いつかはこのモデルについて十分に理解できるようになるだろうと思います」コンセプト "。
「基本的な統計を無視するエンジニアやマネージャーは、より信頼性の高い製品を開発する方法を考える気になれず、生産プロセスを制御するために多額の費用を費やさなければなりません。マネージャーが変動の影響を取り除くために巨額のお金を費やすのではなく、その方法を学ぶためにそれを減らすために、私たちは彼らのアプローチを「テクノロジー修正」と呼んでいますが、競合他社が不確実性を処理できる完全に自動化されたプロセスに何百万ドルも費やしている一方で、変動性を管理し、それから生産を保護する方法を学べば、それは可能です。競合他社の価格を引き下げます。このように推論すると、トヨタがゼネラルモーターズ向けに設置したNUMMI工場が、自動化が最も進んでいないにもかかわらず、最高品質の工場の1つである理由が理解できるだろう。」
引用の説明については、次の記事を参照してください。 許容値フィールドの正しい使用方法と誤った使用方法。不良品と良品の許容範囲に従って製品を分類する必要がありますか、それともプロセスをカスタマイズする必要がありますか?
新しい機器の購入をいつ検討すべきでしょうか?
新しい機器について本当に考える時期についての決定は、1982 年に初めて出版された著書 [2] Out of the Crisis の序文の中でエドワーズ・デミングによって示されています。
「コスト削減の一例。
1981 年 3 月にナシュア コーポレーションの社長ウィリアム コンウェイがリオデジャネイロで行ったスピーチを考えてみましょう。
「当社の最初の大きな成功は 1980 年 3 月に起こり、カーボンフリー コピー用紙の生産における品質の向上とコストの削減でした。
ロールから巻き戻される紙に、さまざまな化学物質を含む水性コーティングが塗布されました。報道範囲が十分であれば、消費者は鮮明なコピーを手に入れることができ、数か月後にこの新聞のおかげでそれを受け取ることができました。コーティングヘッドは、6 ~ 8 フィート (2 ~ 2.5 m) のロール上で毎分約 1,100 直線フィート (335 m) の速度で、紙 3,000 平方フィート (280 m2) あたり約 3.6 ポンド (1.63 kg) の乾燥コーティングを使用します。 ) 広い。鑑定人は紙のサンプルを採取し、それをテストしてコピーの強度 (濃度のレベル) を決定します。これらのテストは、消費者による紙の使用をシミュレートするために、新しくコーティングされオーブンでエージングされたサンプルに対して実施されました。テストの結果、適用範囲が少なすぎるか多すぎることが判明した場合、オペレーターはインク流量*を増減してヘッドを調整します。新しい調整のために頻繁に立ち止まるのが生活習慣になっています。しかし、これらの停留所には代償が伴いました。
エンジニアは、平均コーティング層が高すぎることを認識していましたが、コーティングが使用できなくなる危険を冒さずに平均コーティング層を減らす方法を知りませんでした。新しいヘッドを購入するという選択肢も検討されましたが、それには70万ドルかかりました。これは、70 万ドルのコストに加えて、設置時間の損失と、新しい設置では既存のものより優れたコーティングの均一性と費用対効果が得られないというリスクを意味します。
1979 年 8 月、工場長が助けを求めてきました。頭部に手を触れずに放置した場合、結果は統計的に管理されており、平均被覆率は 3.6 ポンド (誤差は 0.4 ポンド) であることがわかりました。管理限界(シューハート管理図)外の点によって特定されるさまざまな変動原因を排除することで、一貫して良好な品質を維持しながらコーティングの消費量を削減することが可能になりました。 1980 年 4 月までに、流量は 3,000 平方フィートあたり平均 2.8 ポンドに低下しました。 2.4 ~ 3.2 フィートの範囲で、3,000 平方フィートあたり 0.8 ポンド (3.6 ~ 2.8) の節約になり、既存の量と価格レベルで年間 800,000 ドルの節約になります。」
* ヘッドをチューニングするこれらの人々の行為は、ルール 2 またはルール 3 に準拠しています (「 「ファネルとターゲットを使ったモンテカルロ実験」 )、それによってコーティングの厚さの広がりが急激に増加しました。つまり、彼らは目指していたものとはまったく逆の結果を得ました。
プロセス改善のためのイノベーション。
コンウェイ氏が語った話の結末はもっと興味深い。統計的管理はエンジニアリングの革新への道を切り開いた。それがなければ、プロセスは混乱状態にあり、改善の試みの結果を測定することはできなかった。そして統計局はエンジニアと化学者が発明と創造力を発揮することを可能にした。彼らは今や透明で測定可能なプロセスを手に入れた。彼らはコーティングの化学組成を変更し、毎回より少ない材料を使用することを学んだ。消費量を 10 分の 1 ポンド削減することは、材料コストを年間 10 万ドル削減することを意味する。
エンジニアはヘッドの設計も改良し、より均一なカバレージを実現しました。これまでずっと、統計的プロセス制御によりコーティング層が薄くなり、値の広がりは減少し続けていました。
新しい機械や装置は万能薬ではありません。人々が設備の効率的な使い方を学んだことで、品質と生産性において重要な結果が達成された例を今見てきました。
社説や新聞への投書では、アメリカの生産性レベルの低下は、新しい設備や装置、ロボットなどの新しいタイプの自動機械の不適切な使用が原因であるとされている。このようなエッセイは読むのが面白く、生産上の問題について何も知らない人に書くのはさらに興味深いものです。
次の段落は、大手製造会社の従業員である私の友人からの手紙から借用したものですが、これまでに述べられてきたことを説明するものとして役立ちます。
「このプログラム全体(新しいマシンの開発と設置)は失敗に終わりました。これらの優れた機械はすべて、テスト中にその機能を発揮しましたが、工場で稼働し始めると、頻繁に停止したり、深刻な故障が発生したりするため、総コストは下がるどころか急激に上昇しました。これまで誰も、予想される故障と修理の数を評価していませんでした。その結果、ダウンタイムとスペアパーツの不足により大混乱に陥り、スペアパーツが欠如しているため、代替の生産ラインも想定されていませんでした。」
オフィスや工場での自動化ツールや自動データ記録も解決策にはなりません。そのような機器が展示される展示会には、生産性のギャップを克服する簡単な方法を探している何千人もの人々が集まり、命を救う機器を信頼しています。一部の技術は、それ自体でしか採算が取れませんが、新しい機械、デバイス、優れたアイデアの組み合わせによる効果は、衰退を乗り越えた企業の経営陣が提供しなければならない質的改善のほんの一部にすぎません。
もし私が銀行家だったら、ローンを申請している会社が既存の設備の可能性を最大限に活用し、次のことに取り組んでいるという統計的証拠を提供するまで、新しい設備にお金を貸しません。 14点 そして戦う 致命的な病気と障害 」。
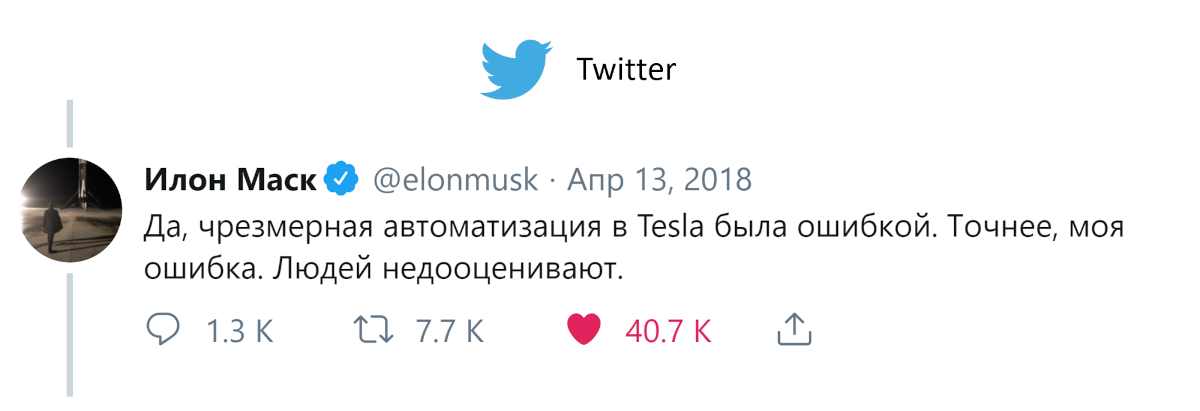
図 2. イーロン・マスクのツイートのスクリーンショット (イーロン・マスク、Twitter)。