1978年に日本で行ったエドワーズ・デミングの演説。
「新しい経営原則の概要」
以下は、1978 年に日本科学技術者連盟 (JUSE) のために W. エドワーズ・デミングが東京で行った忘れ去られた演説の書き起こしです。オリジナルは粗末なコピーであったため、解読できないテキストの小さな部分があります。成績証明書はマイク・マクリーン氏のご厚意によりデミング研究所 (米国) に提供されました。ソース: www.qualitydigest.com
記事の翻訳にはコメントと、Web サイト上のサポート資料へのリンクが追加されており、別のブロックで斜体で強調表示されています。翻訳とコメント:AQTセンター科学ディレクター セルゲイ・P・グリゴリエフ
記事への自由なアクセスは、記事に含まれる資料の価値を決して減じるものではありません。
ほとんどの日本製製品の品質は、驚くべき生産経済性を伴って三級品から優れた品質と信頼性へと目覚ましい飛躍を遂げ、1950 年の急速な爆発に始まり、今日まで続いています。日本の品質と1950年に始まった突然のブームについては世界中の人が知っていますが、それがどのように起こったのかを理解している人はほとんどいません。
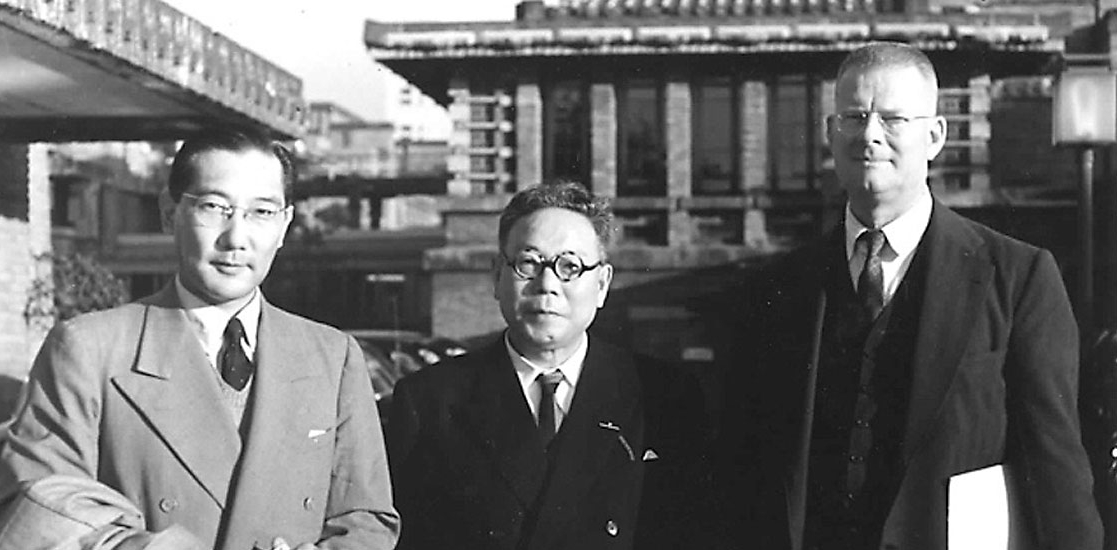
写真。 1950年代、日科技連の会員である西堀栄三郎と東京大学の森口茂一は、日本で最も権威ある経営団体である経団連が会長の石川一郎の下で主催したセッションに、W.エドワーズ・デミングを招き、統計的ビジネス手法について講義した。 JUSE会長でもある)。ソース: デミング研究所 。
日本で品質革命を可能にした管理の統計原則を 1 か所に収集することは価値があると思われます。なぜなら、これらの原則のほとんどは、現時点でもアメリカでは一般に理解されておらず、実践されていないからです。
もちろん、ここで説明した原則のいくつかの相対的な重要性は、1950 年以来長年にわたって変化してきました。ここで説明した原則の一部は、以前の原則の必然として生じました。他の結果もほぼ際限なく追加される可能性があります。
日本の質的飛躍は偶然ではありません。これは、日本の業界全体、生産のあらゆるレベル(もちろん経営陣も含む)において、統計手法を機能させるための協調的で断固とした系統的な努力の結果としての成功でした。繰り返しの訪問と、日本科学技術連盟が主催する管理者、技術者、職人向けのさまざまなレベルの講座が、これらの取り組みを導き、強化しました。おそらくこのような協調的な動きは日本でしかできないことでしょう。
明らかに、品質、均一性、経済性の問題を認識し、それらを解決する試みを評価するには、統計的手法と統計的思考が必要です。統計的手法は、入荷する材料の仕様とテストから、使用中の製品テスト、顧客調査、製品設計、再設計に至るまで、生産ラインのあらゆる段階をカバーします。だからこそ、先ほども言ったように、 ウォルター・A・シューハート , 統計的品質管理は、無駄のない製造の問題を表す最も広範な用語です。
原則1.
製造作業員が欠陥の原因について統計的に管理されている状態で製造した欠陥製品に注意を向けることは、士気を低下させ、コストがかかります。 1 。実際、彼は目隠しをされて、慎重に混ぜられた赤と白のビーズの箱から白と赤のビーズのサンプルを採取しているため、これはまったく役に立ちません。彼はサンプルや製品中にランダムに発生する赤いビーズを制御できません。彼はシステムに勝つことはできない。彼はシステム内の赤いビーズのシェアによって妨げられています。管理者のみがボックス内の赤いビーズの割合を変更できます。
詳細参照 E. デミングの赤いビーズの実験 。
実際、彼のパフォーマンスがその欠陥の原因に関して統計的に管理されているときに、欠陥のある要素に注意を向けると、彼は手順を変更しようとするでしょう...[テキスト消失]、改善を期待しても無駄です。彼の修正の結果は... [テキストが失われました] 彼の結果のバリエーションの増加 - 彼の努力を無効にする裏目に出ます。
私たちが翻訳した Donald Wheeler の記事の説明を参照してください。 許容値フィールドの正しい使用方法と誤った使用方法。不良品と良品の許容範囲に従って製品を分類する必要がありますか、それともプロセスをカスタマイズする必要がありますか?
生産労働者には自分の状況を知る権利があり、自分が生産した欠陥品を見るまでは分からないという主張は、今日のビジネススクールで教えられている管理上のよくある誤解の 1 つです。ここで説明されている誤りは、管理の最良の原則を理解していないことから生じます。
原則2.
従業員が仕事において統計的管理を達成しているにもかかわらず、質または量の点で満足のいくパフォーマンスが得られない場合は、その従業員をまったく別の仕事に異動させる方がよいでしょう。
オープンソリューションの説明を参照してください 人事モチベーション システムにおける KPI の使用についての批判的な考察。または、経営者が会社を運営するために最も重要な情報を自ら奪い、チームワークを破壊する方法 。
原則3.
仕事を統計的に管理できる状態に達していない労働者の訓練と再訓練は、その人にとって依然として効果的です。
原則4.
製品の許容範囲の上限と下限だけでは、生産作業者にとってコストがかかり満足のいく基準点とはなりません。たとえば、1.001 ~ 1.002 cm の範囲の外径公差限界は、製造作業者に直径 1.0012 cm が公差範囲内であることを伝えますが、これは、製造作業者が達成できるものとは異なり、欠陥の発生を減らし、生産性を向上させるのには役立ちません。統計的手法を使用することで労力が軽減されます。 (数年前にシューハート博士が述べた。)
私たちが翻訳した Donald Wheeler の記事の説明を参照してください。 許容値フィールドの正しい使用方法と誤った使用方法。不良品と良品の許容範囲に従って製品を分類する必要がありますか、それともプロセスをカスタマイズする必要がありますか?
原則5.
したがって、お金を節約するために、彼の職務内容では、許容範囲内で個々の要素を分布させて仕事の統計的制御を達成することが求められるはずです。このシステムの下では、高コストの詳細な検査を行わずに、彼の製品は許容範囲を満たします。統計的管理下にあるにもかかわらずパフォーマンスが満足できない労働者は、別の仕事に移され、訓練される場合があります。
原則6.
良い品質が必ずしも高品質を意味するわけではありません。これは主に、市場の要求を満たす低コストおよび品質での均一性と信頼性を意味します。
原則7.
品質特性が公称値から逸脱すると、たとえその逸脱が許容範囲内であっても損失が発生します。均一性が高まると、メーカーは一部のステップを削減したり、より安価な原材料を使用したりするなど、生産プロセスを節約しながら、仕様を満たすことができます。したがって、均質性が高まると、a) 生産者とその消費者の両方が、より大きな節約を達成できるようになります。 b) 一緒にビジネスを行うためのより良い基盤を提供する 2 。
例はたくさんありますが、あまり知られていないかもしれません。たとえば、農産物の均一性は、食品やその他の派生品を経済的に加工するためにも重要です。
詳細参照 タグチ品質損失関数 。
原則8.
混乱状態(不十分な監督、不十分な管理、統計的管理の欠如)では、生産労働者は潜在的な能力を開発し、製品の均一性と生産性を確保することができません。
シューハート管理図などの統計手法は、是正措置を必要とする不均一性の特定の原因の存在を示すシグナルを提供します。
原則9.
企業の競争力の低下を伴う生産コストの高さの理由を 2 つのカテゴリーに分類することをお勧めします。
全身的原因 (一般的または環境的原因) - 85%。
これらの障害は、管理者が修正するまでシステム内に残ります。それらを組み合わせた効果は通常、簡単に測定できます。個々の原因の中には、判断に基づいて特定できるものもあります。残りは実験的に決定できます。操作の記録や資料を調べることによってもわかります。
特別な理由 - 15%。
これらの理由は、特定のワーカーまたはマシンに固有です。シューハート管理図は、通常、作業者が特定して修正できる特別な原因の信号を検出します。
与えられたパーセンテージは、私の経験では、組織的原因が特殊な原因を上回っていることを示しているだけです。製品設計とサービステストはシステムの一部であり、管理者の責任です。
共通原因は、ワーカーのグループ全体に共通である、つまりシステムに属しているという事実からその名前が付けられています。
管理者が共通の原因に対処しなければ、システムの改善も、差異や問題の特殊な原因の軽減も起こりません。
2 つのタイプの理由を混同すると、あらゆるレベルでフラストレーションが生じ、必要とされるものとはまったく逆の、ばらつきの増大とコストの増加につながります。
原則10.
幸いなことに、この混乱はほぼ確実に解消できます。分布、プロセス フローチャート、シューハート管理図などの単純な統計手法は、すべて書籍で説明されており、作業の均一性を向上させるためにいつ行動を起こすべきかをオペレータに伝える信号を提供します。また、いつプロセスを放置すべきかも教えてくれます。
原則11.
これらの単純な統計手法により、次の 2 つの一般的なエラーのコストが最小限に抑えられます。
1. 過度な修正(過剰な規制)。特定の原因を頻繁に追求し、ばらつきや目標からの逸脱を増大させるだけの措置を講じます。
2. 特別な原因の兆候があるにもかかわらず、不作為(何もしない、または少なすぎる)。
どの間違いも完全に避けるのは簡単です。特別な理由については何もせずにエラー #1 (第 1 種) を回避することができ、その結果、できるだけ頻繁に #2 が発生します。その結果は混乱です。あるいは、上向きまたは下向きの偏差のわずかな兆候に対処することで、エラー 2 (タイプ 2) を回避できます。その結果、変動性が増大し、さらに大きな混乱が生じます。
統計的手法は、安定性を実現し、両方のエラーによる損失を最小限に抑える唯一の費用対効果の高い方法です。
本書に記載されていないこと、または品質管理エンジニアにとって不明瞭であるか、一般に知られていないことは、生産作業員に統計信号を送信する同じ管理図が、システム自体に関連する問題の全体像 (一般的な原因) を管理者に提供するということです。 3 。
Edwards Deming (Sergey P. Grigoryev) による記事の前段落の説明
シューハート管理図が、次のような変動の特別な原因の存在の証拠を示している場合 ウェスタンエレクトリックのゾーン基準 、これはプロセスの不安定な (予測不可能な) 動作を示し、「赤い」点で観察された変動は排除すべき特別な理由によるものであり、すぐに排除できない場合は管理下に置く必要があることを生産作業者に示します。ほとんどの場合、これはショップレベルで行うことができます。
同時に、不安定なプロセスの管理限界 (赤い上下の線) は、工場レベルで特殊原因を排除した後にプロセス状態が到達する可能性の最小値を示しています。これらの同じ管理限界とプロセス位置 (中央ライン、CL) は、大部分の場合のさらなる改善がプロセスの設計方法に依存しており、これは企業の能力の範囲内である場合、一般的な (体系的な) 理由による状態を示しています。トップマネジメント。しかし、体系的な変更は、変動の特定の原因が排除された後にのみ着手されるべきです。そうしないと、その有効性を評価できなくなります。
シューハート管理図がプロセスの安定した (予測可能な) 動作を示している場合、プロセスの管理限界と平均は、プロセスが既存の共通原因システムで可能な最良の状態にあることを示しています。そして、このプロセスの状態がその要件を満たしていない場合、状況を改善できるのはシステム的な変更のみであり、これは会社のトップマネジメントのみに影響を与え、現場には影響しません。プロセスが安定した状態にあるため、このプロセスが動作するシステムを改善するために行われた試みの有効性を追跡できます。
店舗スタッフに自主的に安定した工程の改善を求めることは、大小の嘘が生まれて従業員のやる気を削ぐ状況を生み出すことを意味する。そして、そのようなプロセスを改善しようとする作業スタッフによる誠実な試みは、結果をもたらすだけです。 変動性を高める それはプロセスを悪化させ、自分自身の能力への失望を引き起こすだけです。
原則12.
製造または測定プロセスを改善するための最初のステップは、1 つの主要な製品特性を統計的に制御し、次に別の製品特性を統計的に制御することです。プロセスの主要な定性的特性の統計的制御が達成されると、プロセスは次の段階である改善の準備が整います。これは管理者の責任です。
プロセスが最初に統計的管理下に置かれていない限り、一般的な原因を軽減するために講じられた措置の効果を推定しようとする試みは、危険を伴い、誤解を招くことになります。
製品の最も重要な品質特性の統計的管理が達成されたとしても、体系的(一般的な)原因は依然として残っています([ジョセフ M.] ジュラン博士が昔教えたように)。繰り返しになりますが、システム的な(一般的な)原因は管理にとって課題です。
原則13.
単に品質特性を許容範囲内に維持するだけの機械式レギュレータでは、製品の均一性が向上せず、経済的なメリットも得られません。システムは改善されません。機械式コントローラをコンピュータ装置と組み合わせて使用すると、逸脱の特定の原因が発生し、プロセスの調整が必要なときを示す信号をオペレータに提供する管理図を作成できます。
原則14。
工場がシューハート管理図を維持して、認識された問題のどのくらいの割合がシステムに起因しているのか、したがって経営者の責任に起因しているのかを示さない限り、経営者はその仕事を果たしていないことになります。
統計的手法がない場合、「品質を向上させ、コストを削減するために私たちはできる限りのことを行う」という経営陣の通常の主張は、真実ではありますが、統計的管理手法の理解と使用がなければ、単なる希望的観測にすぎません。
典型的な経営陣の発言は、「私は品質管理について十分に理解しているので、社長としてのオフィスから品質管理を効果的に管理できる」というものかもしれません。表面的な理解は問題が起こったときにのみ現れる 4 。
アメリカの経営陣は一般に、すべての生産および品質の問題の責任は生産労働者にあると想定しています。統計的手法がない場合、管理は従業員がミスをしなければ問題はないという定理に基づいて進められます。このエレガントな定理は、製品の均一性を向上させたり、無駄を減らしたりするものではありません。これはコストのかかる態度です。それは経営者の責任と能力を隠蔽し、トラブルが継続することを保証します。
誰もがよく知っている自動車の修理リコールの理由は、明らかな問題があった場合に必ず発生しますが、それは仕上がりの品質ではなく、設計やシステムの品質、したがって管理ミスに関係しています。
経営陣がシステムを改善し、生産労働者が責任を持ち、制御できるものに対してのみ責任を負わせ、システムによって割り当てられた欠陥に対して責任を負わせないようにするという真の試みを生産労働者が目にした場合、生産労働者の士気はどれほど高まるかは、いくら強調してもし過ぎることはない。
原則15.
プロセスは、統計的制御の状態にある場合にのみ、均一性と予測可能な機能を持ちます。この状態では、明日の製品の基本的な品質特性は確実に予測可能な範囲内に収まります。生産量と生産コストを予測できます。
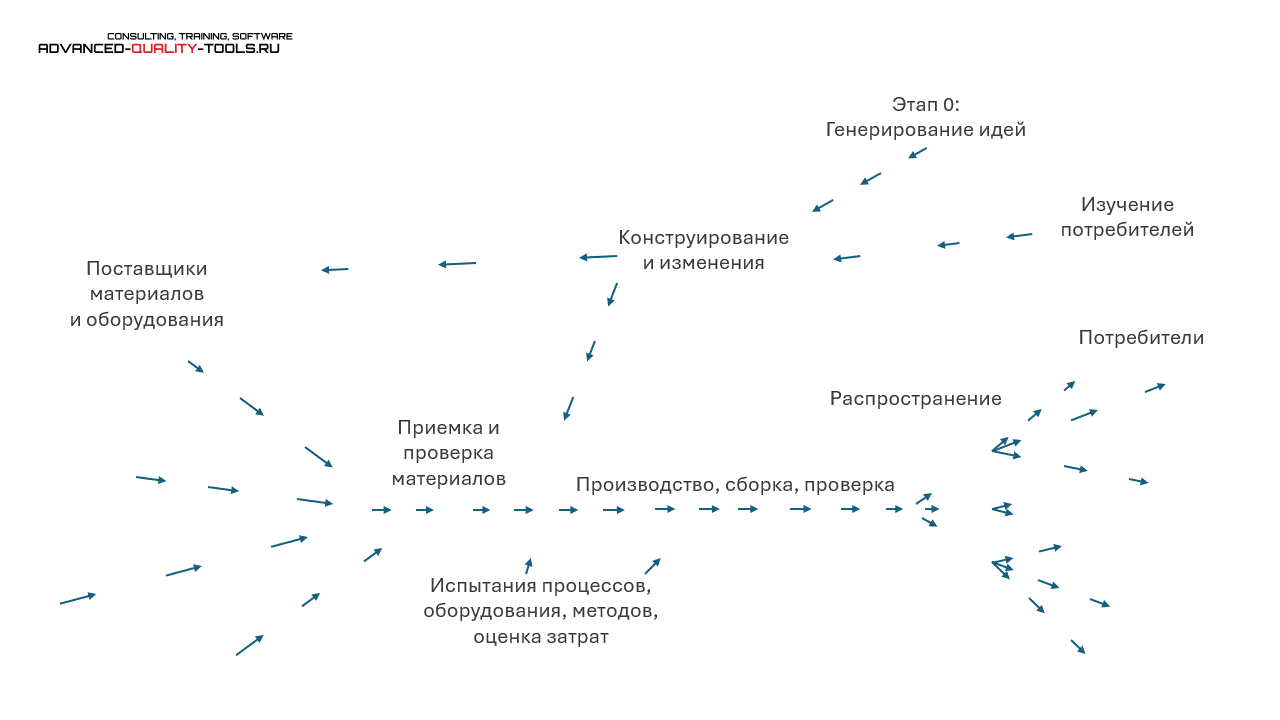
描画。設計、原材料から消費者に届くまでの生産ライン。顧客調査とサービス要件からのデータは、製品の再設計と生産投入要件の変更の基礎となります。
原則16。
消費者は生産ラインで最も重要なポイントです。消費者ニーズの調査とサービスのテストは統計的なタスクです。
原則17。
製品のパフォーマンスは、次の 3 つのコンポーネント間の相互作用の結果です。1) 製品自体。 2) ユーザーとその製品の使用方法、顧客の設置方法、手入れの方法、および使用条件 (例: 顧客がローラー ベアリングに汚れが入るのを許可した)。 3) 操作説明、顧客トレーニング、修理サービス、修理工のトレーニング、スペアパーツの入手可能性。
サービス記録が維持されている機器のメーカーは、記録を継続的に確認して、障害が 3 つのコンポーネント間でどのように分散されているか、および製品のパフォーマンスを最もコスト効率よく向上させる方法を知ることができます。
オファー:
1. 故障診断の頻度分布を顧客の種類、サービス担当者、機器の種類ごとに作成します。顧客と機器の種類間でサービス担当者をランダムに切り替えることにより、サービス担当者のトレーニングを改善するための基礎が提供されます。
2. 機器の種類に応じてお客様のご要望に応じます。その結果、どのタイプの顧客とどの利用条件が最も満足する可能性が高く、どの利用条件が不満を引き起こす可能性が最も高いかがわかります。
3. 障害の種類および機器の種類ごとに障害数の動態を監視します。
原則18。
製品が仕様要件を満たしているか満たしていないことを宣言するためのテスト基準 (技術的許容差) は、製品の性能を評価する基準とはまったく異なります。 18 。
原則19.
製品の予定通りの配達は、数日間は早く配達され、さらに数日間は配達が遅れることを示します。
この原則は、日本である日、到着する電車のホームに足を踏み入れたときに、到着予定時刻まであと 10 秒あることに気づいたときに思いつきました。 「もちろん、彼の到着率を時間どおりと定義するなら、彼は半分の時間早く到着し、半分の時間遅れなければならないでしょう。」と私は言いました。
記事の操作の説明を参照してください。
1.
運用定義
。
原則20。
製品を生産して販売する場合、経営者は次の 2 種類の問題 (課題) に直面します。 6 :
A. すでに製造された製品をどうするか。市場または特定のバイヤーに送るのに適していますか?
B. 将来の製品を改善する方法。
メーカーにとって問題 A は常に発生します。それは、今日の製品をどうするかということです。問題 B に取り組むことは投資です。タスク B の成功度に応じて、将来のタスク A が容易になります。
品質管理が問題 A から問題 B をほぼ除外して構成されていた時代がありました。最終製品を検査して欠陥のあるユニットを特定することで、良品のみが市場または特定の顧客に送られることが保証されると考えられていました。
現在では、最終製品テストをいくら行っても製品の品質を保証できないことが知られています。一部の欠陥品がすり抜けて購入者間の不評を引き起こす可能性があります。さらに、ラインの最後では、再作業や交換にかかる時間とコストの無駄を避けるために、要件を免除する必要が常にあります。検査に依存すればするほど、市場に流通する不良品の割合が増加します。
解決策は管理と追加のテストにあるという考えは、場所によっては、生成される欠陥の割合を減らすためにプロセスについて何かをする必要があるという考えに取って代わられています。
統計的承認手順は、タスク A の最優先サブタスクである必要があります。
統計的手法は、問題 B であるプロセス改善に対する費用対効果の高いアプローチも提供します。
原則21。
複数のユニットを製造してテストするコストは、市場予測と組み合わせた場合でも、製品コストを予測するための十分な情報にはなりません。また、顧客がバッチが要件に準拠しているかどうかをどのようにチェックするかを知ることも必要です。すべての部品が仕様を満たす必要がありますか? (もちろん、テストが破壊的である場合は不可能です。) それとも、クライアントは 100% のコンプライアンスを必要としない受け入れ計画を使用するのでしょうか?
原則22。
単純であろうと複雑であろうと、測定は製造プロセスです 7 。製品は測定システムを使用して得られた数値によって特徴付けられます。観察者の交換を含む統計的管理の対象にならない限り、識別可能な測定システムは存在しません。統計的管理は意見の問題ではなく、偶然に関する特定の統計的テストの遵守の問題です。
私の経験では、信頼性の低い機器や測定値は、製造における多くの問題や紛争の原因となります。商品が不良品だったのでしょうか、それとも測定値が間違っていたのでしょうか?
すべての製造業者は、自社の測定結果と顧客が取得した測定結果との差異に関連する課題に日々直面しています。彼の標準的な測定値と試薬と、彼のクライアントの標準的な測定値と試薬の間。
食品製造業者なら誰でも、すでに流通している、または流通の準備ができている製品が、偽陽性の検査結果により少なくとも一時的に欠陥があることが判明し、後に自社の研究室での汚染が判明したという恐ろしい経験を思い出すことができるでしょう。
原則23。
製造における適切な注意を運用上定義することはできません。したがって、製造における適切な注意の要件は、法的に強制することができません。ただし、生産における注意は定義して測定することができます。ケアの証拠は、意味のあるデータ (グラフや統計計算の形式をとる場合もあります) の形式でのテストの記録によって提供され、是正措置と結果の記録によって補足されます。製品の使用説明書と誤用に関する警告は、メーカー側のある程度の注意を示すプロトコルの一部です。
記事の操作の説明を参照してください。
1.
運用上の定義
。
原則24。
会計期間中に最高の業績(最高の売上、最小の欠陥、最高の生産)を達成した製造従業員または従業員グループに、いわゆる功労賞を与える慣行は、その賞が満足のいく統計的測定に基づいていない限り、士気をくじく可能性があります。それが良いパフォーマンスと単純な運を区別します。賞が業績の統計的尺度に基づいていない場合、その賞システムは単なる宝くじになります。私の知る限り、宝くじは宝くじと言われれば何も問題はありませんが、宝くじはメリットと言われると大きな害を及ぼす可能性があります。その結果、生産性の低下、品質の低下、仕事への不満が生じます。幸運と功績を混同すると高くつく。
当社 Web サイトの記事の説明を参照してください。
1.
幸運と成功を混同しないでください
;
2.
システム内の報告期間の結果に基づく会社員の賞与や減価償却は、宝くじに当たったらご褒美を与えたり、負けたら罰を与えたりするのと同じです。
。
原則25。
統計的手法は企業や政府機関では導入されていません。統計的手法は知識と経験から生まれます。統計理論の知識は基礎となります。従わなければならない保証された料理本レシピはありません。
リンク
1. 原則 1 ~ 17 については、私の記事「経済生産への統計的援助について」(Interfaces、Vol. 2、2014)で詳しく説明されています。 5、No.4、1975年8月:p. 1~15; 「日本の品質管理に関する私の見解」統計応用研究報告書、vol. 2 にも記載されています。 22、No.2、1975年6月:p. 73~80。
2. スミス、リチャード D.「Rescuing Superfoods」、The Sciences、Vol. 16、1976: p. 13〜18。
3. たとえば、W. エドワーズ デミング、「経済生産への統計的援助について」、Interfaces、vol. 2 を参照してください。 1975 年 8 月 5 日: 1 ~ 15 ページ。
4. ウィリアム・ゴロムスキー。 「部門の規模」、『品質の進歩』、1976 年 8 月、p. 13.
5. この原則は、もちろん 1944 年にハロルド F. ドッジによって常に強調されていました。
6. この原則は、1942 年にベル電話研究所のジョージ エドワーズによって策定されました。その貢献は、米国試験材料協会の E-11 委員会の委員長としての長年の勤務中に、受け入れサンプリングに貢献したためです。
7. シューハート、ウォルター A. 「品質管理の観点から見た統計的手法」 、ワシントン州農学部大学院、1939年。 110–119ページ。 (シューハート、ウォルター A.「品質管理の観点から見た統計的方法」、農務省大学院、ワシントン、1939 年;110-119 ページ)。
ク、ハリー H. 「精密測定と校正」 、ワシントン国立標準局、vol. 1、Publication 300、1969年。(Koo、Harry H.「Precision Measurement and Calibration」、ワシントン国立標準局、Vol. 1、Publication 300、1969年)。
キャメロン、ジョセフ M. 「測定保証」 、ワシントン州国家標準局、Bulletin no. NBSIR 77.1240、1977 年。 (キャメロン、ジョセフ M.「測定保証」、ワシントン州国家標準局、会報番号 NBSIR 77.1240、1977 年)。